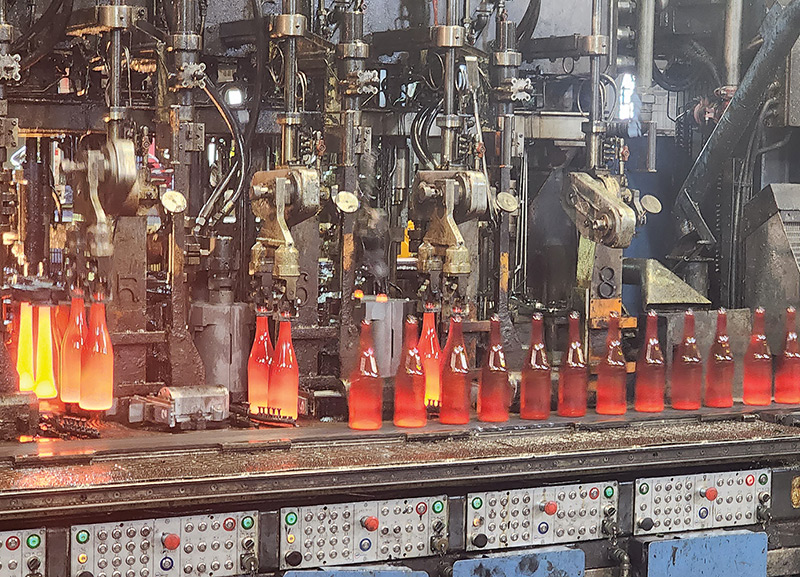
A Béziers, O-I Glass promeut la décarbonation
publié le samedi 30 novembre 2024
Abonnez-vous à la revue pour lire la suite de l'article
s'abonner
Directement alimentée par un convoyeur en calcin par le site de tri et de traitement Maltha, la verrerie de Béziers du groupe O-I Glass se veut la vitrine d’un modèle vertueux du verre, recyclable en boucle fermée. Réduction de la consommation énergétique et allégement des bouteilles sont également au cœur des axes stratégiques de décarbonation du groupe, dont l’objectif est de réduire de 25% ses émissions CO2 d’ici 2030.
Rénové en 2016, le four de l’usine d’O-I Glass à Béziers dans l’Hérault – installé sur un site de 32 Ha – fournit 140 000 tonnes de verre par an. Plus de 60 modèles de bouteilles entre 37,5 cl et
150 cl y sont ainsi fabriqués à destination du secteur des boissons par une équipe de 87 salariés. Le four alimente trois lignes dédiées à la production de grands standards de vins, spiritueux et pétillants. «Nous approvisionnons ainsi de petits domaines viticoles jusqu’aux grands comptes dans un rayon de 200 km pour une empreinte carbone réduite sur le plan logistique», explique Olivier Guillot, directeur de l’usine O-I Glass de Béziers.
Le calcin au cœur du modèle verrier d’O-I Glass
Dans son process de fabrication, l’équipe de Béziers intègre 89% de calcin – verre recyclé – mélangé à du sable, de la soude et différents additifs, porté entre 1300 et 1400°C dans son four. On estime ainsi que pour une tonne de calcin introduite, les émissions carbone sont réduites de 500 g. Soit par tranche de 10% de calcin, 2,5% de CO2 et 5% d’énergie économisés. Pour alimenter son four en calcin, O-I Glass a mis en place un partenariat avec Malthadans le cadre d’une joint-venture avec Renewi. Le centre de tri et de recyclage, situé à quelques pas de la verrerie, tourne en 3×8, 5/7j pour traiter 850 tonnes de verre brut par jour. Un convoyeur automatique, installé entre les deux sites, alimente O-I Glass en calcin et poudre de verre à hauteur de 600 tonnes par jour. «Notre usine est alimentée en déchets de verre, que nous envoient les collectivités aux alentours. Nous réalisons plusieurs étapes de tri, manuels ou automatisés, pour supprimer toute impuretés comme la céramique, la pierre ou la porcelaine, les plus grands ennemis des verriers. Deux types de calcin sont obtenus en sortie de process : le mixte et le blanc», explique Stéphane Revuz, directeur de l’usine Maltha Béziers. La pureté – fixée à 30 ppm/tonne à la sortie – garantit un retour au contact alimentaire du verre recyclé. Pour accompagner sa croissance, Maltha prévoit d’investir dans un nouveau bâtiment de stockage prévu d’ici la fin 2026.
