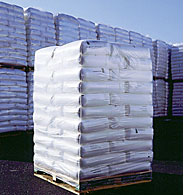
Emballage tertiaire : l’optimisation de mise
publié le jeudi 30 avril 2020
Si leurs fonctions premières restent de sécuriser le transport des palettes et protéger les produits conditionnés de l’environnement extérieur, les films, gaines et housses gagnent en technicité. De plus en plus légers et résistants, ils ne dérogent pas à la tendance générale de l’économie circulaire, intégrant progressivement un taux croissant de plastique recyclé. Avec toutes les contraintes techniques que cela implique.
Des films plus fins pour consommer moins
Dans un marché de l’emballage tertiaire où l’heure est à l’économie de matière, le film de banderolage encore appelé film étirable séduit chaque jour davantage. Amorcée il y a quatre ans, la mutation s’est faite au détriment de la gaine rétractable, jusqu’alors très répandue car abordable et nécessitant peu d’investissement. «La transition a été portée par les grands faiseurs de l’industrie agroalimentaire, et plus particulièrement les acteurs de la boisson. Lorsque de grands groupes comme Cristaline, Danone ou Nestlé opèrent 160 palettes par heure, un gain d’une centaine de grammes de plastique par palette commence à devenir plus qu’intéressant», observe Olivier Pochon, directeur des ventes industrie du groupe Barbier. A titre de comparaison, une palette peut consommer entre 800 g et 1 kg de plastique pour une gaine rétractable, d’une épaisseur moyenne de 100-110 microns, contre 300 à 450 g de plastique pour un film étirable d’une épaisseur de 23 microns. «On estime en moyenne que le film étirable permet une économie de 50% de consommable plastique par an, un atout non négligeable, tant sur le plan financier qu’environnemental», précise le représentant du groupe Barbier. Si le fabricant propose une large panoplie de technologies pour le secteur de l’emballage tertiaire (gamme Barflex (gaine étirable à froid); Barcover (gaine rétractable) et Barstretch (film étirable)), c’est sur le film étirable que le groupe a plus particulièrement investi ses efforts R&D.
«Au même titre que les machines de banderolage se sont bien améliorées, les films étirablesse sont perfectionnés pour devenir de plus en plus techniques. Sur un film XT à fort étirage par exemple, qualité utilisée par les grands de la boisson, les machines de banderolagepeuvent appliquer une force d’étirement allant jusqu’à 300-400% avec un contrôle optimal des tensions, contre il y a peu 150-200%, pour obtenir une épaisseur résiduelle de 5-6 microns. Ces films ont aussi gagné en résistance grâce à un travail de formulation des résines, ils intègrent désormais 9 couches contre 5 auparavant», détaille Olivier Pochon.
Le prochain challenge et non des moindres sera de parvenir à conserver ces propriétés techniques tout en intégrant de la matière régénérée, à hauteur de 40 à 70%. «Cela n’est pas sans surcoût à ces pourcentages car cela impacte les couches fonctions du film, mais reste techniquement réalisable. En tout cas, la demande est croissante et nous incitons nos clients dès à présent à anticiper cette transition, afin d’être prêts lors de la mise en place de la future REP sur les déchets industriels et commerciaux prévue à horizon 2022», explique le directeur des ventes industrie. Le fabricant a d’ailleurs récemment développé pour le groupe Raja un film étirable manuel recyclé à 80%, composé de 30% de film PCR et de 50% de scrab de production. Il est utilisé dans les procédures de «palettisation» et permet de maintenir et sécuriser les marchandises en les protégeant de la poussière, des intempéries et de la lumière, que ce soit dans l’entrepôt, en atelier, ou durant l’expédition. Sa performance éco-responsable du produit n’altère en rien ses caractéristiques mécaniques de résistance et d’étirabilité. Prochaine étape : la mise au point par Barbier d’un film automatique intégrant 50% de matière recyclée et étirable mécaniquement.
Extrait de la revue n° 647 – Avril 2020. Reproduction interdite sauf accord écrit d’Emballage Digest ou mention du support