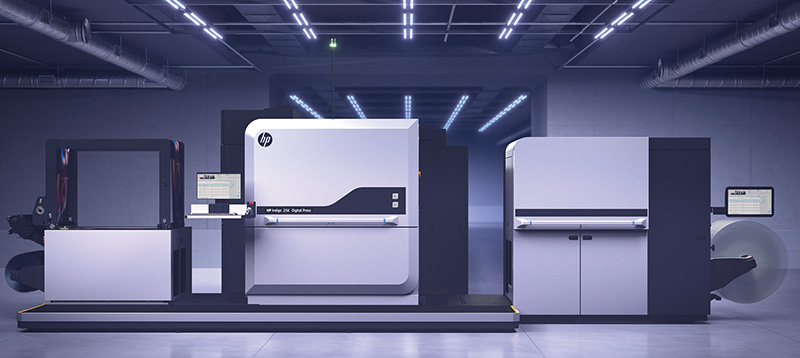
L’impression numérique change de braquet
posted Tuesday 28 February 2023
Abonnez-vous à la revue pour lire la suite de l'article
s'abonner
Sans rien changer à leur positionnement sur la personnalisation et le packaging à valeur ajoutée, les fournisseurs de presses numériques font grimper la productivité de leurs machines de façon à viser des tirages plus importants. Ils mettent, par ailleurs, en avant leurs atouts environnementaux, y compris sur le plan énergétique.
« Passez du fichier au sachet en quelques jours au lieu de plusieurs semaines et imposez-vous sur le marché des emballages souples, écoresponsables et à la demande» : telle est la promesse alléchante que fait HP aux futurs utilisateurs de la presse numérique par procédé électrophotographique liquide (LEP) HP Indigo 25K. Avec un parc installé de l’ordre de 300 machines à travers le monde, ce qui représente un peu plus de 200 clients dans une cinquantaine de pays, cette promesse a su convaincre… même si les débuts n’ont pas été faciles, assume Stéphane Delange, directeur des ventes Label & Packaging chez HP France : «en 2014, le fait de passer de 340 à 760 mm de laize avec l’arrivée de la machine HP Indigo 20000 avait déjà élargi le spectre de nos possibilités dans le domaine de l’impression sur film souple. Néanmoins, il nous a fallu mener un important travail d’«évangélisation» auprès de clients imprimeurs habitués aux grosses volumétries et ne jurant que par la flexographie ou l’héliogravure». L’adoption de cette technologie a donc été progressive, mais elle s’installe très solidement depuis l’introduction du modèle HP Indigo 25K, il y a deux ans, poursuit le directeur des ventes : «cette presse remplace aujourd’hui la HP Indigo 20000 dans l’application films* souples, avec des améliorations significatives en termes de gestion colorimétrique et de rapidité de mise en œuvre».
Accélération du time to market
Au-delà des aspects techniques – conformité aux réglementations de l’UE et de la FDA en matière d’emballage des denrées alimentaires bien entendu, mais aussi qualité comparable à celle de la flexo ou de l’hélio –, Stéphane Delange invoque également une conjoncture très favorable pour expliquer le dynamisme du marché de l’emballage alimentaire flexible imprimé à la demande. «Nos solutions numériques sont plutôt positionnées sur les séries limitées ou moyennes. Et nous voyons justement apparaître beaucoup de petites marques dont la principale préoccupation au sujet de l’impression des emballages n’est pas le volume mais la réactivité : l’un de nos points forts puisqu’on parle en l’occurrence d’une semaine de délai au lieu de huit en conventionnel». À cela s’ajoute une forte tendance à la personnalisation, laquelle a concerné 15% du packaging souple en 2022, soit 50% d’augmentation en un an, observe le directeur des ventes. Enfin, il ne faut pas négliger les considérations environnementales, largement en faveur de l’impression numérique selon HP. Dans un livre blanc paru en 2016, ce dernier faisait ainsi état, pour les presses Indigo, d’un impact réduit de 40 à 60% par rapport à la flexographie, et de 60 à 80% par rapport à l’héliogravure.
