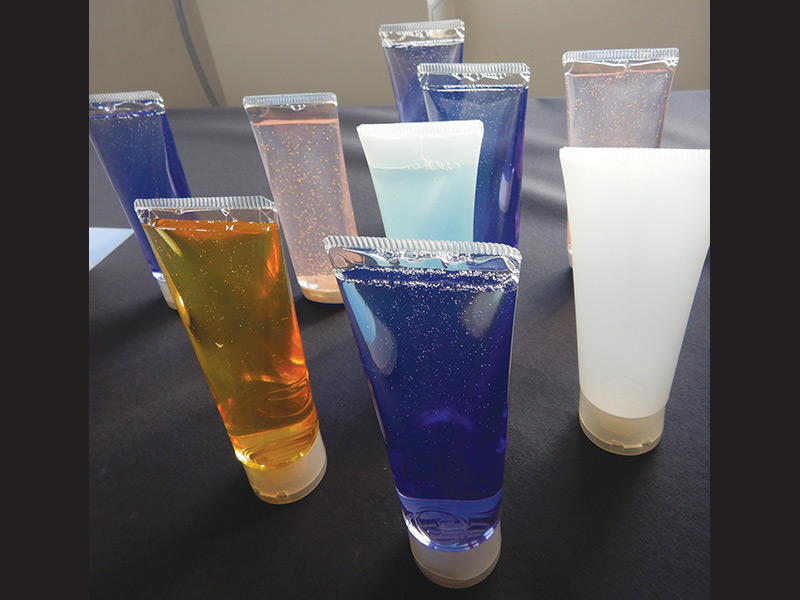
Le belge Delta Engineering dévoile ses dernières innovations techniques
posted Sunday 12 January 2025
De la bouteille au tube en passant par un nouvel essai autour de l’impression digitale directe, Delta Engineering dévoilait lors de ses dernières portes ouvertes ses technologies rupturistes.
Fondé en 1992, Delta Engineering est actif dans le domaine de l’automatisation pour l’industrie du plastique et particulièrement la conception et fabrication de machines d’automatisation pour le secteur du moulage par soufflage. Au grand site de production en Roumanie, bureau vente et service aux Etats-Unis, se joint un site de production technique et le siège social à Ophasselt, 40 km à l’ouest de Bruxelles. En 2023 Isytech, société française qui a fait partie de Sidel, connue pour son coating Actis® et spécialisée dans les traitements de surface, a rejoint le groupe. Cette année, c’est Shift+ID, société sud-africaine spécialisée dans la conception d’équipements pour impression digitale sur emballage, qui vient élargir l’expertise du groupe. Deux solutions innovantes sortaient du lot lors des journées portes ouvertes annuelles.
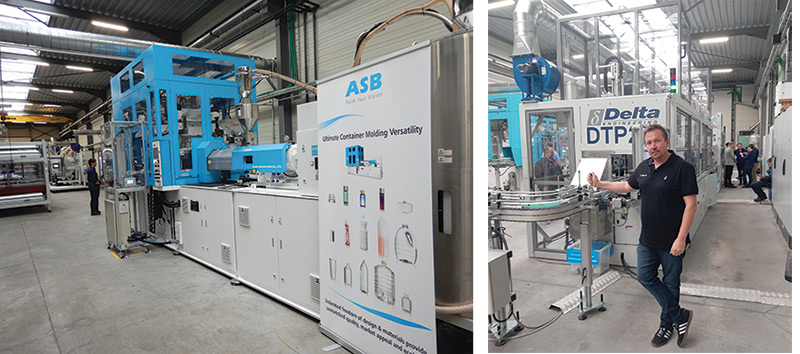
La technologie « Bottle to Tube »
Danny De Bruyn, l’un des fondateurs de Delta Engineering explique : «transformer une bouteille en tube n’est pas vraiment une idée nouvelle. Nous travaillons sur ce projet R&D depuis 2014. Un porteur de marque s’y est d’ailleurs risqué et cassé les dents… Le tout pour réussir un tel projet, c’est d’aligner le moment opportun avec les moyens financiers. Il y a aujourd’hui une série de soucis avec les tubes laminés et coextrudés sur le marché. Pas recyclables, ils pourraient bientôt être taxés, la tête du tube monomatière présente un risque de fuite à la barrière, les coûts de transport sont à la hausse, le remplissage des tubes n’est en moyenne que de 70%, et enfin la soudure finale n’est réalisée qu’en fin de process rendant la qualité du pack difficile à contrôler».
