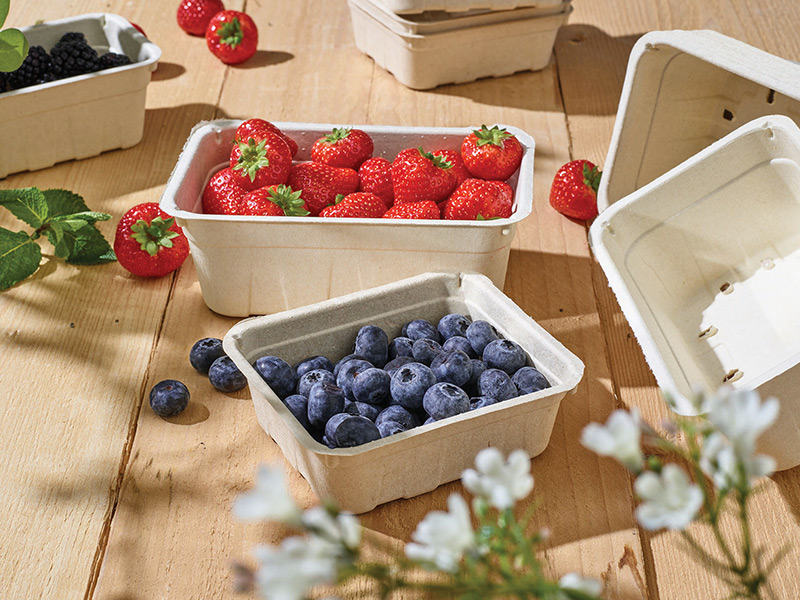
Emballages en cellulose moulée : un fort potentiel sous conditions
publié le samedi 30 novembre 2024
Abonnez-vous à la revue pour lire la suite de l'article
s'abonner
La cellulose moulée en est encore à ses débuts mais pourrait constituer une alternative intéressante aux emballages en plastique, à condition de relever deux défis majeurs : l’amélioration de ses capacités barrière, et l’augmentation de ses taux de production pour être plus compétitive.
La cellulose moulée progresse dans l’industrie de l’agro-alimentaire, stimulée par la nécessité de réduire l’utilisation du plastique. Outre les classiques boîtes à œufs, les applications se diversifient avec des barquettes pour fruits et légumes, ou des barquettes pour plats préparés. De nouvelles familles de produits émergent, à l’instar de la nourriture pour animaux, des produits congelés nécessitant des calages ou des calendriers de l’avent pour chocolats, comme celui réalisé par le fabricant d’emballages en cellulose moulée à sec PulPac pour la marque Lakrids by Bulow. Pour des applications futures, ce fabricant collabore par ailleurs avec PA Consulting dans le cadre du projet Bottle Collective, pour lequel le groupe Diageo teste des bouteilles en fibre moulée à sec pour des marques comme Baileys et Johnnie Walker…
Pour l’instant, les emballages en cellulose moulée vendus en France proviennent majoritairement d’Asie. Quelques acteurs se sont lancés dans une production locale sur le marché français. Pour Marion Muzy, responsable R&D du fabricant Ecofeutre, «le potentiel sur les emballages en cellulose moulée est énorme. En 2019-2020, nous avons constaté une forte augmentation de la demande, notamment pour la restauration à emporter. Ecofeutre a investi dans la construction d’une usine quasiment entièrement dédiée à l’emballage alimentaire en cellulose, en fibres vierges pour du contact direct. On assiste à une augmentation globale de la demande mais la loi AGEC, ses modifications, et l’arrivée de la directive PPWR ont apporté de la confusion. Cette dernière pourrait en effet s’avérer moins restrictive concernant le conditionnement de certains fruits et légumes. Les industriels ont mis en suspend leurs projets et attendent d’en savoir plus sur ce segment de marché», dit-elle. Frédéric Salomon, directeur général et co-fondateur de la société Daurema avec Cyril Forestier et Florian Lefebvre, renchérit : «nous sommes encore peu d’acteurs, et notre petite entreprise reste un ovni dans l’industrie française de la cellulose moulée. Nous avons investi 4 millions d’euros dans notre unité de fabrication, pour une capacité de production de 25 millions de pièces. En 2024, notre production sera plutôt de 8 à 10 millions de pièces, nous avons encore de la marge. Initialement notre objectif était de cibler le marché des fruits rouges, qui a été exempté par la loi AGEC. Les lois changent trop fréquemment, et nous en sommes tributaires», soupire-t-il. Les associés réfléchissent au développement d’autres produits, en dehors du secteur de l’agro-alimentaire.
