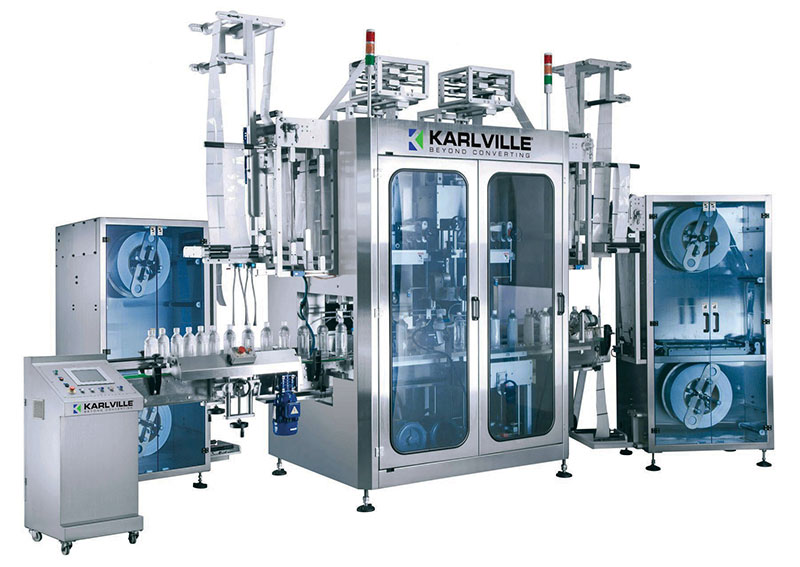
Les manchonneuses face aux enjeux de durabilité
posted Monday 30 September 2024
Abonnez-vous à la revue pour lire la suite de l'article
s'abonner
Le développement de manchons plus facilement recyclables ou intégrant du recyclé a amené les constructeurs à adapter leurs machines. Objectif : ne faire aucun compromis sur la cadence et la qualité de pose, tout en intégrant de nouvelles fonctionnalités et en réduisant l’empreinte carbone de leurs lignes.
Karlville travaille la machinabilité des nouveaux matériaux
Face à un marché du sleeve à la recherche d’un second souffle, trois leviers de croissance se veulent encore moteurs pour cette famille de produits : le sleeve en polyoléfine qui continue à gagner des parts de marché, de la même façon pour le rPET. Le manchon en tant qu’élément d’inviolabilité pour des produits cosmétiques, de santé ou des vins & spiritueux se dessine comme un autre relai de progression face au sleeve pour regroupement promotionnel attaqué frontalement par des solutions papier/carton ces dernières années, analyse Karlville. «L’on voit se créer de nouvelles opportunités pour le sleeve. Dans le secteur de la détergence ou des lessives comme récemment pour Lénor, il apporte une fonction barrière et permet de se passer de bouteilles opaques», constate Laurence Corbet, directeur technico-commercial Karlville Europe.
Côté machines, le constructeur travaille en étroite collaboration avec les fabricants de résines et de films pour tester leur machinabilité. Objectif : améliorer la technicité des matériaux lors d’étapes clés comme la découpe, la soudure, le scellage, l’application ou la rétraction du manchon. Karlville accompagne aussi les clients sur le passage du PET au rPET ou aux polyoléfines, en adaptant les process des lignes sans impacter la cadence. «S’orienter vers ces manchons demande une courbe d’apprentissage pour tous les acteurs, que ce soient les fabricants de films, les constructeurs de machines ou leurs utilisateurs», explique Laurent Corbet. Autre récent développement : la mise au point d’un système de division de lignes avant le manchonnage. En passant de 1 à 2 lignes par exemple, il est possible de s’affranchir de plusieurs mètres de convoyeurs avant la pose de manchons d’inviolabilité. «Ces derniers réclament beaucoup de régularité lorsqu’il s’agit de produits de santé, techniques et de petite taille. Cette expertise nous a permis de gagner de beaux projets, notamment dans le secteur des collyres ophtalmiqueset prochainement dans celui des flacons avec pipettes», indique le représentant de Karlville. Enfin, l’entreprise peut s’appuyer son tunnel de rétraction Tornadofaisant appel à de l’IR «nouvelle génération» pour réduire la consommation énergétique et réduire la longueur des tunnels.
PDC Europe mise sur la synchronisation électronique et l’IA
Basé à Montdidier dans la Somme, le spécialiste depuis 40 ans de la pose de sleeve étirable ou thermo-rétractable PDC Europe réalise 90% de son CA à l’export. L’entreprise familiale créée par Jean-Claude Vandevoorde – désormais dirigée par son fils Derek Vandevoorde – conçoit des machines de pose de manchon couvrant les trois principaux besoins du marché, que sont la protection des produits (inviolabilité), leur décoration et leur conditionnement (mise en lot). Le constructeur se démarque par son modèle d’intégration verticale : ses deux usines du groupe dessinent, fabriquent les pièces et les armoires électriques, assemblent, montent et installent l’ensemble des machines commercialisées. Chaque étape clé étant réalisée en interne par des spécialistes.