La technologie «Bottle-to-Tube» développée par Delta Engineering permet de transformer des bouteilles en PET moulées par soufflage en tubes souples. Tout d’abord lors de la phase de moulage et de conversion, les bouteilles en PET sont fabriquées par injection soufflage et moulage (ISBM). Elles sont ensuite transformées en tubes en coupant puis en soudant la base. Un processus simple qui évite les étapes multiples comme la coextrusion ou le laminage pour former un cylindre. Les tubes sont ensuite remplis en utilisant les lignes de remplissage standards pour bouteilles, sans besoin d’équipements spécifiques. Le niveau de remplissage est quasi-total, nul besoin de laisser une marge pour éviter tout débordement du produit. «Nous avons opté pour des tubes en 100% PET. Grâce à la haute densité de ce polymère, 30% en moins est nécessaire pour des tubes de même volume en PP. Le PET est plus robuste que le PP, qui a tendance à se briser dans des environnements froids. Le tube est de plus cristallin, permettant de voir le produit par transparence. Les tubes en démo ont une épaisseur de 180 microns. La machine DTA-101, dans le showroom possède une seule station et permet la production et le remplissage de 1000 tubes à l’heure. Dans un premier temps, nous visons le marché haut de gamme avec des volumes modestes. Notre seul brevet concerne la méthode de soudure», poursuit De Bruyn. Les tubes peuvent être revêtus par coating plasma pour fournir une barrière efficace contre l’oxygène et les solvants, les rendant adaptés aux produits sensibles. Ils peuvent également être manipulés comme des toddles en utilisant les outils standards des lignes d’embouteillages de boissons. Ils peuvent être imprimés, embossés, et moulés dans des formes non circulaires comme des ovales ou des carrés, permettant une grande liberté de branding. Coût annoncé d’une ligne de moyenne gamme «bottle to tube» avec coating plasma autour de 3,2 million US $ pour une production de 12.9 million de tubes par an ou 1620 tubes à l’heure. Delta Engineering finalisera l’an prochain la DTA-104 qui, avec quatre stations, sera présentée au K-Show et disponible en 2026.
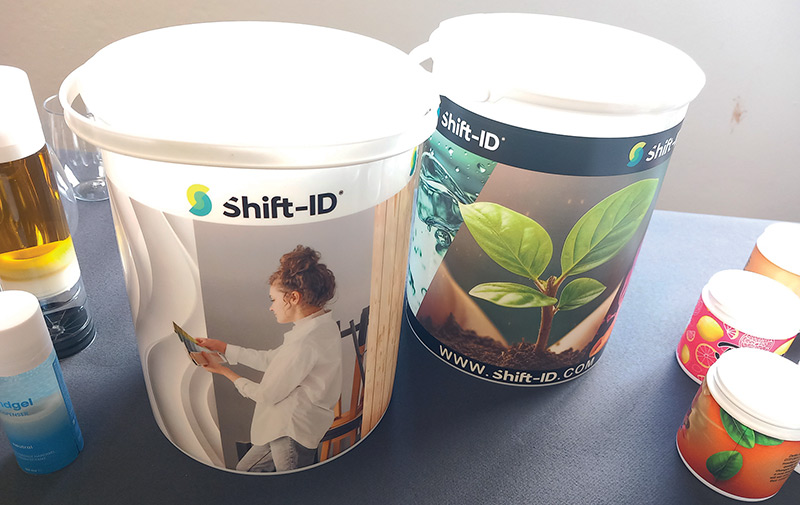
Impression digitale direct, nouvelle tentative
Quant à l’impression digitale sur bouteilles PET, plusieurs grands équipementiers allemands tels que Krones, Till, KHS et Tonejet se sont déjà essayés à la technologie sans réussir à convaincre nombreux porteurs de marque. Direct Print Powered by KHS est encore utilisé chez le brasseur belge Martens et DecoType de Krones fonctionne toujours chez Döhler, producteur d’ingrédients alimentaires mais en 2023 Krones a annoncé l’arrêt de production de cette technologie. Ces équipements à haute cadence sont destinés aux gros volumes. Cette fois, Shift-ID, la PME sud-africaine vise le haut de gamme et la petite série. Principal acteur du pays dans l’impression offset pour les seaux de peinture depuis 20 ans, Shift-ID se lance dans le défi du digital aux côtés de Delta Engineering. Ce partenariat exclusif a permis le développement en quatre mois de leur première machine d’impression digitale pour emballage polymère. Une gamme de machine pour plusieurs niches suivra dans les mois à venir. En démo, se trouvait la DTP 281qui imprimait en digital des petits raviers en PP. Le brevet étant en cours, les informations sur la machine sont restées limitées. Les quatre stades classiques se succèdent : alimentation des contenants, dépose du coating, impression, sortie et mise en caisse. Avec huit stations d’impression, bouteilles et containers entre 40 et 100 mm peuvent être traités et imprimés à des vitesses de 1700 à 5000 produits à l’heure. L’impression est réalisée à 2 mm de la surface de l’emballage, l’encre est disponible chez deux grands fournisseurs du marché. Selon Brian Murray Directeur de Shift+ID (en photo p.6), par rapport aux contenants en IML, les avantages sont majeurs en termes d’économie d’encre, et donc de prix. Pour les grands contenants on parle de 20 à 30% moins cher, et plus encore pour les petits emballages où le die cutting de l’IML alourdit le prix.