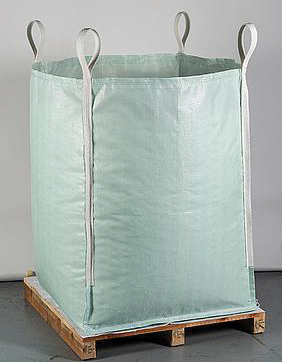
Sacs industriels : mieux transporter et recycler
publié le dimanche 30 octobre 2022
Abonnez-vous à la revue pour lire la suite de l'article
s'abonner
Eléments essentiels de la chaine logistique des produits vracs à écoulement libre, les big bags ou
Grands Récipients Vrac Souple (GRVS) sont appréciés pour leur légèreté et leur rapport coût/qualité. Majoritairement en PP, ils séduisent par une empreinte carbone plus faible qu’un contenant rigide de type fût. Avec comme bémol : un usage qui reste unique pour 75% des big bags commercialisés, leur élimination se faisant en décharge ou par incinération. Le secteur travaille donc à organiser leur recyclage en instaurant des boucles fermées ou à réduire leur empreinte environnementale en développant des systèmes de remplissage des big bags plus performants.
Starlinger recycle les sacs industriels dans une logique de boucle fermée
Pour inscrire le big bag dans une économie circulaire, le fabricant de big bags par extrusion et tissage Starlingera développé un schéma complet de recyclage tout au long du cycle de vie du sac : fabrication, utilisation, récupération et lavage. Pour faciliter leur recyclage, la société a adapté dans un premier temps leur couture, en les équipant d’une doublure en PE facilement amovible et d’étiquettes d’information, ainsi que d’un passeport matière, dans lequel chaque étape du cycle de vie du big bag y est consignée. Un suivi nécessaire pour garantir un flux de matériaux homogène et une bonne qualité du matériau recyclé.
Pour assurer un recyclage de qualité des sacs en PP, le retour des big bags au remplisseur est réalisé lors d’une collecte séparée afin de garantir un PP le moins contaminé possible. Une garantie supplémentaire de non contamination avec d’autres plastiques et qu’ils ne soient pas orientés dans le flux de post-consommation. Starlinger collecte ces big bags et les prépare avant d’être broyés, lavés, puis transformés en rPPsur une ligne de recyclage interne à Starlinger afin d’y être à nouveau intégré dans le procédé d’extrusion à hauteur de 50%. La fabrication des sacs est réalisée sans fil multi-filament de polyester pour la couture et en utilisant des doublures et des étiquettes d’information en PE facilement amovibles, ce qui fait du nouveau big bag un emballage facile à recycler. Ces derniers offrent les mêmes caractéristiques de résistance à la traction, de poids et de protection qu’un sac fabriqué à partir de PP vierge.
Autre alternative développée, la conception de sacs à partir de bandes de PET. Outre sa grande résistance et sa stabilité de forme, le PET peut être aussi recyclé et traité. «Grâce à une méthode appelée polycondensation à l’état solide (SSP), le poids moléculaire du PET recyclé peut être rétabli à son niveau d’origine, ce qui permet d’obtenir un matériau qui est littéralement «comme neuf», même après avoir été recyclé de nombreuses fois. Et de l’intégrer jusqu’à 100% dans nos sacs», indique Starlinger. Le fabricant propose d’ailleurs grâce à ce procédé du rPET de qualité alimentaire, approuvé par la FDA et l’EFSA, pour ouvrir le champ d’applications possibles aux big bags.
Pour Starlinger, les deux approches PP et PET sont complémentaires. La technologie d’utilisation du rPP dans la production de big bags suscite autant d’intérêt que la solution PET, les premières lignes de production de tissu ruban PET pour la production de big bags ayant débuté cet été.
Adivalor organise la première unité française de recyclage des big-bags agricoles Adivalor et la société Novus officialisent leur partenariat pour la création d’une nouvelle usine de recyclage de big-bags agricoles.
