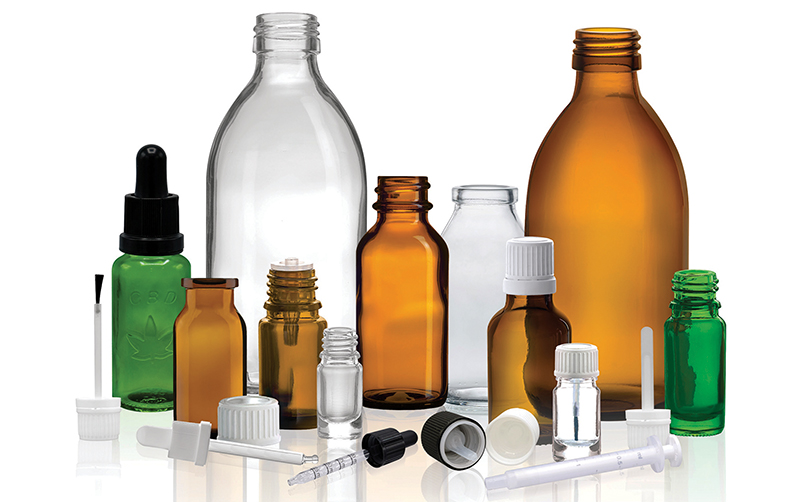
Le renouveau des flacons en verre
posted Thursday 30 November 2023
Abonnez-vous à la revue pour lire la suite de l'article
s'abonner
Contribuer au développement durable tout en gagnant en qualité et en performance : un pari en passe d’être remporté par la filière du verre pharmaceutique européenne. Pour y parvenir, les principaux verriers (Bormioli Pharma, Stoelzle Pharma, Schott) ont beaucoup investi (et continuent) dans leurs capacités de production, la décarbonation et l’innovation environnementale. Et cela, sur un marché post-covid en forte croissance et encore très tendu, tiré par les médicaments biotech et les produits OTC.
Si le Covid a mis à mal le modèle de «fabrication sur commande» traditionnel du verre pharmaceutique, selon Andrea Sentimenti, directeur marketing & innovation chez Bormioli Pharma, les verriers européens sortent plus forts et mieux armés de la crise sanitaire, ayant su répondre à la très forte hausse de la demande de flacons pour les vaccins et les médicaments dispensés dans les unités de soins intensifs. «Nous avons réagi rapidement en investissant dans de nouvelles installations et capacités de production, note-t-il. Ces efforts, combinés à de nouvelles solutions pour relever les défis logistiques liés à la chaîne du froid, ont permis de surmonter les pénuries». Les investissements récents dans les machines et systèmes d’inspection de dernière génération ont également entrainé «une élévation significative des normes de qualité», ce qui n’a fait que renforcer le positionnement leader de l’Europe, le plus grand producteur de verre au monde, concentrant un tiers de la production, selon Grand View Research. Aujourd’hui, les acteurs sont prêts à faire face à la croissance de la demande sur un marché mondial des emballages en verre pharmaceutique estimé à 18,26 milliards de dollars en 2022 et qui croît de 9,6% par an, selon le cabinet d’études.
Forte croissance sur tous les segments
Chaque type de verre possède ses propres caractéristiques chimio-mécaniques pour s’adapter aux formulations pharmaceutiques. «La demande de médicaments contre les rhumes, la toux et les infections des voies respiratoires, conditionnés dans des flacons ambrés de type III, a entrainé une hausse des ventes de 18,9% au deuxième trimestre 2023», indique Andrea Sentimenti sur la base des chiffres IQVIA. Cette tendance à la hausse devrait se poursuivre sur les prochains mois de saison grippale. En parallèle, le switch des médicaments sur prescription vers les produits en accès libre (OTC) est une tendance continue, avec une demande mondiale pour ces produits OTC qui va augmenter de 8,5% sur la même période pour atteindre 187 milliards de dollars (IQVIA). Les produits cosméceutiques et nutraceutiques (hybrides entre pharmaceutiques et cosmétiques) connaissent également de belles progressions, selon Stoelzle Pharma, fabricant de verre de type II et III.
A cela s’ajoute la montée en puissance des médicaments biologiques plus difficiles à fabriquer, stocker et administrer que les petites molécules, et conditionnés en verre de type I. La demande s’oriente vers les «médicaments biotechnologiques, thérapies géniques, traitements oncologiques et à forte valeur ajoutée», précise Andrea Sentimenti. Après un pic sans précédent lié aux campagnes de vaccination Covid, le marché du verre de type I a retrouvé son rythme de croissance antérieur avec une demande de «produits d’emballage en verre personnalisés et dotés de caractéristiques spécifiques pour relever certains défis, tels que le transport, l’intégrité et la manipulation du médicament». De son côté, le verre de type II maintient un taux de croissance constant, principalement lié à l’expansion des produits dérivés du sang.
Une innovation tirée par la qualité et l’environnement
Le moteur de l’innovation réside avant tout dans l’amélioration des caractéristiques du verre. «Le perfectionnement des traitements utilisés sur la surface interne des récipients en verre permet de faibles niveaux de seuil hydrolytique pour les flacons qui s’adaptent ainsi aux médicaments administrés par voie intraveineuse», note Andrea Sentimenti. Un autre axe d’amélioration est la résistance du récipient, notamment la surface externe du verre grâce à de nouvelles technologies telles que l’utilisation de couches minces de silicium, de l’oxygène par dépôt chimique en phase vapeur sous vide (procédé CVD) et plasma. «Comme les contenants sont soumis à des processus intenses tels que la stérilisation et dépyrogénation, l’objectif est de réduire les risques de casse en production, liés aux contraintes mécaniques et thermiques ainsi qu’aux chocs et éraflures», explique-t-il. Bormioli Pharma s’intéresse également aux technologies et processus qui permettent de réduire les substances lixiviables et extractibles, induisant des tests continus sur des échantillons afin de garantir la stabilité des formulations, de plus en plus agressives chimiquement. D’où le lancement de la nouvelle génération de flacons en verre Delta, avec des caractéristiques supérieures de neutralité chimique, d’absorption des chocs et d’écoulement sur les chaînes de montage.