A chaque technologie de formage ses avantages
Toute jeune société, Daurema s’est lancée il y a deux ans sur le segment de la barquette en cellulose moulée pour conditionner des fruits et légumes. Elle dispose d’une gamme de six barquettes obtenues par thermoformage des fibres, «la technologie la plus premium pour des produits plus esthétiques. La ligne de production est alimentée par la pâte de cellulose : les barquettes sont ensuite formées en ligne grâce à un moule. Certes, ce process de fabrication consomme de l’eau, mais nous pouvons aujourd’hui la réutiliser. En revanche, les coûts d’électricité sont importants car c’est indispensable pour sécher les barquettes», explique Frédéric Salomon. Les associés souhaitaient proposer des emballages «naturels», sans liner plastique. «La cellulose, matière première renouvelable, se trouve dans tous les végétaux ! Nous utilisons des fibres issues de forêts gérées de façon durable ou de plantes annuelles – blé, chanvre, lin, miscanthus… Sa fin de vie est simplifiée : une barquette en cellulose se recycle dans la filière papier-carton, ou en compost à domicile», ajoute-t-il. La cellulose moulée assure, par ailleurs, une bonne protection des produits conditionnés en amortissant les chocs, et permet un design sur-mesure. Il existe actuellement trois types de technologie de fabrication de cellulose moulée – de deux en mode humide et une séche. La méthode «conventionnelle» – la plus répandue en France – compte deux moules de formage à froid et un tunnel de séchage, pour obtenir par exemple des boites à œufs ou des calages résistants. La technologie de thermoformage implique elle quatre ou six moules de formage – dont deux à froid et quatre à chaud, pour la fabrication de produits à parois fines (barquettes alimentaires, intercalaires de briques, etc.). Elle commence à être bien représentée sur notre territoire. Quant à la cellulose moulée à sec, elle est pour l’instant émergente en France et adaptée à la production de produits de faible profondeur (couvercles, plateaux, produits PulPac). Contrairement aux deux précédentes technologies qui nécessitent de grandes quantités d’eau, les fibres sèches sont comprimées et moulées sous haute pression, à haute température. Ses partisans mettent en avant une moindre consommation d’eau et d’énergie. En France, le groupe Hébert a acquis la licence du groupe suédois PulPac en 2022 pour intégrer sa technologie de cellulose moulée à sec. Quant à la décoration de la fibre moulée, elle reste encore limitée. Ecofeutre est par exemple en mesure de proposer la technologie MFL™ (Molded Fiber Labeling), une étiquette en papier qui fusionne avec l’emballage en cellulose moulée. Mise au point par le groupe Pagès, cette solution permet de décorer des emballages de différentes formes (anguleux, ronds). Ecofeutre réalise en outre du marquage dans la masse grâce à des inserts, ou encore des designs spécifiques gravés dans le moule.
Augmenter la capacité barrière, tout en supprimant le liner plastique
Si les emballages en fibres moulées ont un fort potentiel, plusieurs défis doivent être relevés pour une adoption plus large. L’amélioration des propriétés barrières s’avère essentielle. Marion Muzy constate une augmentation de la demande de la fonctionnalisation de la cellulose moulée avec différentes barrières pour des conditionnements «longue durée». «Ecofeutre fabrique des boîtes à repasou des bols à salade thermoformés assurant une barrière à l’huile et à l’humidité pendant 24h, grâce à un traitement dans la masse de la fibre de cellulose. Nous utilisons des additifs fréquemment employés dans l’industrie papetière. Contrairement aux pays asiatiques, nous n’avons pas recours à des PFOAs ou des PFAs», précise-t-elle. «L’utilisation de molécules perfluorées – les PFAs – était efficace pour les barrières mais désormais contestée sur un plan environnemental et sanitaire. Ces molécules restent encore très utilisées par les fabricants chinois – cela joue plutôt en notre faveur», renchérit Frédéric Salomon. Chez Ecofeutre, le process de préparation de la pâte de cellulose permet d’obtenir des emballages plus denses, plus imperméables, limitant la traversée de l’huile ou de l’humidité. «Le triptyque machine-matière-moule a toute son importance», assure Marion Muzy. Par ailleurs, Ecofeutre travaille sur la lamination de films fins en plastique (PE/PP) et bioplastique (PLA) pour