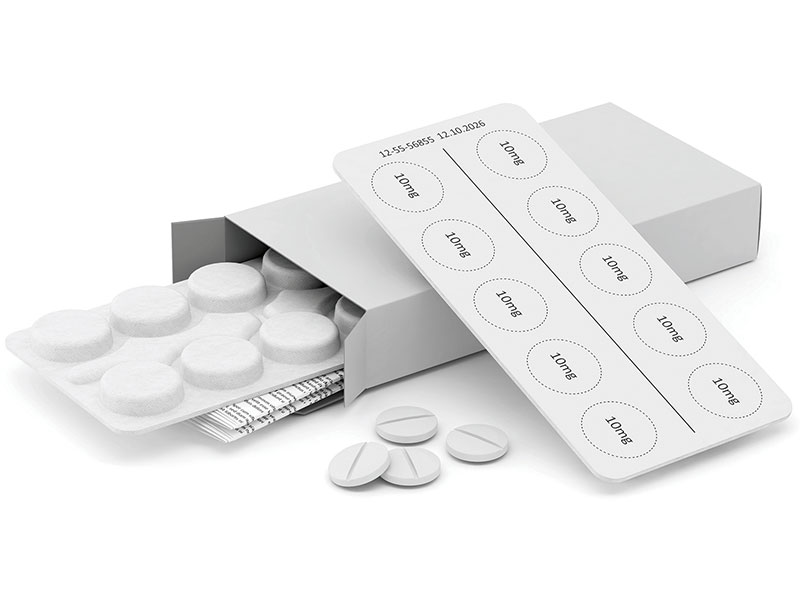
Blisters : en quête d’une alternative durable
publié le samedi 31 août 2024
Abonnez-vous à la revue pour lire la suite de l'article
s'abonner
Au fil des années, les Contract Drug Development and Manufacturing Organizations (CDMOs) tels que Delpharm, Unither Pharma, Skyepharma ou encore Biose Industrie, sont devenus des partenaires clés du développement des laboratoires pharmaceutiques et sociétés biotech sur un marché mondial qui croît de 6,74% par an, estimé à 330 milliards de dollars en 2029 (Modor Intelligence). Ces acteurs, qui affichent une forte empreinte industrielle européenne, veulent croire en la nouvelle donne qui se dessine en faveur de la souveraineté sanitaire et de la reconquête d’un leadership industriel français. La priorité est aujourd’hui donnée au développement de nouvelles capacités pour répondre aux besoins, à la spécialisation pour se différencier et, dans l’ensemble, à un accompagnement élargi de l’innovation jusqu’au conditionnement et l’industrialisation du médicament.
La durabilité est au cœur de la conception des futurs blisters pharmaceutiques pour répondre aux défis du recyclage ou de la réutilisation. Parmi les initiatives actuelles, la Blister Pack Collective, initiée par PulPac et PA Consulting, vise à promouvoir la technologie de fibres moulées du fabricant suédois et les collaborations avec les industriels (notamment Haleon, Sanofi et Bayer Consumer Healthcare) afin de réduire considérablement le recours au PVC et à l’aluminium dans les plaquettes de comprimés pharmaceutiques en accès libre (OTC), les nutraceutiques et cosmétiques. Papacks travaille également dans ce sens au sein de l’Association européenne des producteurs de pâte moulée (EMPPA), tandis que Liveo Research met en avant ses blisters mono-matériaux circulaires. En France, Adelphe prépare un guide sur le blister éco-conçu pour début 2025.
Le secteur de la santé qui regroupe les médicaments, compléments alimentaires et dispositifs médicaux, représente à lui tout seul près de 80 000 tonnes d’emballages ménagers, selon Adelphe. Parmi ces emballages, il y a le blister pharmaceutique, composé d’une coque en PVC et d’un film aluminium, qui ne bénéficie pas de filière de recyclage. Et pourtant, la loi anti-gaspillage en faveur de l’économie circulaire (AGEC) prévoit que tous les matériaux y soient intégrés au plus tard le 1er janvier 2030. D’ici cinq ans également, la stratégie de décarbonisation menée à un niveau européen vise à atteindre 55% de réduction des gaz à effet de serre et mettre en place les leviers nécessaires à la réalisation d’une production décarbonée, différenciée et compétitive.
Développements sur la pulpe moulée « à un stade avancé »
Au niveau des emballages, un axe de développement stratégique pour la filière est de remplacer le blister traditionnel PVC/Alu par des plaquettes thermoformées à partir de matières premières renouvelables, en particulier de pâtes moulées dérivées de fibres fraîches durables, pour remplacer les blisters traditionnels à base de plastique et d’aluminium, et ainsi réduire leur impact environnemental dans le sens d’une économie circulaire. Ces perspectives se situent aujourd’hui à «un stade avancé de développement», selon Tahsin Dag, pdg de Papacks et président de l’Association européenne des producteurs de pâte moulée (EMPPA). «Les applications d’emballages blisters en pâte moulée sont appelées à se multiplier au fur et à mesure que les industries pharmaceutiques et cosmétiques vont accorder la priorité à la durabilité, indique-t-il. La demande est motivée à la fois par des pressions réglementaires mais aussi par la demande des consommateurs pour des produits respectueux de l’environnement». Pionnier en matière de durabilité, Papacks apporte sa pierre à l’édifice des progrès
récents avec le développement de sa technologie propriétaire Papacks® Plant-Based Coating, un revêtement à base de plantes et sans plastique, qui offre des propriétés barrières essentielles telles que la résistance aux graisses, à l’oxygène et à la vapeur d’eau. «Nous avons également remplacé la feuille aluminium traditionnelle de scellage par un papier étanche pour que nos plaquettes thermoformées soient entièrement renouvelables», note-t-il. Un point d’attention a été de certifier les matières FSC® et que les processus de production soient alimentés par de l’énergie verte. «Bien que nos produits ne soient pas encore disponibles sur le marché, nous avons la capacité de produire plus de 100 millions d’unités de plaquettes thermoformées grâce à nos unités fonctionnelles, dès que la demande affluera», ajoute-t-il. Un facteur d’accélération pourrait être le partenariat signé en juin, avec Bayer Consumer Healthcare, pour rendre ses emballages de médicaments de santé publique (Aspirine, Bépanthène, Claritin, …) 100% recyclables ou réutilisables à l’horizon 2030. «Nous espérons que ce partenariat permettra de faire évoluer les normes mondiales dans l’industrie», commente Tahsin Dag, qui précise les prochaines étapes et défis associés pour Papacks : lancer ses produits blisters en pâte moulée sur le marché, assurer de leur conformité réglementaire, collaborer avec des leaders industriels pour promouvoir une adoption généralisée, et mener des campagnes de sensibilisation auprès des consommateurs sur les avantages des solutions d’emballages durables.
