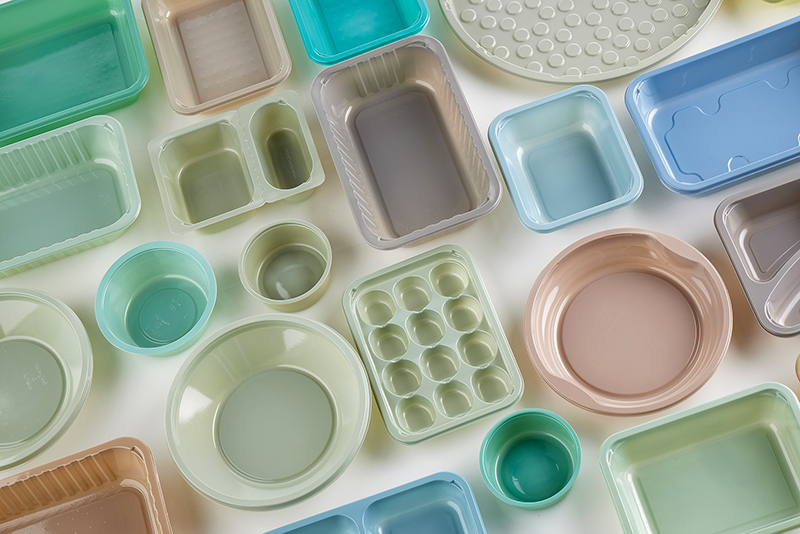
Les barquettes font le plein d’innovations !
posted Sunday 31 March 2024
Abonnez-vous à la revue pour lire la suite de l'article
s'abonner
De nouvelles alternatives arrivent sur le marché, avec des barquettes réutilisables ou des barquettes en carton adaptées à différentes fonctions. Qu’il s’agisse de barquettes en plastique ou en carton, réduire la part de matière et faire en sorte que l’emballage soit totalement recyclable restent des axes prioritaires pour les fabricants.
Dans le secteur des emballages en plastique – et notamment sur le segment de la barquette alimentaire – un nouveau discours émerge chez de plus en plus d’acteurs, qui affichent la volonté de recycler à terme la même quantité d’emballages que celle mise sur le marché. Concrètement, certains mettent en place un circuit de recyclage en boucle fermée dans le but de créer leur propre circularité en réutilisant la matière dans leurs emballages.
C’est le cas du groupe Faerch – qui vend environ 24 milliards de contenants alimentaires rigides sur le marché européen chaque année. Depuis 2018, aux Pays-Bas, il dispose de sa propre usine de recyclage de barquettes en PET, qui récupère «les barquettes alimentaires post-consommation pour les reconvertir en nouveau matériau de qualité alimentaire. Nous avons récemment réalisé des investissements importants pour augmenter la capacité de cette usine afin qu’elle puisse traiter 60 000 tonnes de déchets en entrée», explique Elisabet V. Sandnes, directrice du développement durable chez Faerch. Un système qui permet en outre d’assurer son indépendance et de sécuriser son approvisionnement en matière recyclée, à une période où la demande pour en intégrer dans les emballages est croissante. Ne voulant pas prélever le PET des collecteurs de bouteilles, Faerch a créé une boucle fermée pour collecter et recycler les barquettes en PET dans le Benelux. Le groupe ambitionne par ailleurs de construire davantage d’usines de recyclage en Europe. «L’emplacement dépendra des partenariats qui nous permettront de trouver des sources de matières premières de barquettes en PET post-consommation. Dans le pays choisi, nous serons bien sûr ouverts à toute discussion avec les recycleurs et les parties prenantes autour de la stratégie nationale concernant la responsabilité des producteurs», ajoute Elisabet V. Sandnes. Faerch mène plusieurs actions en parallèle, en convertissant, par exemple, un maximum d’emballages fabriqués à partir de matériaux multiples et de PS en PET, et en concevant de façon spécifique les barquettes afin que leur design permette un empilement ultra-bas. Elles nécessitent ainsi moins d’espace lors du transport.
Un design adapté pour faciliter le tri
L’écoconception, c’est également travailler sur la notion de design pour intégrer la fin de vie d’une barquette. «Le design doit faciliter le geste du tri par une forme ou une conception simplifiée, l’utilisation d’un colorant détectable, ou encore la juste part de matière. Si une barquette est destinée à un marché particulier, il est possible d’agir sur sa finesse, par exemple. Nous créons des moules prototypes afin que nos clients mènent des tests», détaille Eloïse Loriot, responsable communication d’Europlastiques, fabricant de barquettes en plastique – principalement en PP. Le groupe a, par ailleurs, sécurisé il y a quelques années un approvisionnement en matériaux recyclés chimiquement et aptes au contact alimentaire, mais le cadre règlementaire n’étant pas encore défini avec certitude, l’intégration de PP recyclé chimique n’est pour l’instant pas concrétisée.
Producteur d’emballage en carton, Solidus part de «l’utilisation finale de l’emballage et de sa future recyclabilité pour travailler en étroite collaboration avec les papeteries du groupe afin d’établir la qualité de carton (100% recyclé) à utiliser, et le grammage correct. Ensuite, en production, nous décidons du poids total de l’emballage et des revêtements adaptés. Nous disposons de plusieurs types de liners : papier kraft, films complexés, films PET, PE ou OPP selon les produits conditionnés et les conditions d’utilisation des emballages», décrit Daniel Aristegui, responsable des ventes pour Solidus. En 2023, le groupe a créé la filiale d’innovation Solidus Inova afin de coopérer avec un groupe d’industriels européens à l’élaboration d’emballages en carton recyclé pour l’industrie alimentaire, éliminant toute substance issue de matières fossiles. Récemment, Solidus a investi plusieurs millions d’euros pour créer et produire la nouvelle gamme Futurline® en carton, qui comprend un emballage skin, une barquette simple, et une barquette pour conditionnement sous atmosphère modifiée.
