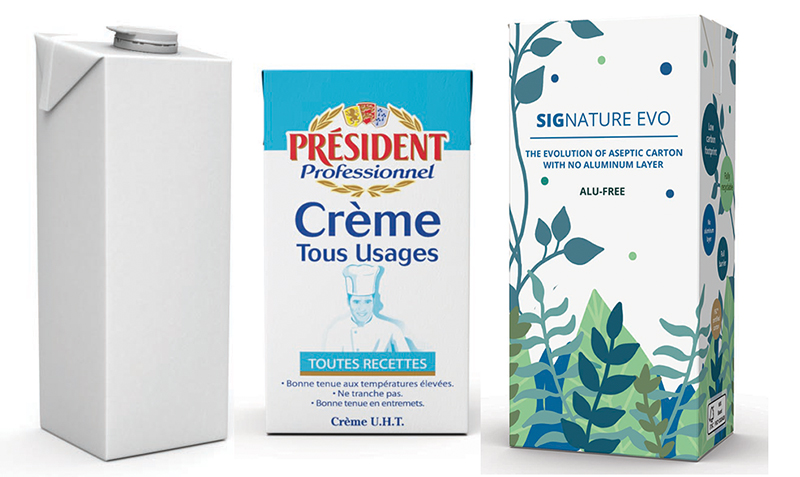
Les briques : objectif 100% fibres
posted Thursday 30 March 2023
Abonnez-vous à la revue pour lire la suite de l'article
s'abonner
Les fournisseurs de briques alimentaires visent d’augmenter au maximum le pourcentage de fibres dans les emballages. Leurs travaux portent, par ailleurs, sur la suppression du revêtement intérieur en aluminium, et l’utilisation de plastique végétal.
La brique suit l’évolution du marché, en baisse. «Cela dit, sur les deux segments principaux de la brique, le lait et les jus, la baisse est chronique : en cause, la disparition du petit-déjeuner – ou sa simplification. Le marché du lait accuse une baisse de 3% par an depuis dix ans. Quant au jus, on constate un recul de 15% en volume par an depuis 2015. La part de marché des briques a cependant tendance à se stabiliser dans ces deux secteurs ces dernières années. Elle se développe aussi sur de nouveaux marchés comme celui des eaux», remarque Carole Fonta, directrice générale d’Alliance Carton Nature (ACN), l’association réunissant les fabricants Tetra Pak, SIG et Elopak.
En termes de part de marché, 44% du lait consommé en France est en brique – le reste dans des bouteilles en PEHD principalement – et 38% des jus – la majorité est surtout conditionnée dans des bouteilles en PET. Le marché de la brique baisse d’environ 3% par an. Il est stable (à 90% de PDM) pour les soupes. «La France reste très consommatrice de plastique, même si la brique est bien perçue par le grand public. C’est un petit marché en France. Les pays du nord de l’Europe en consomment trois à cinq fois plus», souligne Carole Fonta. Selon Citeo, 70 000 tonnes de briques ont été commercialisées en France en 2021, dont 40 000 tonnes collectées en vue de leur recyclage.
Côté recyclage, la fibre des briques est intégralement recyclée en produits d’hygiène et d’essuyage. Quant au PolyAl (mélange de plastique et aluminium, qui compte pour 25% de la composition d’une brique), actuellement un tiers est recyclé en divers produits – mobilier urbain et palettes notamment, le reste est majoritairement incinéré. Les fabricants et les recycleurs collaborent dans le but de pouvoir recycler 100% de ce PolyAl d’ici 2025. De nouveaux procédés de recyclage ont été développés ces dernières années afin de permettre de séparer ses différents composants (PEBD du corps des briques, PEHD des bouchons et aluminium) pour augmenter la valeur des débouchés.
Augmenter la part de fibres
« Deux facteurs influent sur l’innovation : la règlementation, et l’impact environnemental de la production alimentaire, qui représente 25% des gaz à effet de serre dans le monde. Tetra Pak, ainsi que ses clients, doivent donc limiter leur utilisation de ressources, notamment d’origine fossile, pour améliorer à la fois leur efficacité opérationnelle et leur empreinte carbone. En termes de solution d’emballage, nous avons l’ambition de développer une brique alimentaire provenant entièrement de matières renouvelables ou recyclées, à faible empreinte carbone. Pour cela, nous avons prévu d’investir 100 millions d’euros par an, sur les cinq à dix prochaines années. Et à l’horizon 2030, nous visons de proposer un emballage utilisant au maximum des matériaux issus de la fibre dans sa composition», révèle Sarah Nerbonne, directrice marketing France et Benelux pour Tetra Pak. Le groupe vient d’ailleurs d’annoncer le lancement d’une recherche inédite sur l’emballage alimentaire à base de fibres, en collaboration avec le laboratoire suédois MAX IV qui abrite une nouvelle station de recherche consacrée à l’étude des matériaux issus de la forêt. L’objectif de cette recherche est de découvrir de nouvelles perspectives sur la nanostructure des matériaux en fibres, avec une première application visant à optimiser la composition des matériaux utilisés pour les pailles en papier.
