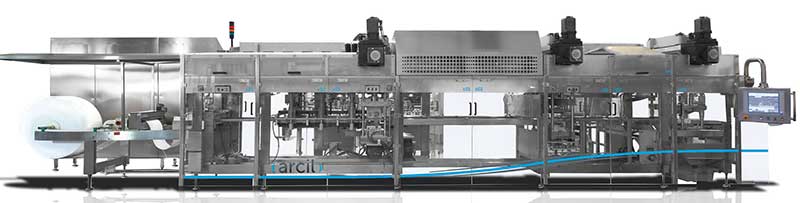
Les solutions FFS évoluent lentement, mais sûrement
posted Thursday 31 August 2023
Abonnez-vous à la revue pour lire la suite de l'article
s'abonner
Nouveaux matériaux, nouvelles applications et associations fonctionnelles… : les machines de conditionnement Form-Fill-Seal, jusqu’à présent réputées peu flexibles, tendent à le devenir davantage pour mieux satisfaire les utilisateurs.
« Notre marque phare pour les systèmes Form-Fill-Seal, c’est Arcil, mentionne d’emblée Fabien Jego, chef de produits FFS chez Synerlink (groupe Barry-Wehmiller). Dans ce domaine, s’il n’y a pas de nouvelle référence machine depuis l’Arcil 7(jusqu’à 40 000 pots/h), on enregistre cependant des progrès notables, par exemple le fait d’accepter désormais le PET pour la fabrication de packs sécables et plus seulement le PS avec décor papier comme c’était le cas auparavant». Et d’expliquer que cette avancée a été obtenue notamment grâce à des efforts de R&D effectués au sein de la filiale Sogameca et ayant abouti à la mise au point des outils de découpe Snapcut, caractérisés par des durabilités de 10 millions de coups, soit 5 000 heures de production avant ré-affûtage.
Autre tendance : l’étiquetage dans le moule (IML) avec des étiquettes en polystyrène de façon à donner aux industriels la possibilité de mettre en œuvre des emballages recyclables 100% PS (pot, décor et opercule). «D’une façon générale, si les solutions FFS pâtissent tout comme les autres du plastic bashing, elles se distinguent néanmoins par un impact carbone modéré du fait qu’elles suppriment le transport des pots préformés vides, qu’elles sont compatibles avec l’ultra-propreté sans dépense d’énergie supplémentaire pour décontaminer le plastique, et enfin qu’elles ne réclament pas de carton pour le suremballage des multipacks», insiste le chef de produits.
Fabien Jego observe par ailleurs un intérêt croissant des donneurs d’ordres pour la rénovation des machines, avant réemploi : «la durée de vie mécanique de nos systèmes est d’une trentaine d’années alors que les premiers problèmes d’obsolescence électronique surviennent parfois au bout de dix ans. C’est pourquoi notre service upgrade prend les devants et contacte directement les clients, qui profitent bien souvent de la nécessité d’un retrofit pour adapter leurs équipements à de nouveaux matériaux ou à des esthétiques d’emballages plus attrayantes».
De l’importance de l’interfaçage entre le thermoformage et le remplissage
Constatant lui aussi la désaffection des utilisateurs vis-à-vis du PS dans les nouveaux projets FFS, Eric Maussion, directeur général d’Illig France, met en avant la capacité actuelle de machines telles que la FSL 48à produire – là encore au moyen d’un outil de découpe spécifique – des multipacks en PP et PET standard parfaitement sécables : «en outre, nos systèmes FSL (avec un L pour Labeling) conçus pour le PP intègrent l’IML, ce qui veut dire qu’ils mettent en forme des emballages mono-matériaux écoresponsables. Petit bémol : dans ces conditions, la cadence admissible avec le PP n’est plus de 28 cycles/minute comme avec le PS, mais de 25 cycles/minute».