«Nos clients sont la recherche d’investissements sécurisés qui vont durer dans le temps, tout en ayant un coût de production le plus faible possible. Les machines faible consommation sont plébiscitées pour réduire leur bilan carbone ainsi que des consommables recyclables. Consommer la juste énergie est dans notre ADN depuis nos débuts. Nous sommes à notre 5e génération de tunnels à air chaud recyclé, à faible consommation d’énergie car on réinsuffle l’air chaud de la chambre dans des résistances développées en interne. Enfin, tous nos tunnels sont équipés de solutions d’isolation thermique très efficaces pour ne pas disperser cette énergie. Une conception qui permet d’économiser jusqu’à 40% d’économie d’énergie vapeur pour une longueur similaire», détaille Derek Vandevoorde, pdg de PDC Europe.
Avec une activité en forte progression, la PME a recruté dix nouveaux salariés en moins d’un an sur plusieurs postes de l’achat à l’automatisme en passant par le bureau d’études. «De nouveaux marchés s’ouvrent pour le manchon étirable en PE transparent ou teinté dans la masse sur le secteur de l’industrie agro-alimentaire, les marques recherchant des soutions de décoration recyclables, facilement séparables, sans colle ou encres perturbatrices», confie le dirigeant. Côté machine, PDC Europe a récemment apporté plusieurs optimisations. En utilisant la synchronisation électronique de tous les mouvements, le constructeur réduit le nombre de pièces mécaniques nécessaires et peut ajouter de nouvelles fonctions intégrées à la machine sans besoin de blocs supplémentaires. Autre avantage : communiquer également plus facilement avec des éléments périphériques comme un robot par exemple qui serait alloué à la formation de lot avant de passer par la manchonneuse. En complément, PDC Europe a développé une gamme de convoyeurs et a breveté SURE, un système universel de rejet électronique brushless de produits non conformes. Deuxième axe de développement : l’intégration d’IA dans les caméras de vision afin d’offrir un contrôle qualité du sleeve désormais après rétraction. «Avant l’IA, on confirmait seulement au client que le manchon était présent et au bon endroit. Désormais, on peut aussi s’assurer qu’il est bien orienté, bien rétracté et que les éventuelles perforations nécessaires sont aussi présentes. En alimentant des occurrences dans une base de données, le système nous permet d’être encore plus précis sur les critères suivis de qualité. Il s’agit du fruit d’un long travail de collaboration avec le CEA Tech, entamé depuis
cinq ans. La technologie est désormais assez mature pour être commercialisée. Elle est proposée en option pour des produits à forte valeur ajoutée où le souci du détail est important comme pour les produits cosmétiques par exemple», ajoute le pdg.
Sleever® répond aux attentes du full-service haute cadence
Très exigeants, les sous-traitants en marque blanche – un secteur caractérisé par du multi-référencement et du multiproduits – sont à la recherche de solutions machines capables de répondre à un ensemble de besoins : un time to market court, des prix compétitifs et des produits éco-conçus. Les lignes de conditionnement recherchées doivent donc être souples, rapides et afficher une faible consommation en énergie. Objectif : garantir une prestation de service de qualité tout en optimisant la supply chain. En combinant un sleeve de 20 microns avec une Duo Combisteam LWPET®FB1100-A300, Sleever® a pu satisfaire cette demande en développant de A à Z une ligne haute cadence (1100 cp/min) à rétraction vapeur pour la pose de sleeve «full body» de produits probiotiques laitiers.
De dernière génération, le sleeve LWPET® choisi pour ce projet affiche l’épaisseur la plus basse du marché à ce jour : 20 microns (les standards avoisinant les 40 microns). Résultat : une empreinte carbone réduite de moitié et une optimisation de l’ensemble de la chaine logistique.
Côté machine, la conception modulaire et linéaire intègre un châssis tout inox, entièrement cartérisé adapté aux nettoyages fréquents. Le design de cette machine apporte une empreinte au sol réduite avec deux têtes de pose décalées et deux tunnels de rétraction assemblés sur un seul châssis permettant de réaliser deux machines en une. Son ergonomie et ses fonctionnalités ont été étudiées pour optimiser les temps d’intervention de l’opérateur sur le cycle de production, notamment grâce à la présence des deux magasins multi-bobines permettant de suivre la cadence et libérer l’opérateur du poste de chargement d’alimentation bobines.
Les outillages dédiés pour chaque produit permettent de réduire les temps de changement de format. En cas de dysfonctionnement sur l’une des deux têtes de pose, la carterisation sur l’ensemble du parcours produit de chaque tête permet de ne pas arrêter la machine même en cas d’intervention sur l’une d’entre elle. La conception de la machine réduit aussi les temps d’intervention lors des vides de ligne. L’efficience de la ligne est donc optimisée.
Pour réduire les consommations d’énergie, la structure des tunnels de rétraction a été conçue pour garantir une isolation optimum et permettre un ajustement de la consommation vapeur pour chaque format. «Cette conception unique de nos tunnels de rétreint combiné à une faible épaisseur du
film permet de réduire de 60% la consommation énergétique de notre solution», déclare
Bruno du Plessix, responsable développement business chez Sleever®. L’ensemble permet d’obtenir une efficience de 98% à 1100 cpm avec un sleeve d’une épaisseur de 20 microns. «Une première mondiale, aucune machine aujourd’hui ne tourne à une telle vitesse en utilisant un sleeve d’une épaisseur 20 microns», indique Sleever®. Une 2e ligne est en commande pour un grand nom des PGC. Une solution qui répond parfaitement aux besoins des acteurs du marché laitierqui requièrent une très haute cadence. Et qui pourrait également trouver sa place chez les industriels en hygiène/beauté et en détergence, même si les cadences recherchées restent moindres.