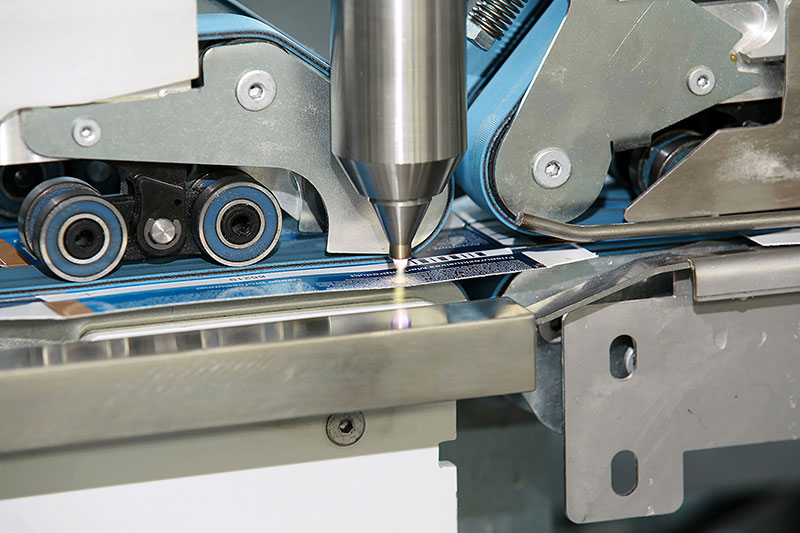
Plasmatreat développe un traitement de surface automatisé pour emballages en carton et boîtes pliantes
publié le vendredi 05 juillet 2024
Plasmatreat a présenté sur le dernier salon Drupa à Düsseldorf une nouvelle application de sa technologie plasma adaptée à l’industrie de l’emballage et de l’impression. Le procédé permet le prétraitement des emballages en carton et des boîtes pliantes avant le collage et l’impression.
Le collage et l’impression de boîtes pliantes déjà finies (avec vernis UV ou laminage d’un film) revêtent une importance particulière dans les processus industriels. En effet, aujourd’hui les boîtes pliantes et les emballages en carton modernes sont produits avec des feuilles imprimées, affinées, coupées et pliées en feuilles ou en rouleau dans une plieuse, avant d’être pré-collées par le fabricant. Cette opération est accomplie par des encolleuses de haute performance avec des vitesses allant jusqu’à 600 m/mn. L’utilisation d’adhésifs à froid permet sans problème une adhérence directe sur les cartons sans vernissage. Cependant, si le produit a déjà des finitions spéciales telles qu’un vernis ou un film laminé, les zones qui doivent être ensuite collées (comme la couture longitudinale ou le rabat inférieur) ou imprimées ultérieurement (par exemple pour le remplissage ou les dates de péremption) nécessitent un traitement préalable pour être rendues rugueuses en utilisant un processus complexe mécanique dans des machines séparées par fraisage, meulage ou brossage. Dans le cas contraire, ces endroits doivent être masqués à grands frais dans le scellage lors du processus de finition.
L’intégration d’un système automatisé Openair-Plasma® simplifie considérablement ce processus car les buses de plasma sont installées directement dans la machine encolleuse et donc intégrées directement dans les lignes de production. Les boîtes pliantes et les cartons d’emballage sont ainsi prétraités directement et à grande vitesse au cours du processus de fabrication dans les zones qui doivent être imprimées individuellement ou ultérieurement, ou encore dans les zones de joints adhésifs et des coutures collées. Les autres procédés sont donc remplacés par le système plasma. Ainsi, l’augmentation de la tension de surface est suffisante pour augmenter considérablement la capacité d’adhérence, la colle à froid qui est généralement utilisée adhère sans problème indépendamment du laquage et de l´étanchéité de la surface.
Par ailleurs, en combinant le procédé Openair-Plasma® avec l’Unité de Contrôle du Plasma (PCU – Plasma Control Unit) de Plasmatreat, une fiabilité et une reproductibilité élevées du processus de traitement peuvent également être assurées pour les lots suivants. En effet, dans la PCU, l’utilisateur dispose de plusieurs modules d’assurance qualité spécifiquement adaptés au traitement au plasma, tels que le module de puissance plasma (PPM), qui enregistre les valeurs de courant et de tension directement au niveau de la tête de la buse. Le module de contrôle de la lumière (LCM) surveille en permanence la génération de plasma. En outre, le module de contrôle de débit (FCM) ajuste en permanence le débit du gaz de procédé aux conditions du process. Ainsi, non seulement les données de production, mais également les données de maintenance prédictive sont enregistrées en continu, garantissant ainsi une production fluide et reproductible. Plasmatreat peut ainsi garantir que chaque composant d’un processus est traité avec la même intensité de plasma et que la même qualité est obtenue sur toutes les lignes de production. De plus, par rapport à d’autres méthodes de prétraitement telles que le traitement à la flamme ou les promoteurs d’adhésion, les fabricants peuvent réduire considérablement leur empreinte carbone en utilisant la technologie plasma qui nécessite généralement uniquement de l’air comprimé et de l’électricité à la génération du plasma.
Plasmatreat a profité de la Drupa 2024 pour faire découvrir en direct l’application de prétraitement Openair-Plasma® sur des emballages en carton et des boîtes pliantes ainsi que l’impression ultérieure d’un QR code sur une petite boîte pliante pour sucettes, finie avec un vernis UV. D’un point de vue technique, ce système, développé avec le fournisseur néerlandais de solutions jet d’encre DJM, utilise la matrice à fente large des buses plasma PFW70 et PFW100 de Plasmatreat pour les applications larges ou sur toute la surface. Les buses PFW70 et PFW100 assurent un prétraitement uniforme sur une largeur de 70 à 100 mm par buse plasma à des vitesses relatives allant jusqu’à 200 m/min. La disposition modulaire de plusieurs buses offre en effet une flexibilité en termes de largeur et de vitesse de traitement.