Intégration facilitée dans les lignes de production
Dans l’alimentaire, si Mimaki est absent du marché des emballages plastique en contact avec les denrées, ce fournisseur est en revanche bien présent sur celui du packaging à haute valeur ajoutée, qu’il s’agisse de cartonnages, de bouteilles de verre, de boîtes en métal ou même de contenants en bois. «Avec la technologie UV, la polymérisation de nos encres se fait par flashage, donc sans chauffe ni risque d’altération du support. Notre procédé est par conséquent non seulement économe en énergie, mais parfaitement compatible avec le bois, ce qui donne lieu à des réalisations très originales dans l’alimentaire», se félicite Martial Granet, directeur de la filiale France & Maghreb. Si ce fabricant, pour l’instant, n’accompagne pas les industriels du packaging sur les très longues séries propres à la grande distribution, un pas vers une plus grande automatisation et une meilleure intégration de ses machines dans les lignes de production a toutefois été franchi avec la prise en charge des commandes MDL (Mimaki Device Language). Une fonctionnalité proposée notamment sur les nouvelles imprimantes à jet d’encre UV-LED UJF MkII e-series, capables d’imprimer à plat sur une grande variété d’objets (boîtes, bouteilles thermos, etc.), ou encore sur la JFX600-2513, qui se distingue par la taille de son plateau (2,5 m x 1,3 m) et le nombre de ses têtes (16). Au final, ce modèle affiche une vitesse de 200 m²/h, trois à quatre fois celle de la JFX500-2131. Et ceci avec les atouts habituels des imprimantes à jet d’encre UV dans le domaine de la personnalisation. «Par superposition de couches, on peut aussi obtenir des effets de texture ou de relief très appréciés dans l’univers du luxe : boîtes de caviar, étuis de spiritueux, coffrets de pâtisseries haut de gamme…», énumère Martial Granet.
Numérique ET analogique
Dans cette éternelle dichotomie entre variabilité des impressions et volumétrie, le constructeur Koenig & Bauer, bien connu pour ses outils offset et flexo, tente une intéressante synthèse avec une machine hybride moyen format, dédiée au carton plat et dénommée VariJET 106. «L’idée, pour des tirages qui seraient en même temps importants et diversifiés, est d’intégrer dans la même machine d’une part l’offset, pour imprimer la partie commune à tous ces tirages, et d’autre part l’impression numérique jet d’encre, de façon à répondre aux problématiques de personnalisation, de données variables, etc. Avec en prime de multiples possibilités d’ennoblissement (dorure à froid, vernis sélectif….)», argumente Frédéric Pambianchi, directeur général de Koenig & Bauer France. Conçue en partenariat avec Durst pour la partie numérique (têtes d’impression, logiciel RIP), la VariJET 106 imprime en sept couleurs (CMJN, orange, vert et violet) au moyen d’une technologie jet d’encre à base aqueuse conforme aux normes alimentaires. Construit sur la base d’un châssis de machine offset Rapida 106, cet équipement est en capacité d’imprimer jusqu’à 5500 feuilles/h au format B1. Il est actuellement en bêta-test chez plusieurs clients (aucun en France) dont le point commun est de proposer à leurs clients la réalisation d’étuis pliants personnalisés ou en petites séries de manière rentable et rapide.
Économies d’énergie
Dans le coût de revient de ces tirages, il faut bien entendu intégrer la part croissante de l’énergie. D’où la décision récente de Koenig & Bauer de lancer une solution de gestion énergétique dédiée aux imprimeurs et aux fabricants d’emballages. «Pour mettre en œuvre cette solution baptisée VisuEnergy X, nous commençons par installer dans les différentes armoires électriques de la machine des boîtiers chargés de relever la consommation de chaque sous-ensemble, explique Frédéric Pambianchi. Une fois collectées, les données sont transmises à un logiciel de type Saas (Software as a service) en charge de les digérer et de les mettre en forme». À ce stade, le client dispose d’un tableau de bord, d’indicateurs et de rapports certes utiles pour constater d’éventuelles dérives, mais insuffisants pour conduire de véritables actions d’efficacité énergétique. «Celles-ci résulteront en fait du volet consulting de l’offre, réalisé par des cabinets spécialisés opérant en partenariat avec Koenig & Bauer. Ce sont ces spécialistes qui sauront conseiller utilement nos clients en matière d’optimisation opérationnelle, d’organisation de la production, etc.», précise Sarah Herrenkind, responsable marketing de la filiale française. Certifiée DIN ISO 50001, cette solution serait en mesure de réduire les consommations de 7 à 10% en moyenne dès la première année d’utilisation.