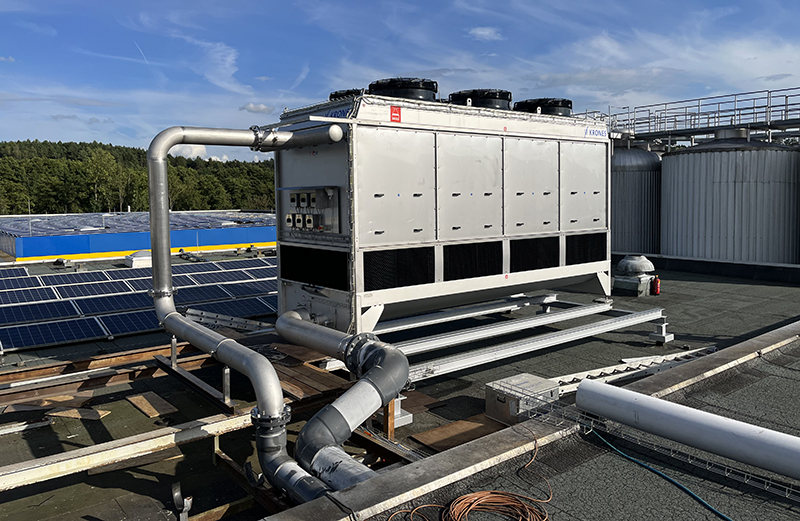
Krones equipped Kaiser Bräu with a VapoChill system
posted Tuesday 12 December 2023
The Kaiser Bräu brewery has expanded considerably in recent years. The beer is exported to Italy, China and the USA. One of the success factor is the use of state-of-the-art brewing and production technology. In recent years, a galvanised evaporative cooling system with a radial design was used for recooling the refrigeration system. Due to its age and design, the energy required for operation was no longer up to date. The decision in favour of a replacement and also in favour of a supplier was quickly made: In future, a Krones VapoChill will efficiently generate the required cooling energy.
Krones’ extensive expertise in thermal processes has been incorporated into the development of the VapoChill. The result is a particularly space-saving operating principle: the process water loses its heat in contact with the ambient air. Part of the water evaporates, whereby energy is extracted from the remaining water and it is cooled down. This concept of the open evaporative cooling tower enables a high energy yield on a small footprint. The hygienic design of the VapoChill was also important for Kaiser Bräu: the asymmetrically sloped tray of the cooling tower, which is made entirely of stainless steel, ensures that no water can accumulate and guarantees that the tray empties to the lowest point.
In addition to high beer quality, the issue of sustainability is also very important to Kaiser Bräu. « In order to be able to offer good beer with a clear conscience, we attach great importance to resource conservation and energy efficiency in our production. The particularly efficient fan was therefore another major plus point for us when selecting the cooling tower, » explains Stefan Benaburger, master brewer at Kaiser Bräu.
The EC motors of the fans are characterised by a high degree of efficiency and offer up to 30% less energy consumption in full load operation. As brushless motors, they also enable maintenance-free operation. The fans are infinitely variable so that the desired cooling temperature can be precisely maintained. This also contributes to energy efficiency, as unnecessary cooling is avoided.
Thanks to the integrated modular design in series production at the Flensburg plant, the VapoChill could be produced in just 8 weeks and delivered very quickly to the Neuhaus an der Pegnitz site thanks to a customised delivery concept.