Une initiative conjointe pour réduire les plastiques à usage unique
Pour accélérer la transition vers des blisters plus durables et contribuer à la résolution d’un défi mondial, le fabricant suédois PulPac et PA Consulting ont lancé l’initiative conjointe Blister Pack Collective, qui rassemble notamment les branches santé grand public de Haleon, Sanofi (depuis février dernier) et Bayer (octobre dernier). Objectif : développer et industrialiser l’emballage à base de matériaux de pâtes durables et renouvelables, qui permette de remplacer en toute sécurité et réduire l’utilisation des plastiques difficiles à recycler et à usage unique dans les plaquettes thermoformées. «Nous travaillons aujourd’hui sur des multiples applications avec nos clients, qui vont des recharges dans la beauté jusqu’aux blisters de comprimés pour les médicaments, en passant par les compacts de maquillage et les flacons de crème hydratante», présente Jamie Stone, expert en conception et innovation chez PA Consulting. Une large gamme de produits peut être fabriquée à partir de fibres moulées à sec et chaque partenaire apporte son expertise : PA Consulting dans le conseil en innovation et PulPac avec sa technologie innovante de fibres moulées sèches (ou Dry Molded Fiber), qui se présente comme une alternative viable, durable et adaptable aux emballages en plastique à usage unique. Il y a des produits «plus faciles» à convertir en fibres moulées à secs, tels que les couvercles, plateaux, couverts, etc. déjà développés et prêts à être commercialisés. «Dans le cas des flacons et des blisters, c’est un peu plus complexe, indique-t-il. Les produits de santé ont des exigences élevées en matière de barrières entre l’humidité et l’oxygène. Mais le matériau et le processus de fabrication de la fibre moulée à sec sont compatibles avec une large gamme de revêtements et de films, qui peuvent répondre aux exigences barrière spécifiques des produits». Chaque nouveau développement d’emballage vise à donc trouver l’équilibre entre les exigences du produit, de son utilisation et le profil de durabilité souhaité, qu’il s’agisse de réduire l’empreinte environnementale globale, diminuer ou éliminer le contenu en plastique, abandonner les matériaux difficiles à recycler et/ou augmenter la recyclabilité.
Dans ce sens, la technologie
Dry Molded Fiber de PulPac présente de nombreux avantages : elle minimise les émissions de CO2 (avec une empreinte jusqu’à 80% inférieure à celle du plastique et de la fibre moulée humide) et nécessite une consommation d’eau minimale. Elle permet la production de plaquettes de comprimés polyvalentes, comparable à celles en PVC, en termes de conception et de nombre de comprimés. «Le processus ouvre surtout la voie à une production de masse à grande vitesse et à faible coût», indique-t-il. Bien que chaque produit ait ses exigences, le collectif prévoit que les premiers emballages en fibres moulées à sec permettront une réduction de 90 à 95% du plastique par rapport aux emballages blisters actuels et que, pour certaines applications, des emballages 100% papiers seront possibles.
L’axe des blisters mono-matériaux
Dans le cadre de son initiative «Réduire les déchets», le fabricant de films Liveo Research participe également à construire un monde plus durable à partir de ses blisters mono-matériaux ou circulaires, One Material Blister (OMB). L’idée est d’avoir des films blisters et d’operculage d’un seul et même matériau pour être facilement recyclés dans le flux de déchets actuel et réutilisés. «Aujourd’hui, nous offrons des solutions en PP et APET», indique Joerg Hoepfner, responsable des solutions marketing chez Liveo Research. Le fabricant applique également son concept de blisters mono-matériaux aux «nutraceutiques», c’est-à-dire aux vitamines, minéraux et probiotiques. Pour ces applications, l’entreprise propose la solution «Recyform MA», dans laquelle le film de base et le film d’operculage sont en APET. «Le film de base contient également entre 30 à 50% de produits recyclés post-consommation (PCR), précise-t-il. En fin de vie, les deux films sont fondus ensemble pour créer un nouveau film de base avec une teneur PCR plus faible». Le développement de blisters circulaires est l’axe central des travaux de Liveao Research dans ses laboratoires. «Nous réalisons de nombreux tests sur les machines de conditionnement sous blisters de nos clients. Ce qui constitue des ressources intéressantes pour nos nouveaux et futurs développements de produits», conclut Joerg Hoepfner.