garantir une barrière longue durée à l’oxygène et à la vapeur d’eau. «Nous avons investi en 2022 dans une machine dédiée à la lamination. Nous axons notre communication sur le fait de séparer le film de la barquette bien que celui-ci ne perturbe pas le tri dans la filière carton. Un film de 50 à 100 microns, selon les barrières souhaitées, pèse environ 10 à 15% de la barquette. Ainsi ces barquettes laminées trouvent des applications dans les rayons «traiteur» des supermarchés, où elles restent une dizaine de jours. Certaines peuvent même garantir des durées de conservation plus longues – de 20 à 40 jours – pour des produits préparés, comme des panés végétaux. Outre la lamination, la cellulose est traitée en masse contre l’humidité afin que la barquette résiste aux conditions du réfrigérateur», détaille Marion Muzy. Depuis quelques années, de nombreuses publications scientifiques se concentrent sur la fonctionnalité. «Nous savons que le film complexé est une transition avant une solution sans plastique. Nous collaborons avec différents laboratoires en France, en Allemagne et aux Etats-Unis sur la fonctionnalité en surface, par exemple en ayant recours à un multi-trempage pour obtenir un complexe à base de fibres. Nous nous sommes aussi rapprochés de start-ups qui travaillent sur le greffage de la cellulose», explique-t-elle. Des traitements de surface et des enductions en sprayage existent, mais nécessitent un savoir-faire précis et restent, pour certains, à base de polymères. Assurément, apporter une fonctionnalité sur des produits en 3D tout en assurant la possibilité de sceller la barquette reste une étape importante dans le développement futur des emballages alimentaires en fibre moulée.
Réduire les prix des pack en cellulose moulée pour favoriser leur adoption massive
Un autre défi réside dans l’échelle de production de la fibre moulée traditionnelle par rapport aux plastiques. «Avec des taux de production pour les produits en fibre moulée conventionnelle nettement inférieurs à ceux des plastiques, les entreprises doivent souvent investir massivement pour agrandir leur capacité de fabrication afin de rivaliser avec celle du plastique. La fibre moulée à sec, cependant, répond à cette limitation en offrant des vitesses de production rapides et une production élevée dans un espace d’usine réduit», remarque Viktor Wingård Börjesson, directeur des opérations de PulPac. Côté prix de revient, une barquette en cellulose coûte environ deux fois plus cher qu’une barquette en plastique, pour des produits de grande consommation. En outre, «on note une différence de prix entre les produits chinois et français, malgré le transport depuis l’Asie… Le prix reste encore un frein. Les machines n’ont pas les mêmes cadences, et c’est logique : on extrait de l’eau de la cellulose, cela ne se fait pas aussi rapidement que refroidir du plastique ! Cela dit, elles évoluent, deviennent plus «industrielles». Depuis quatre ou cinq ans, on voit l’émergence de nouveaux fournisseurs de machines qui ont la volonté d’industrialiser nos technologies», souligne Marion Muzy. Le coût de la barquette en cellulose pourrait à terme être réduit s’il devient possible d’utiliser à plus large échelle la fibre recyclée et les résidus de fibres végétales, surtout avec des machines plus performantes. «Nos travaux de recherche sur les résidus de procédé de fibres végétales comme le lin et le chanvre, leurs traitements pour être aptes aux thermoformages et leur fonctionnalisation sont en cours. Cela permettra de maîtriser et de réduire les coûts de matières premières, et de sourcer localement une cellulose qui ne provient pas du bois», ajoute-t-elle. Viktor Wingård Börjesson estime que «les consommateurs sont de plus en plus disposés à payer davantage pour des options durables. Selon le rapport Buying Green 2023 de Trivium Packaging, 82% des consommateurs, tous groupes d’âge confondus, sont prêts à payer un supplément pour des emballages durables – soit une augmentation de quatre points par rapport à 2022 et de huit points depuis 2021. Ce changement dans les attentes des consommateurs renforce la viabilité de la fibre moulée en tant qu’alternative durable». Le groupe PulPac estime que les progrès réalisés sur les machines permettront de fabriquer bientôt en fibre moulée à sec des produits d’une profondeur plus importante. L’aventure de la cellulose moulée ne fait que commencer.