Schott travaille également à améliorer en continu la formulation du verre, ses propriétés chimiques mais aussi géométriques et visuelles. Parmi les innovations les plus récentes, le fabricant vient de lancer Fiolax® Pro, un tube en verre borosilicaté de type I, supérieur chimiquement, avec un profil amélioré de lixiviables et extractibles et une résistance hydrolytique. Celui-ci est également exempt de métaux lourds. «Nous envisageons de le produire à l’avenir avec de l’énergie verte pour réduire considérablement l’empreinte carbone du produit», indique Patrick Markschläger, vice-président exécutif de l’activité Schott Tubing. Et pour améliorer la qualité, Schott a mis au point la technologie de fabrication intelligente perfeXion® «pour détecter même les plus petits écarts dans chaque tube, améliorant la qualité au-delà des normes industrielles».
La nouveauté chez l’autrichien Stoelzle Pharma est EcoSecur, un procédé innovant à la fois sûr, stable et économe en ressources, pour le traitement de la surface interne des flacons d’injection et de perfusion en verre de type II. «La technologie utilise un processus de traitement liquide qui permet un dosage précis adapté à la taille de chaque flacon, de 6 à 500 ml, indique Antonia Karamat, directrice adjointe des ventes monde pharma de Stoelzle. Le processus de fabrication surpasse les technologies précédentes en termes de qualité, stabilité et fiabilité». Grâce à EcoSecur, le verrier a réussi à réduire l’utilisation de composants chimiques jusqu’à 50% et les émissions de CO2 jusqu’à 80%. Stoelzle innove également avec PharmaCos, une gamme d’emballages pour les produits de bien-être et de santé (anti-âge, compléments nutritionnels, …) qui sont en forte croissance. «Celle-ci comprend une large gamme de pots de 5 à 500 ml et de flacons à épaule plate de 20 à 150 ml, disponibles en verre ambré et silex avec différentes finitions de col», annonce-t-elle. PharmaCosse concentre sur les secteurs nutraceutique et cosméceutique, pour lesquels la durabilité est une priorité avec une vaste gamme de pots et flacons à épaule plate fabriqués à partir d’une proportion importante de calcin de verre recyclé.
Optique décarbonation
Si la robustesse des flacons en verre ne fait plus de doute, l’industrie devra de plus en plus s’adapter aux exigences de durabilité environnementale. «Il existe déjà des gammes de produits en verre recyclé, notamment pour les types II et III, qui utilise des matériaux issus d’une chaîne d’approvisionnement externe certifiée pour un usage pharmaceutique», souligne Andrea Sentimenti. À l’avenir, l’objectif est d’élargir les sources d’approvisionnement en verre post-consommation, y compris les flacons en verre utilisés pour les produits pharmaceutiques, ce qui n’est pas autorisé aujourd’hui. «Mais d’un point de vue chimique, l’option est totalement sûre car le processus de régénération du verre comprend un point de fusion compris entre 1400 et 1600°C, une température qui garantit la stérilisation complète et l’élimination des impuretés des contaminants», précise-t-il.
Un autre sujet d’actualité
vise la décarbonisation de l’industrie, qui amène certains des plus importants verriers européens à étudier de nouveaux mélanges de combustibles pour leurs fours à verre, notamment les biocarburants, l’hydrogène, la fusion 100% électrique et les solutions de carburant hybride. La complexité d’une telle transition a motivé la création de consortiums industrie/académie, par exemple Glass Futures, une organisation à but non lucratif basée au Royaume-Uni, dont fait partie Bormioli Pharma, pour avancer sur de nouvelles technologies et processus industriels à faible émission.
«La question de la durabilité dans la production, les processus et la chaîne de valeur, est aussi essentielle chez Schott», selon Patrick Markschläger. Ces dernières années, le fabricant allemand a continuellement augmenté ses capacités de production, en se concentrant sur l’Asie. «Cette année encore, nous avons démarré la production avec une nouvelle cuve de fusion en Inde pour fabriquer l’ensemble de notre gamme de verre borosilicate Fiolax®», ajoute-t-il. Avec l’enjeu d’être carbone neutre dans la production d’ici 2030, Schott prévoit d’investir 40 millions d’euros dans un projet de construction d’une nouvelle cuve de fusion de verre à base d’électricité verte à Mitterteich, en Bavière. «Les émissions de GES seront réduites d’environ 80%», pointe-t-il.
Chez Stoelzle, les investissements actuels visent principalement à favoriser la décarbonisation avec des étapes importantes franchies cette année sur son site autrichien. «Nous avons investi 3 millions d’euros dans un préchauffeur de lots de pointe, qui utilise les gaz d’échappement chauds du four pour sécher et préchauffer les matières premières, explique Antonia Karamat. L’approche innovante réduit non seulement l’électricité nécessaire au boosting, mais aussi la consommation d’énergie d’environ 1,3% sur le site». Et cet automne, Stoelzle passera au premier doseur électrique sur l’un de ses fours, une étape importante sur la voie de la décarbonisation des procédés.