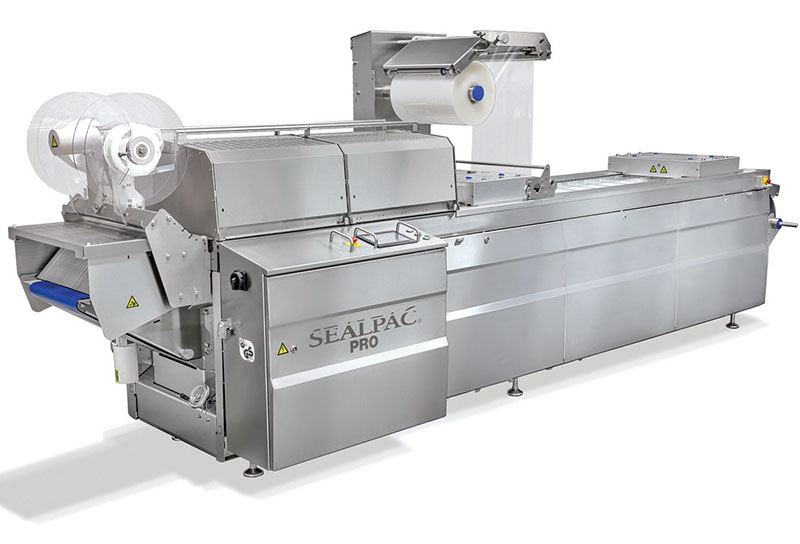
Des thermoformeuses à la portée des PME
publié le vendredi 31 mai 2024
Abonnez-vous à la revue pour lire la suite de l'article
s'abonner
Moins coûteuses, focalisées sur les tâches essentielles et faciles à prendre en main, même par du personnel inexpérimenté, les thermoformeuses destinées aux PME constituent une catégorie bien à part pour les constructeurs.
« L’introduction des thermoformeuses Série PROsur le marché français vise à renforcer notre position sur le segment des machines économiques et compactes que recherchent la plupart des PME de l’agroalimentaire», explique Thomas François, responsable commercial de Sealpac pour les régions Nord et Est. De fait, dans le thermoformage, ce fournisseur était jusque-là connu pour sa Série RE, constituée d’équipements plutôt destinés aux grandes séries. «Du point de vue de la capacité de production, la Série PRO s’arrête avec la PRO14 là où la Série RE commence avec RE15», indique le responsable commercial.
Mais au-delà de l’élargissement de l’offre, cette Série PRO marque aussi chez Sealpac un tournant en ce qui concerne les méthodes de fabrication : «alors que la Série RE met en œuvre des châssis pliés, des entretoises soudées, etc., autrement dit des procédés qui contribuent à la robustesse des matériels mais en augmentent le prix de revient, la Série PRO mise sur la découpe laser et une construction modulaire à même d’abaisser les coûts de production». Et si l’on ajoute à cela quelques optimisations et compromis techniques, on arriverait dans certaines configurations à un écart tarifaire de 30 à 40% entre la gamme RE et la Série PRO, estime Thomas François.
Trois machines complémentaires
« Le second intérêt de cette nouvelle famille pour les PME, poursuit-il, c’est le gain de place obtenu au niveau des zones de chargement grâce à l’adoption d’un système de cloisonnement autour des montées de postes et à la suppression concomitante des capots de protection amont et aval». La longueur d’une Série PRO démarre ainsi à 3 m et peut aller jusqu’à 4 m pour la PRO10, 5 m pour la PRO12 et 6 m pour la PRO14. En dehors de la longueur et de la cadence (jusqu’à 8 cycles/minute pour les PRO10 et PRO12, 10 cycles/minute pour la PRO14), les différences entre les trois modèles portent sur la laize (jusqu’à 460 mm dans tous les cas mais avec davantage de latitude pour les PRO12 et PRO14), sur les pas d’avance (prédéfinis pour la PRO10, définissables par tranches de 10 mm pour la PRO12 et la PRO14), la profondeur maximale de formage (105 mm pour les PRO10 et PRO12, 140 mm pour la PRO14), et sur la compatibilité avec les différents matériaux et techniques d’emballage. Concrètement, la PRO10 sera limitée aux films souples et au sous-vide tandis que la PR012 autorise la mise sous atmosphère modifiée et que la PRO14 peut en outre traiter les films rigides et réaliser des emballages rétractables de type ShrinkStyle®.
Le skin et rien que le skin !