La nouvelle unité démarrera sa production en juin 2023, avec une capacité de matière plastique recyclée (MPR) pouvant atteindre 10 000 tonnes par an en 2024. Implantée en Normandie dans la région de Gisors (27), la nouvelle unité de production de Novus sera une première en France pour le recyclage de GRVS. Les processus utilisés par l’usine de matières plastiques recyclées à base de polypropylène et de polyéthylène basse densité ont été préalablement testés en usine pilote : la MPR est de haute qualité, elle pourra être incorporée dans la fabrication d’emballages neufs, en substitution de matière plastique vierge. Le projet a demandé un investissement de 10 millions d’euros. Pour Luc Letierce, président de Novus : «ce projet s’inscrit dans notre stratégie d’investir dans des activités nouvelles, qui contribuent à rendre plus durable l’usage des intrants agricoles, notamment les engrais conditionnés. Ce partenariat montre à quel point le monde agricole est un acteur pionnier de l’économie circulaire». Adivalor assurera la majorité de l’approvisionnement de l’usine Novus en big-bags, grâce à la performance du programme français de collecte de ces emballages, utilisés pour le transport et le stockage des engrais et des semences. «Cet accord consolide notre engagement de recycler 100% de ce type d’emballage et illustre concrètement notre volonté de localiser en France le maximum de capacité de recyclage», ajoute Ronan Vanot, directeur général d’Adivalor. 9 300 tonnes de big-bags ont été collectées en 2021, recyclés à 100% par des recycleurs localisés en Pologne, Espagne et Italie. L’éco-organisme a pour objectif de garder ces performances de collecte et de recyclage, tout en les localisant au plus proche des agriculteurs, selon la feuille de route établie avec ses actionnaires. Ce projet est soutenu par les metteurs en marché d’engrais et de semences certifiés, représentés respectivement par la société Soveea et l’association Ares, actionnaires d’Adivalor. Le projet bénéficie également des financements et d’un prêt de la BPI3 dans le cadre du plan «France Relance».
Greif-Velox remplit les big bags sous vide pour un process zéro poussière
Le nouveau système VeloVac-XL de Greif-Veloxpermet un ensachage propre et compact de poudres ultralégères grâce à une technologie de vide innovante. Les poudres sont remplies dans une chambre à vide complètement étanche avec une taille de grain inférieure à 200 micromètres et une densité apparente de 10 à 450 grammes par litre. Contrairement aux systèmes d’emballage par pompe, le VeloVac XL génère un vide atmosphérique, aspirant le produit directement dans le GRVS sans déversement. Toute poussière qui s’échappe est automatiquement extraite et réinjectée directement dans le processus d’ensachage.
Cette méthode d’ensachage propre à très faible teneur en poussières permet aux utilisateurs de réduire considérablement les coûts des travaux de nettoyage coûteux et intensifs autour du système, tout en assurant la sécurité et santé des opérateurs.
Autre avantage : les sacs sont compactés jusqu’à 400% avec le VeloVac XL, ce qui réduit considérablement les coûts de stockage et de logistique par rapport aux systèmes traditionnels d’ensachage par pompe, libérant ainsi de l’espace et du budget pour d’autres produits et projets.
L’utilisation de GRVS peut également minimiser les déchets et les temps d’arrêt : Comparé aux sacs à valve de 7,5 kg, le VeloVac XL permet aux utilisateurs de remplir des quantités jusqu’à 66 fois plus importantes dans un GRVS (Grand Récipient Vrac Souple). La manutention devient également plus simple et plus efficace pour les clients finaux – les sacs plus grands sont traités et vidés plus rapidement et utiliser moins de sacs signifie dépenser jusqu’à 30% de moins en emballage. De conception modulaire autorisant plusieurs niveaux d’automatisation, VeloVac XL se distingue enfin par ses performances élevées en fonction de la configuration et des propriétés du produit, le système peut remplir de quatre à dix GRVS par heure dans toutes les tailles de sacs souhaitées, avec un poids de remplissage pouvant atteindre 500 kg.