Associer réemploi et production de barquettes
Un consortium composé de trois sociétés françaises – Natural Development, Généomat et Natur’al Packaging – s’intéresse également aux emballages en carton. Elles se sont associées pour mettre au point la solution de conditionnement B-Simple System®, pensée pour répondre aux exigences de la loi AGEC, et déclinable afin d’obtenir différentes fonctions (sous vide, operculage, flowpack…). Le consortium vient de lancer sa première solution : une barquette «skin» pour l’emballage sous vide, encore en prototype. La barquette en carton, à usage unique, est livrée à plat : «elle est ensuite mise en forme sur le lieu de conditionnement grâce à un conformateur – une sorte de moule – réutilisable, en PP injecté donc solide, qui est adapté aux machines existantes chez les clients. En assemblant la barquette et le conformateur, le résultat ressemble à barquette classique, adapté à une machine sous vide. Le conformateur, qui absorbe les contraintes mécaniques du conditionnement skin, est ensuite retiré pour la mise en rayon de la barquette carton B-Simple conditionnée. Le conformateur – qui peut supporter 400 cycles selon nos estimations – reste dans l’atelier de conditionnement, ce qui supprime la problématique du retour des contenants que l’on rencontre souvent dans le réemploi», remarque Philippe L’Hospital, cofondateur de Natural Development. En partenariat avec Généomat, cabinet de conseil en innovation et R&D, spécialisé dans les matériaux, le recyclage et les emballages, B-Simple® a pu voir le jour. La société Natur’al Packaging commercialisera les emballages issus de cette solution, en bénéficiant d’une licence exclusive en France et en Belgique. «Fabriquer une nouvelle barquette coûte cher : notre système nécessite juste de fabriquer une empreinte (le conformateur) par thermoformage, pour un coût de développement de l’ordre de 5000 euros. Le carton est deux fois plus léger qu’un carton classique pour emballage «skin». Nous avons estimé que notre solution est deux fois moins chère qu’une barquette classique en carton – qui doit être épaisse pour résister aux contraintes de la technologie sous vide. Par ailleurs, le film sur le fond de la barquette, assurant la barrière, est posé à plat : on ne l’étire pas, il est donc très fin, de l’ordre de 25 microns», assure Philippe L’Hospital, dont la société réalise des bilans carbone et des analyses de cycle de vie. Pour cette barquette, l’ACV montre une réduction des émissions de gaz à effet de serre et une réduction en eau de 75%, par rapport à une barquette en PS de même format.
Une solution alternative : la barquette en bagasse
Spécialiste de la production d’emballages alimentaires en céramique, Agro Concept Embal commercialise également des produits en verre, acier émaillé et acier inoxydable. Depuis peu, la société propose une gamme de barquettes issues des déchets de la culture de la canne à sucre, 100% biodégradables, compostables (Home compost), et conformes au contact alimentaire. «Nous avons choisi cette matière car elle provient de déchets, et non de cultures. Nous avons conçu les moules afin que les barquettes soient utilisables sur les installations existantes sans aucune modification des matériels et outillages. Les barquettes sont ensuite fabriquées en Chine où la culture de la canne à sucre est bien présente. L’impact carbone sur une barquette transportée d’Asie est très faible car on en met énormément dans un cargo», précise Gérard Deshayes, directeur commercial de la société. Selon la société, les barquettes en bagasse offrent une bonne résistance mécanique et thermique – tenue jusqu’à 220 degrés, compatibilité avec tout type de fours, et possibilité de surgélation. L’intérieur est recouvert d’un liner de faible épaisseur de type PE ou PP selon les aliments conditionnés, pour apporter étanchéité et barrière au gaz. «Déposer un liner sur la barquette n’est pas simple, car il faut réussir à placer un film de faible épaisseur – entre 50 et 115 microns – sans qu’il perde ses propriétés. Nous avons mis cela au point avec l’équipementier Ati-Ouest – et beaucoup d’investissements en R&D, moules, outillages, lignes robotisées… Le film représente environ 10% du poids total de l’emballage : il n’est pas nécessaire de le retirer – bien qu’il soit conçu pour être détachable – avant de mettre la barquette à recycler dans la filière papier-carton», ajoute Gérard Deshayes. La société garantit par ailleurs l’absence de liant hydrophobe dans le matériau – qui peut gêner la désintégration de la fibre lors du recyclage. Ce liant est parfois nécessaire pour certaines matières afin d’assurer la rigidité et l’étanchéité de la barquette. Adaptée à de multiples applications (charcuterie, produits de la mer, surgelés ou encore plats cuisinés), la barquette est operculable avec ou sans liner – dans ce cas, le soudant du film sera spécifique pour adhérer directement sur la bagasse. Cette barquette a reçu un avis favorable du Cerec (Comité d’Evaluation de la Recyclabilité des Emballages papiers Cartons, créé par Citeo et Revipac) concernant sa recyclabilité. L’organisme complète généralement ses avis par des recommandations pour encore améliorer la recyclabilité de l’emballage – des conseils précieux pour les acteurs du secteur.