Une brique d’un litre se compose d’environ 75% de papier, 21% de plastique, et 4% d’aluminium. Depuis quelques années, Tetra Pak propose des briques contenant du plastique d’origine végétaleavec un approvisionnement ségrégué, tout en restant compatible avec la filière de recyclage en place. Cette action permet une réduction de 15 à 30% de CO2 à l’emballage, certifiée par l’organisme indépendant The Carbon Trust. Autre option : intégrer du plastique recyclé attribué, dit «circulaire» car favorisant l’incorporation de matériaux recyclés dans les chaines de valeur. Cette alternative a été choisie par les marques de crème Elle&Vire et Lactalis sur ses références en bio.
Supprimer la couche d’aluminium
Tetra Pak teste par ailleurs la substitution de la barrière aluminium (qui pèse pour 30% des émissions de CO2 de la brique) par une barrière à base de fibre. «Nous avons introduit en Asie une barrière à base de PET en 2020, pour apprendre sur le remplacement de la barrière aluminium. Mais la barrière PET n’est pas compatible avec les filières de recyclage en Europe. La barrière à base de fibres, compatible avec la filière de recyclage, maximise en plus la valeur de la brique pour les recycleurs», note Sarah Nerbonne. La France compte deux recycleurs papetiers – Lucart et Essity – chez lesquels la majorité des briques alimentaires sont envoyées. Des investissements sont en cours pour augmenter les capacités de recyclage des éléments non-fibreux de la brique, c’est-à-dire les couches de plastique et d’aluminium. «D’ici 2025, l’ambition est de recycler l’intégralité des éléments issus de la collecte. L’enjeu majeur est de continuer d’augmenter cette dernière, qui était à hauteur de 57% en France en 2021», ajoute-t-elle.
Depuis 2020 chez l’entreprise SIG, 100% de l’aluminium acheté pour ses briques en Europe est certifié ASI (Aluminium Stewardship Initiative), ce qui garantit une utilisation «durable» de la ressource – de l’extraction de la matière jusqu’au processing. Dès 2010, SIG proposait aussi la brique combibloc ECOPLUS, dont la structure ne comporte pas de couche d’aluminium. En 2017, la société a mis au point un emballage en carton aseptique sans aluminium, fabriqué à partir de polymères contribuant à développer une filière de polymères végétaux, issus de la filière bois (de l’huile de tall), selon une approche certifiée d’équilibre des masses. La marque Candia a été la première à adopter le pack SIGNATURE 100 en France. «Ces structures sans couche d’aluminium sont bien adaptées au lait UHT, non sensible à l’oxygène, protégeant ainsi le produit pendant environ six mois. Pour les autres boissons sensibles à l’oxygène, comme les jus ou les laits aromatisés, SIG développe une autre
structure sans couche d’aluminium, baptisée SIGNATURE EVO. La barrière est composée d’un autre type de polymère. La structure SIGNATURE EVO sera disponible avec des polymères classiques ou des polymères d’origine végétale selon une approche certifiée d’équilibre des masses», explique Mélanie Révolte, responsable marketing France de SIG. La société continue d’œuvrer pour réduire la part de plastique dans ses emballages : «cela passe par le choix des matériaux, la structure de la brique… Nous visons d’atteindre environ 90% de fibres dans nos emballages d’ici 2030», ajoute-t-elle.
Investissements pour améliorer les procédés industriels
Le groupe suisse poursuit ses investissements. Il vient d’annoncer la construction d’un nouveau site en Inde – son premier site de production de contenants en carton aseptiques, pour fournir les producteurs indiens de produits laitiers et de boissons non gazeuses. L’investissement s’élève à 60 millions d’euros entre 2023 et 2025, pour cette usine qui produira à terme jusqu’à 4 milliards d’unités par an. Par ailleurs, SIG a investi sur son site en Suisse prés de Zurich (Neuhausen) pour la production de bouchons attachés. «Nous avons mis au point un système polyvalent afin de permettre à nos clients de limiter leurs investissements pour passer d’un bouchon classique à un bouchon attaché selon les séries», précise Mélanie Révolte. La société a, en outre, développé une solution machine pour produire un nouveau format de brique d’un
litre, dotée d’un bouchon à large ouverture. Cette nouvelle génération de machine sera plus rapide, plus économique et plus durable (en termes d’énergie, d’eau, de consommables…). Quant à l’usine Tetra Pak de Dijon, qui fabrique 3 milliards de briques par an, elle a servi en 2022 de pilote pour un processus d’impression par flexographie sans solvant, à base d’encre à l’eau. Le site
Tetra Pak de Chateaubriand, qui produit 4,5 milliards de bouchons chaque année, a lui bénéficié de 100 millions d’euros d’investissement pour fabriquer des bouchons solidaires – dont la présence sur les emballages concernés sera une obligation légale à partir de juillet 2024.