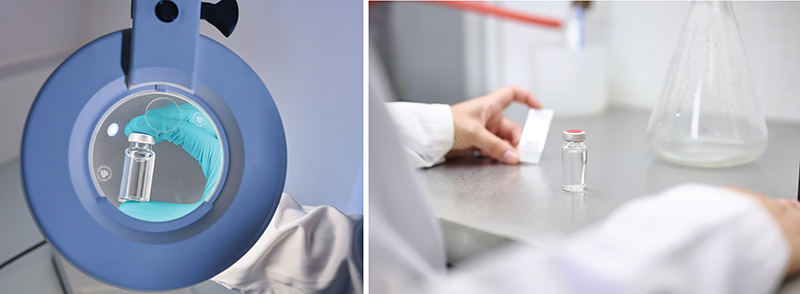
Flacons verre : comment répondre à la forte demande
posted Thursday 30 March 2023
Abonnez-vous à la revue pour lire la suite de l'article
s'abonner
La plupart des produits pharmaceutiques administrés par voie parentérale/injectable sont conditionnés dans du verre étiré tubulaire de Type I, qui présente une forte résistance hydrolytique ainsi qu’aux chocs thermiques. Face aux pénuries liées à une forte demande mondiale, les fabricants de flacons en verre (SGD Pharma, Bormioli Pharma, Schott) ont développé des alternatives en verre moulé pour répondre aux nombreux besoins liés aux médicaments biotechs et innovants, notamment les vaccins. Ils investissent également dans de nouvelles capacités et des solutions durables dans le sens de la RSE. Sans oublier de nouvelles solutions de distribution d’ampoules (Packsys).
La période de la Covid-19 a accéléré l’innovation pour conditionner les médicaments les plus sensibles, biotechs et innovants afin de garantir les capacités et les approvisionnements.
Illustration avec Idency, le nouveau flacon moulé en verre de Type I destiné à la voie d’administration parentérale, développé en un temps record par les équipes de SGD Pharma pour proposer une offre complémentaire au verre étiré à ses clients. «Il s’agit d’une nouvelle génération de flacons allégés en poids de 24% par rapport à un flacon moulé standard ainsi qu’une réduction de 25% d’émission de CO2 comparé au processus de production du verre étiré», présente Najet Mebarki, directrice Product Management et Innovation chez SGD Pharma.
Du verre étiré au verre moulé
Le salon CPhI Francfort, en novembre 2022, a été l’occasion pour le fabricant de lancer et tester son nouveau flacon auprès des visiteurs. «Le retour a été très positif avec un effet de surprise lié à la difficulté de différencier les flacons étirés des flacons Idency en verre moulé», pointe Yvan Garnier, ingénieur chef de projet R&D senior chez SGD Pharma. La particularité de Idency est de présenter des caractéristiques d’inspectabilité comparables au flacon en verre tubulaire.
«L’aspect visuel est identique, note-t-il, la seule différence réside dans la hauteur avec un différentiel de 5 millimètres. Le flacon Idency
(10 ml) est également un peu plus lourd (16 grammes contre 10 grammes pour l’étiré) afin de garantir une résistance mécanique incomparable, avec la possibilité de gerber les palettes», ajoute-t-il. Autre avantage : son procédé de fabrication se fait en une seule étape, contrairement à celui du verre étiré qui requiert deux étapes. L’opération de transformation de la canne de verre peut être sujette à rendre plus sensible chimiquement la base des flacons, qui correspond à leur fermeture dans le procédé de fabrication. «Nous fabriquons Idency sur notre site de Saint-Quentin-La-Motte avec une technologie de pointe en termes de fours de fusion, de contrôles d’inspection et de salle ISO», souligne-t-il. Fier de cet accomplissement, SGD Pharma annonce pouvoir livrer le flacon partout dans le monde dans un délai compris entre 3 à 6 mois seulement. «Le passage d’un verre tubulaire à Idency n’induit pas de changement drastique sur les lignes de remplissage de nos clients», précise Najet Mebarki. La priorité est maintenant de développer la gamme et de lancer de nouveaux formats d’ici fin 2023. Un autre avantage concurrentiel de SGD Pharma pour le verre moulé est de les traiter en vue d’un thermoscellage. «Nous livrons des flacons Type III pour administration orale, du 10 au 730 ml, prêts à être thermoscellés, grâce à l’application d’un traitement sur le buvant. Cette technologie est destinée aux produits en poudre, notamment les antibiotiques pédiatriques, très sensibles à l’humidité et à l’oxygène», indique-t-elle.
Étude comparative
De son côté, Bormioli Pharma répond aux pénuries actuelles grâce à sa technologie Delta de verre borosilicaté moulé. «Il s’agit d’une solide alternative avec une performance très proche des flacons tubulaires pour des médicaments injectables à doses élevées», souligne Andrea Sentimenti, directeur marketing et innovation de Bormioli Pharma. Le fabricant a mené une étude comparative sur les flacons 10 et 30 ml en verre étiré et moulé, conformément aux directives standards de la pharmacopée européenne. «Les résultats ont révélé que le verre moulé permettait des performances mécaniques et chimiques supérieures par rapport au tubulaire, tandis que ce dernier affiche une meilleure qualité esthétique de surface», ajoute-t-il. «Le poids des flacons en verre moulé premium est d’environ 50% supérieur à celui des flacons tubulaires de la même catégorie, ce qui les rend nettement plus résistants aux contraintes mécaniques». De plus, l’absence d’échauffement localisé dans le processus de fabrication rend les flacons en verre moulé plus homogènes d’un point de vue chimique et plus résistants à la corrosion avec un risque négligeable, voire nul, de délamination. Concernant les chocs thermiques, les différences sont négligeables en termes de réaction au moins jusqu’à un différentiel de température de 90°C. «Nous souhaitions démontrer, données en main, que le verre moulé est une véritable alternative au verre tube pour les flacons, pour casser le mythe existant au sein de l’industrie que seul le verre tube est un choix possible pour l’emballage parentéral», note-t-il.
Nouvelles capacités et investissements
Après sa reprise par le fonds Triton Partner en 2017, Bormioli Pharma s’est engagé dans un vaste programme d’investissements pour développer ses capacités de production de verre, avec l’acquisition de nouveaux fours dans ses usines en Italie du nord (Bergantino et
San Vito al Tagliamento) et l’extension à venir de son site allemand à Bad Konigshofen.
Dans le même temps, SGD Pharma a investi 60 millions d’euros avec Corning dans une nouvelle usine dédiée au verre étiré tubulaire en Inde. «Nous devenons au travers de ce partenariat un fournisseur de cannes pour sécuriser la supply chain pour nos clients locaux et internationaux», note Najet Mebarki.
L’année dernière, Schott a annoncé tripler sa capacité de production de flacons prêts à l’emploi (RTU) au Liban, en Pennsylvanie, aux Etats-Unis. Avec sa plate-forme Schott iQ®, les flacons RTUsont livrés prélavés et pré-stérilisés pour réduire les coûts et délais de mise sur le marché des médicaments.
Les flacons adaptiQ® sont fabriqués à partir de verre borosilicaté Fiolax® Type I, avec plus de 750 combinaisons de produits possibles premium : Everic® pur (compatibilité médicamenteuse et une résistance au délaminage exceptionnelles), Schott Type I plus® (produits biologiques hautement sensibles), Schott TopLyo® (médicaments lyophilisés) et un verre de couleur ambre (produits sensibles à la lumière).