Ceci dit, s’il faut chercher un point faible aux FFS, il n’est pas relatif aux cadences mais plutôt à la flexibilité, aux changements de formats… «C’est sur ce thème que les utilisateurs demandent aujourd’hui aux fabricants de faire des propositions, et chez Illig nous le faisons avec un nouveau concept baptisé Flexibel», annonce le dirigeant. À gros traits, l’idée consiste à interconnecter une thermoformeuse Illig de type RDM, réputée justement pour sa flexibilité, en formats et matériaux (avec intégration possible des procédés de décoration Illig IML-T® ou PML®), à une machine Fill-Seal du marché. «Ce qu’il faut comprendre, c’est que les performances de l’ensemble vont dépendre étroitement de la qualité de l’interfaçage, de la façon de gérer l’accumulation des pots en sortie de thermoformeuse, etc. C’est tout cela que recouvre le concept Flexibel».
Les atouts du convoyage électromagnétique
L’agilité fait également partie des sujets du moment chez PFM Packaging Machinery. L’une des voies retenues par ce fabricant d’équipements de conditionnement pour emballages souples est le transport électromagnétique des objets tel qu’on l’a vu apparaître il y a quelques années chez Beckhoff, B&R Automation ou encore Rockwell Automation. «Mis en œuvre sur nos machines horizontales de la gamme D-Series(avec un D pour Doypack), ces chariots indépendants montés sur modules magnétiques, totalement désynchronisés par rapport au reste de la ligne, ont pour effet d’en optimiser la cadence d’utilisation, indépendamment du temps de cycle théorique», expose Frédéric Mauclair, directeur général de PFM Packaging Machinery France. Pour illustrer le surcroît de flexibilité apporté par de tels systèmes de transfert, le directeur général précise qu’il devient possible avec eux de faire varier le nombre de sachets traités au cours de la même opération (en ajustant éventuellement leur largeur) alors que ce nombre est immuable avec un système de transport traditionnel (un seul sachet en version Simplex, deux sachets en version Duplex et trois sachets en version Triplex).
En ce qui concerne les FFS verticales, Frédéric Mauclair signale le lancement d’un nouveau modèle dans la série RQ : la 550 Nano. «Avec une hauteur de chute réduite à 400 mm, cette machine cible le conditionnement de produits fragiles (chocolats, gaufrettes, snacks…) avec des dimensions de sachets relativement importantes puisque la laize peut aller jusqu’à 550 mm. Et à cela s’ajoute une grande diversité de sachets (coussin, fond plat, quatre coins soudés ou encore Doy Style avec ou sans zip)».
Densification des produits pulvérulents
Du côté des Établissements Prud’homme, Calixte Claux présente pour sa part la nouvelle version de la Concetti Continua, une FSS monobloc six stations dédiée à la mise en sacs de produits pulvérulents.
«Conçue à l’origine pour le conditionnement du ciment, cette machine, dotée d’un dispositif de nettoyage automatique par buses d’air, a été repensée pour les applications alimentaires au niveau des joints, de la visserie, des zones de rétention, etc.», commente le responsable commercial. Ainsi modifiée, la Continua peut sans problème ensacher des additifs et autres prémix en poudres fines. «L’un de ses points forts est l’emploi d’une canne de désaérationmicroperforée pour aspirer l’air à l’intérieur du produit et in fine réduire le volume de l’emballage. Pour accélérer le processus, le système de dosage peut opérer en deux temps, avec une phase complémentaire intervenant sur une station dédiée après tassage du sac et avant désaération finale si nécessaire», poursuit Calixte Claux. Remplis à une cadence d’environ 500 unités à l’heure (pour une masse typique de 25 kg) s’ils sont hermétiquement fermés (jusqu’à 800 unités/h sinon), les sacs en question, de format carré avec soudures en K, sont réalisés à partir d’une gaine préformée en PE standard (sans micro-perforations de ventilation) d’une épaisseur de l’ordre de 100 micromètres.