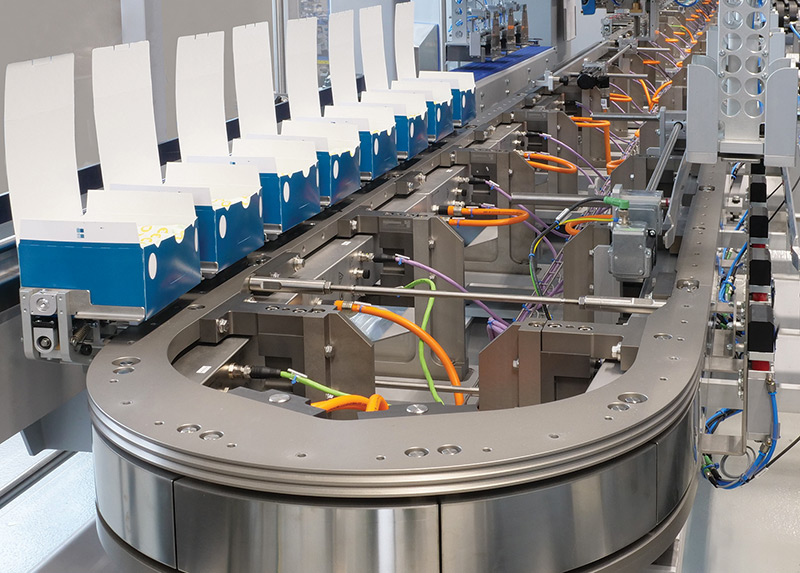
Lignes complètes : l’agilité des flux fait la différence
posted Sunday 12 January 2025
Abonnez-vous à la revue pour lire la suite de l'article
s'abonner
Convoyeurs magnétiques intelligents, navettes de transport robotisées, robots collaboratifs mobiles… les fournisseurs de lignes complètes se démarquent en innovant dans la transitique.
Les périodes incertaines comme celle que vit actuellement l’industrie française sont paradoxalement loin d’être défavorables aux projets de lignes complètes. C’est en tout cas ce qu’observe Frédéric Mauclair, directeur général de PFM Packaging Machinery France : «l’investissement est certes potentiellement important, mais le retour financier est attractif, avec par ailleurs une gestion de projet aisée pour l’acquéreur puisque le nombre d’interlocuteurs est réduit. Par conséquent, dès lors que la décision d’achat est prise, tout peut aller assez vite, ce qui rassure les investisseurs. Et de fait, nous livrons régulièrement des lignes complètes !».
Dans cet exercice, le groupe PFM met principalement à profit son expertise de l’emballage souple (tant primaire que secondaire) pour construire des lignes pouvant en plus intégrer des dispositifs de pesage ainsi que des îlots robotisés dédiés à la manipulation des produits, et allant jusqu’à la mise en caisse ou en présentoir si nécessaire. «Nous sollicitons des partenaires pour certaines fonctions mais faisons en général appel aux solutions émanant des différentes sociétés du groupe».
Chariots magnétiques
Parmi les secteurs les plus demandeurs de lignes complètes en ce moment, Frédéric Mauclair cite la biscuiterie, connue pour ses exigences en matière de flexibilité. «Les clients veulent pouvoir décliner facilement leurs productions en sachets coussins, sachets quatre coins soudés ou autres sachets à fond plat. Et cela tombe bien car c’est exactement ce que nous leurs proposons avec notre système QRM (Quick Release Module)qui permet d’embarquer toutes les pièces de pliage utiles et déjà préréglées dans la machine, de telle sorte qu’il n’y a rien à faire lorsque l’on passe d’un sachet à l’autre, si ce n’est changer de pièce de format et redémarrer».
En ce qui concerne le transport, cette quête de flexibilité peut également passer par l’utilisation de chariots magnétiques. «Ces convoyeurs offrent de nouvelles cinématiques et donc de nouvelles façons de résoudre les problèmes de gestion de flux. C’est une technologie que nous intégrons de plus en plus et avons appris à maîtriser il y a déjà plusieurs années en collaborant avec divers fournisseurs, et qui se développe actuellement».