Reste à savoir si la polyvalence technique des modèles les plus sophistiqués correspond à un véritable besoin de la part des industriels. Il y a quelques années, c’est ce que déclarait Ulma Packaging en présentant la thermoformeuse TFS 200 MSV (pour MAP/Skin/Vacuum). Or, c’est un constat sensiblement différent que dresse aujourd’hui Yves Belzanne, directeur du développement commercial thermo/operculage pour la France : «l’expérience montre que les clients qui ont acquis cette machine l’utilisent en réalité pour faire soit du MAP et de la mise sous vide, soit uniquement du skin». L’autre constat d’Ulma, c’est que le choix a priori surprenant des entreprises qui n’achètent la TFS 200 MSV que pour le skin s’explique en grande partie par l’attractivité de son tarif. «D’où l’idée de proposer une déclinaison encore moins coûteuse de ce modèle en lui ôtant le MAP et la mise sous vide, ce que nous avons fait avec la TFS 200 Sdont les caractéristiques générales sont identiques à celles de la MSV – notamment une cadence max. de 7,5 cycles/minute en skin – pour un prix catalogue inférieur d’environ 15%», indique le porte-parole d’Ulma Packaging.
Une thermoformeuse qui ne forme pas
Pour les poissons, charcuteries et autres viandes fraîches sous emballage skin, Ulma Packaging a par ailleurs lancé la TFS 216 : une machine assez particulière dans le sens où si elle est bel et bien construite sur la base d’une thermoformeuse, elle n’opère aucun formage du support. L’idée est en l’occurrence de travailler à partir d’un carton (avec liner) livré en rouleau et qui reste plat jusqu’à sa découpe, après nappage du film, mise sous vide et soudure. «La protrusion des produits sur ces cartons plats peut atteindre 90 mm et il est possible de traiter jusqu’à six plateaux à la fois à une cadence comprise entre 7 et 10 cycles/min», détaille le directeur du développement commercial. Précisons que la TFS 216 s’avère d’autant plus économique à l’usage qu’elle est équipée d’un système de transport du film inférieur sans chaîne qui rend le carton utilisable sur toute sa largeur, sans aucun déchet.
Dans ce même objectif de limiter les chutes de film, Yves Belzanne mentionne également la nouvelle technique brevetée Width-Flex qui permet de faire varier la laize d’une machine en fonction des impératifs de production : «tout se fait en mode 100% automatique grâce à des moteurs brushless. S’agissant de la thermoformeuse TFS 700, la plus grosse de notre gamme et pour l’instant la seule à bénéficier de cette option, le réglage va de 320 à 700 mm».
Le confort des réglages 100% automatiques
Pour Éric Le Normand, responsable technique chez Guelt, la simplification des changements de formats fait aujourd’hui partie des services les plus utiles qu’un constructeur de machines puisse rendre à ses clients, surtout dans le cas des PME : «dans l’agroalimentaire, ces entreprises ont encore plus de mal à recruter que les autres, donc elles embauchent souvent des personnes sans expérience qui apprécieront tout particulièrement les réglages 100% automatiques». Lancée en 2019 mais plusieurs fois améliorée depuis, la THR3 Premiumest l’exemple type de ces équipements faciles à piloter. «Les changements de formats automatiques concernent à la fois le formage, la soudure et la découpe, ces deux dernières étapes étant opérées sur le même poste», souligne le responsable technique. Une conception originale qui a d’ailleurs été l’occasion d’un dépôt de brevet portant sur une étape de soudure spécifique : «sur cette machine, la découpe a pour effet de supprimer la liaison qui existe entre les deux films et permet normalement l’entraînement du film supérieur. Si bien qu’il nous a fallu rétablir une liaison sur les bords du film grâce à un petit poste de soudure situé avant le poste principal et dont la description constitue l’un des points clés du brevet».
Intelligence assistée
En pratique, lorsque le changement de format n’impose pas le remplacement du film, Guelt garantit une exécution en moins de 30 secondes. «Il suffit d’appuyer sur un bouton et le reste s’effectue tout seul », commente Éric Le Normand, ajoutant que grâce à certaines astuces d’implantation, le fait de disposer à demeure d’un choix de quatre outillages supérieurs n’a pas d’impact significatif sur l’encombrement de la machine (L x l x h : 3153 x 1140 x 1727 mm).
Caractérisée par une cadence de 6 à 15 cycles/minute et une profondeur de thermoformage de 70 mm en cinq paliers, la dernière version de la THR3 Premiumse veut capable de répondre à la plupart des cas d’utilisation (film rigide, film souple, carton…) avec en prime un certain quotient d’intelligence assistée : «elle peut reconnaître les films et matériaux qu’elle va souder et propose alors les réglages adéquats à l’opérateur en fonction de l’historique».