Alléger les bouteilles
Autre axe stratégique déployé par O-I, celui de l’allégement des bouteilles. Un million d’euros a été investi sur le site de Béziers en 2023 pour adapter une des lignes en production en verre allégé de teinte verte ou feuille morte. En passant d’un poids de 410 à 360 g, les bouteilles de vin ainsi produites dans la verrerie affichent une économie de 12% des émissions carbone. «Tout le défi technique a consisté à ajuster le process industriel pour obtenir une bouteille qui soit à la fois légère, esthétique et résistante», détaille Yann Berton, responsable de production. Lancée en juin 2024, cette version allégée a déjà séduit 22 clients. Quelques mois plus tôt, le verrier avait annoncé en marge du salon Vinexpo, le lancement d’Estampe, première bouteille 75 cl éco-conçue fabriquée par l’usine de Labégude, dont l’empreinte carbone et la démarche pour atteindre la neutralité carbone ont fait l’objet d’une validation par le cabinet de conseil en climat The Carbon Trust. Avec un poids de 390 g et l’utilisation à 82% de verre recyclé dans sa fabrication, la bouteille Estampe obtient une empreinte carbone de seulement 249 g d’équivalent CO2, soit 25% d’émissions carbone en moins par rapport aux bouteilles classiques de 500 g. Des performances qui peuvent encore être optimisées par la dématérialisation de la capsule de surbouchage, l’adoption d’un bouchon de liège et d’une étiquette en papier. L’empreinte résiduelle est compensée par l’achat de crédits carbone, notamment avec la plantation de vergers en France et le financement d’un projet de reforestation au Brésil.
Autres axes de décarbonation
Outre l’intégration de calcin et l’allégement des bouteilles, d’autres voies sont explorées pour réduire l’empreinte carbone du groupe verrier : approvisionnement en énergies renouvelables, diminution de la consommation énergétique sur les fours et les canaux de distribution, récupération de chaleur, etc. Equipée d’une station de traitement des eaux ainsi que d’un filtre de recyclage des poussières, l’usine de Béziers bénéficie d’une installation de panneaux photovoltaïques de 10 000 m² et d’une centrale produisant 1,7 GWh/an soit l’équivalent d’une consommation de 2000 foyers. Alimenté en gaz, le four fonctionne en continu depuis 15 ans, le process de fusion ayant besoin de stabilité. «Lorsqu’il arrivera en fin de vie, se posera la question de basculer sur un autre mix énergétique pour réduire encore notre empreinte. De par sa forte capacité (410 tonnes), il sera impossible de le passer en 100% électrique. Il faudra s’orienter très certainement vers une solution hybride», explique Olivier Guillot. L’investissement est hautement stratégique puisque le coût d’un nouveau four à lui seul avoisine une moyenne de 60 M€.
Automatiser pour gagner en performance
Depuis la cabine de contrôle conçue pour une vision 180°C, les opérateurs peuvent surveiller les trois lignes de production en simultané, sortant les bouteilles à une cadence de 140 par minute. Une fois acheminées dans la zone froide, s’entame un contrôle minutieux de chaque article sur la base de
40 critères. Statistique tout d’abord par un opérateur puis systématique par une série de plusieurs modules équipés de caméras venant s’assurer de la conformité des bouteilles : contrôle du fond, de la bague, de l’étanchéité, d’un trop plein de matière dans le col, de défauts de structure avec risques de casse, etc. Toutes les bouteilles avec des imperfections sont éjectées pour être refondues et éviter toute perte de matière. Les produits conformes partent vers une cellule de palettisation automatisée pour être rassemblés par rang et couche sur une palette, étiquetée et habillée par une housse rétractable totalement étanche (film de 100 microns) avec d’être envoyée vers la zone de stockage. Un espace de stockage dont 98% couvert permet le stockage de 45 000 palettes avant leur expédition.