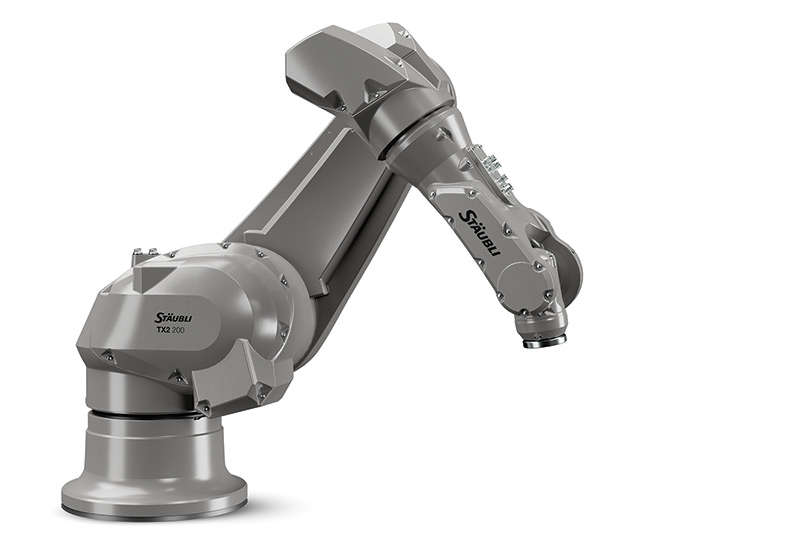
Des robots toujours plus simples à mettre en œuvre
publié le mardi 25 février 2025
Abonnez-vous à la revue pour lire la suite de l'article
s'abonner
Interfaces de programmation sans code, applications standardisées « prêtes à l’emploi », intégration d’intelligence artificielle… : les fournisseurs de systèmes robotiques mettent tout en œuvre pour faciliter la prise en main de leurs produits.
« Il n’y a jamais eu autant de robots exposés sur les stands des salons dédiés aux industries agroalimentaires qu’en 2024 !», se félicite Jacques Dupenloup, directeur de la division robotique de Stäubli en France. Bien qu’elle ne reflète pas forcément l’état général du marché français de la robotique – en retrait en 2023 par rapport aux deux années précédentes –, cette observation illustre en tout cas l’appétence des IAA pour la robotique industrielle et collaborative. «En attendant la consolidation des chiffres de 2024, on peut déjà dire que les industries agroalimentaires, qui déploient environ 400 robots chaque année en France, ont été proportionnellement plus demandeuses que la plupart des autres secteurs l’année dernière». Et Jacques Dupenloup de citer la pénibilité des opérations dans certaines usines – avec les difficultés de recrutement qui en découlent – ainsi que la recherche de compétitivité comme principales explications à ce dynamisme.
Pour servir les IAA, Stäubli s’appuie sur une offre forte d’à peu près 80 modèles parmi lesquels une quinzaine de robots (du quatre axes au six axes) dédiés aux environnements les plus exigeants de ce secteur. «Le respect des contraintes est assuré par le biais des options : utilisation d’huile alimentaire dans les réducteurs, compatibilité des pièces avec les produits et procédés de nettoyage, suivi des règles de conception hygiénique…».
Programmation intuitive
Même si elle ne figure pas parmi les applications les plus «spectaculaires», la palettisation est, d’après la profession, l’une des plus pourvoyeuses de projets en ce moment. Un constat qui a logiquement conduit Stäubli à étendre sa gamme de bras robotisés six axes vers les fortes charges avec le lancement du TX2-200 (170 kg admissibles, jusqu’à 2609 mm de rayon d’action). «Ce robot industriel, capable si besoin de travailler en mode collaboratif, existe en version HE (Humid Environment) pour les environnements difficiles : criées par exemple. Il se caractérise également par une consommation d’énergie réduite (-10% par rapport à la génération précédente en fonctionnement, -40% en veille), notamment grâce à l’intégration du nouveau contrôleur CS9», ajoute Jacques Dupenloup. Un contrôleur qui rend en outre les robots quatre ou six axes qui en sont équipés encore plus attractifs du point de vue de la mise en œuvre grâce à la nouvelle interface de programmation graphique VAL Blocks. Avec cette dernière, la création d’une application ne passe en effet plus par l’écriture de code, mais par la manipulation de blocs fonctionnels (prise/dépose d’une pièce, mouvements, etc.) directement sur un écran tactile.