Optimisation du timing
Un intérêt que partage Pierre Therville, responsable de la filiale française de Cama, en prenant l’exemple de la MTL Monoblock, une machine capable de gérer simultanément trois types de produits et formats d’emballage en carton. «Avec sa capacité totale de traitement de 1800 produits/minute, ses trois alimentations séparées, ses possibilités de panachage et son évolutivité, la MTL représente l’état de l’art de Cama dans le registre de la production adaptative, notamment grâce à la mise en œuvre d’une boucle de navettes électromagnétiques indépendantes ACOPOStrak, réalisée par B&R Industrial Automation». Et d’expliquer que la MTL Monoblock est ainsi en mesure de tirer le meilleur parti du timing de chaque station dans l’objectif d’augmenter la productivité globale. Une efficience que Pierre Therville juge tout à fait adaptée aux contraintes des secteurs agroalimentaires «en tension», par exemple celui de la nourriture pour animaux de compagnie qui doit répondre au succès grandissant des assortiments de recettes dans le même suremballage.
Modularité
Tout comme PFM, Cama fabrique en interne les robots qui remplacent désormais une bonne partie des mouvements mécaniques traditionnels. Ce qui ne l’empêche pas de nouer des partenariats pour atteindre certains niveaux de performances ou sur d’autres gammes, l’un des derniers en date étant celui conclu avec Autonox Robotics. «Notre force dans les lignes complèteset le sur-mesure en général, c’est d’une part l’épaisseur de notre portefeuille de solutions mobilisables dans les différents domaines de l’emballage (étuyage, formage, encaissage, wrap-around, fermeture, suremballage, etc.), et d’autre part le caractère modulaire de notre architecture. Si bien qu’en fonction des contraintes et des souhaits de nos clients, notamment en termes de compacité, nous pouvons répondre à ses demandes aussi bien par un ensemble de machines indépendantes que par une approche monobloc qui aura l’avantage de minimiser le convoyage».
Robots mobiles de transport
Pour Charles-Antoine Freiher, responsable commercial France/Espagne de la société Gerhard Schubert, ce sont d’ailleurs les techniques de transport utilisées au sein des lignes complètes qui, aujourd’hui, creusent souvent l’écart d’une réalisation à l’autre sur le plan de l’ergonomie, de l’agilité, des coûts de maintenance, etc. D’où l’importance de l’ingénierie dans la mission de Schubert Packaging Systems, l’entité en charge de la fourniture de lignes clé en main à l’intérieur du groupe. «La révolution en marche, c’est dans l’intelligence des flux qu’elle réside. En mettant par exemple à contribution – comme nous le faisons dès à présent suite à notre partenariat avec Carrybots – des robots mobiles de type AGVentre certains îlots de production en lieu et place des convoyeurs». Dans l’agroalimentaire, le responsable commercial ne croit cependant pas aux vertus des systèmes de transfert à moteurs linéaires proposés par plusieurs spécialistes des automatismes : «ces systèmes sont performants en vitesse et en accélération, mais s’avèrent limités en charge, en longueur et en évolutivité, sinon à des coûts prohibitifs». Depuis 2009, Schubert propose quant à lui le «robot de transport agile» Transmodul, alimenté par induction électromagnétique et capable de se déplacer librement sur une voie de roulement. «Nous avons fait en sorte que l’architecture Transmodul soit redondante, ce qui signifie que la panne d’un module n’a pas de conséquences sur la disponibilité de la machine. Selon nous, il s’agit d’une technologie qui répond donc parfaitement aux attentes de nos clients, tant en termes d’efficacité que de coûts».
Réseau neuronal
Pour les fonctions de pick and place, Schubert a également dévoilé sous le nom de tog.519un robot collaboratif mobile caractérisé par une vitesse particulièrement élevée (jusqu’à 90 coups/minute) et une remarquable facilité de programmation : «contrairement aux cobots classiques, le tog.519 n’est pas programmé par apprentissage mais par intelligence artificielle, via un réseau neuronal. En pratique, à partir d’un certain nombre d’images des produits et de l’environnement de production, le tog.519 est à même d’élaborer de façon autonome le meilleur scénario possible correspondant à sa tâche (prise/dépose de produits, séparation, réorientation, tri…), et de le remanier ultérieurement si nécessaire». Cette simplicité de mise en action le rendrait idéal pour gérer des changements de production, mener à bien une campagne promotionnelle limitée dans le temps, voire faire face à une défection de personnel.