Cobots en complément
On peut reconnaître dans ce développement la même logique de démocratisation que celle qui, conjointement avec la promesse d’une conception «intrinsèquement sûre», a fait le succès de la robotique collaborative, passée de moins de 2% des ventes mondiales de robots il y a une petite dizaine d’années, à quelque 10% actuellement. «Avec la rapidité d’installation, la facilité de (re)programmation est notre marque de fabrique», opine Martin Duterte, ingénieur commercial chez Universal Robots. Une opinion semble-t-il partagée par le marché, si l’on se réfère aux 40 000 cobots UR mis en service dans le monde au cours des quatre dernières années, et que le lancement d’une nouvelle plate-forme logicielle (PolyScope X) vise à entretenir – et si possible conforter – malgré les efforts de la concurrence. «Pour autant, il n’est pas question pour la cobotique de remplacer la robotique industrielle traditionnelle, car les deux familles répondent à des besoins différents : flexibilisation de la production avec faible empreinte au sol pour la première, hautes cadences pour la seconde», insiste l’ingénieur commercial. Ce qui ne signifie pas que les machines soient nécessairement très différentes : «certains cobots pourraient très bien accéder à des cadences plus élevées, toujours dans un environnement ouvert, à condition d’être associés à des scrutateurs laser chargés de sécuriser la zone de travail, de même qu’un robot industriel classique peut tout à fait être utilisé comme un cobot si on le dote des options de sécurité nécessaires. D’ailleurs, les principaux fabricants de robots industriels disposent tous aujourd’hui d’une gamme de cobots !».
Solutions standardisées
En somme, les clients ont le choix… et l’embarras du choix.D’où l’importance pour eux d’être bien orientés. En tant que
responsable du réseau de partenaires/intégrateurs d’Universal Robots,Martin Duterte met en avant le côté sécurisant et «facile à prendre en main» des offres standardisées développées au sein de ce réseau, à l’instar de la solution de palettisation UR20-PE20d’UR et Robotiq. «Bien entendu, tout dépend de la complexité de l’application, certaines d’entre elles constituant même de véritables défis ! Par exemple la palettisation hétérogène, qui consiste à manipuler et à positionner différents produits sur une palette en garantissant l’équilibrage final». Typiquement le genre d’exercice dans lequel il paraît intéressant de recourir à l’intelligence artificielle… Laquelle IA fait opportunément l’objet d’un partenariat entre Universal Robots et la société Nvidia : «grâce à cette collaboration, nous allons intégrer dès cette année à notre catalogue un ensemble de périphériques associés à diverses briques logicielles, notamment autour de la reconnaissance de forme pour des cobots de dévracage», commente Martin Duterte.
Amélioration de la cybersécurité
« La différence entre un robot industriel et un robot collaboratif, c’est qu’il faut arrêter le premier avant de pouvoir le toucher, alors qu’on peut toucher le second pour l’arrêter, résume sous forme de boutade Nicolas Couche, responsable produits chez Fanuc. Mais pour ce qui concerne la programmation, ces deux types de robots disposent chez nous des mêmes interfaces graphiques, donc on ne peut pas dire que l’un soit plus simple à configurer que l’autre». Autre remarque au sujet des coûts : «en moyenne, l’investissement matériel représente aujourd’hui à peine un tiers du budget global, c’est-à-dire moins que la somme des études, de l’installation, des essais, etc. Par conséquent, c’est la complexité d’un projet robotique qui en détermine bien plus le coût que le fait de mettre en œuvre un robot industriel ou un robot collaboratif».
Ces mises au point étant faites, Nicolas Couche souligne que ce n’est pas seulement sur la technologie des bras robotisés que portent actuellement les efforts R&D de Fanuc, mais aussi sur le contrôle et les logiciels applicatifs. Disponible en standard sur tous les cobots CRX(une douzaine de modèles au total, tous déclinés en version IAA) et opérable sur les robots non collaboratifs via l’utilisation d’une tablette, le nouveau logiciel PalletTool®3 permet ainsi aux opérateurs d’optimiser les plans de palettisation. S’agissant du picking, on note également l’arrivée d’un outil de gestion de flux baptisé iRPickTool qui permet à un ou plusieurs robots d’identifier, de saisir et de positionner des objets sur un convoyeur à bande. Enfin, l’année 2025 sera marquée chez Fanuc par l’introduction et la généralisation progressive du contrôleur R-50iAqui, outre de meilleures performances d’asservissement, anticipe les exigences en matière de cybersécurité du règlement européen sur les machines qui entrera en vigueur à partir de janvier 2027.