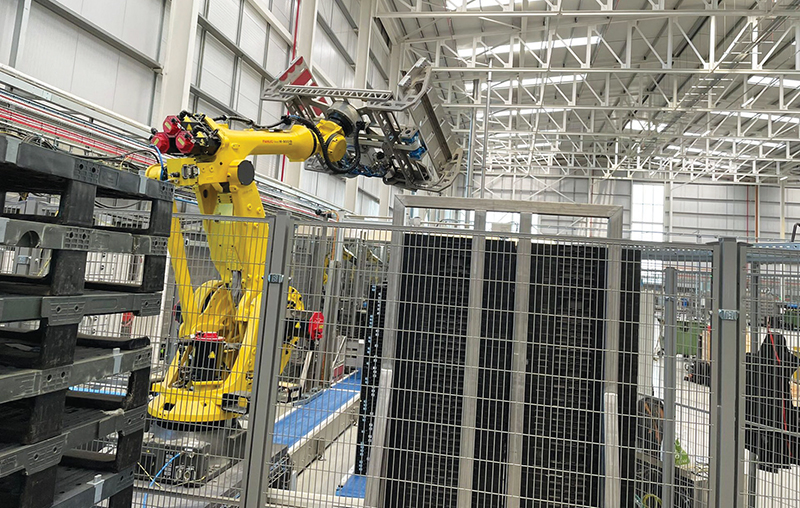
Réemploi des emballages industriels : les investissements se poursuivent
posted Saturday 30 September 2023
Abonnez-vous à la revue pour lire la suite de l'article
s'abonner
Si le débat réemploi vs. recyclage des emballages ménagers fait actuellement couler beaucoup d’encre dans le cadre du PPWR, la question de la réutilisation des emballages industriels et logistiques est également d’actualité avec l’arrivée de la future REP EIC (Emballages Industriels et Commerciaux) en 2025. De nombreux acteurs (IFCO, IPP, Tosca, LPR, etc.) n’ont pas attendu pour œuvrer à la mise en place de systèmes de location de contenants adaptés aux besoins de la chaine logistique, et poursuivent leurs investissements pour automatiser leurs centres et réduire l’empreinte carbone de leurs systèmes.
IFCO optimise en continu son système SmartCycle
Aujourd’hui, avec un parc de plus de 370 millions d’emballages réutilisables en circulation et 80 sites de lavage pour une capacité de nettoyage de 2 milliards d’unités par an, IFCO livre des bacs réutilisables dans plus de 50 pays et travaille en étroite collaboration avec plus de 18 000 producteurs et plus de 550 détaillants dans différents secteurs alimentaires (des fruits et légumes à la viande, en passant par les produits de la mer et les produits de boulangerie). «Maximiser l’efficacité de la supply chain avec notre système unique de location-gestion est une situation gagnant-gagnant. Basé sur notre mode de fonctionnement baptisé SmartCycle, le système de mutualisation et de location-gestion des bacs plastique réutilisables d’IFCO permet d’optimiser l’efficacité de la chaîne d’approvisionnement alimentaire de nos clients et de leur faire réaliser des économies logistiques significatives», commente Anastasios Papadopoulos, vice-président de la productivité des actifs et de l’exécution de la logistique chez IFCO. Côté coût, le pooler estime que son système permet de réduire les coûts de ses clients de 27% par rapport à des emballages à usage unique, qui sont certes moins chers à l’achat, mais engendrent un coût de collecte et de traitement en fin de vie. Grâce au déploiement de la plateforme numérique MyIFCO dans 30 pays, les clients peuvent gérer et suivre l’ensemble de leur parc de contenants à distance. Autre atout de taille selon IFCO : «le degré élevé de standardisation de nos solutions présente des avantages logistiques considérables et ce à toutes les étapes de la supply chain (de la livraison des bacs propres aux producteurs, à l’acheminement vers les plateformes logistiques des détaillants jusqu’à la livraison des produits aux points de vente). En cela, elles sont particulièrement adaptées aux entrepôts automatisés, qui rendent le tri, le stockage et la préparation des commandes plus efficaces», ajoute le porte-parole d’IFCO. Raison pour laquelle la société développe en permanence ses bacs réutilisablesafin qu’ils économisent l’espace autant que possible, comme le fait sa gamme Lift Lock. «Avec seulement 28 mm de haut une fois replié, il s’agit actuellement du modèle de caisse le plus plat d’Europe et constitue notre produit phare. Grâce à leurs dimensions réduites, les palettes peuvent contenir davantage de bacs réutilisables, augmentant ainsi l’optimisation des coûts logistiques», ajoute Anastasios Papadopoulos.
Tosca mise sur l’automatisation de ses centres de lavage
Tosca s’est récemment équipé d’un centre de lavage automatisé de pointe à Dublin. L’installationpeut traiter 5 000 contenants en plastique réutilisables par heure, soit plus du double de ce qu’une ligne standard peut traiter. L’investissement permet de pallier le manque d’opérateurs et les difficultés de recrutement et minimise les risques de contamination croisée puisque l’équipement permet d’effectuer les opérations sans aucune intervention humaine. Avec moins de quatre personnes, les contenants pliables sales sont chargés et empilés sur une palette à une extrémité de la ligne, et déchargés entièrement propres, empilés et prêts à l’emploi à l’autre extrémité. « Notre nouveau centre de lavage en Irlande reflète notre volonté de résoudre certains des problèmes les plus critiques auxquels la chaîne d’approvisionnement alimentaire est confrontée, tels que la pénurie de main-d’œuvre, la sécurité alimentaire et l’impact sur l’environnement. Avec cette nouvelle installation, nous sommes les pionniers d’un centre entièrement automatisé pour répondre aux besoins de nos partenaires de manière durable, en apportant plus d’automatisation à la chaîne d’approvisionnement», explique Adrian Dale, directeur général de Tosca au Royaume-Uni et en Irlande. Le site d’une surface de 8000 m² est équipé de panneaux solaires, d’un éclairage LED et de capteurs pour économiser l’énergie. Il accueille également un séchoir centrifuge, ainsi qu’un système de recyclage de l’eau tout au long du processus de lavage. Objectif : en sortie de ligne, les contenants nettoyés doivent contenir moins d’un gramme d’eau. «L’ouverture de ce centre de lavage avancé en Irlande nous place à la pointe de l’industrie et nous permet de fournir à nos partenaires le service de haut niveau dont ils ont besoin pour s’assurer que leur chaîne d’approvisionnement dispose de contenants propres et disponibles», a conclu Mike Wasson, directeur des opérations chez Tosca.
IPP modernise ses infrastructures dans le Nord de la France
Pour accompagner sa croissance en France, l’expert de la location de palettes bois IPP (Faber Group) s’est équipé, en début d’année, d’un nouveau centre de service entièrement automatisésur la commune de Labourse, à 23 km au Nord-Ouest de Lens (Hauts-de-France). D’une capacité de traitement de plus de 2,5 millions de palettes par an, le site industriel appartient à la société HDF Emballages, qui depuis 2016 est spécialisée dans le recyclage et la revalorisation de palettes bois. Cette année, cette dernière assurera la collecte, le tri et la réparation de 1,8 million de palettes bois brun-brique de la marque IPP pour la moitié Nord de la France. Avec une telle capacité de traitement, le centre de service de Labourse devient le troisième dépôt le plus important en termes de capacité de traitement d’IPP en France, après Paris et Lyon. L’ouverture de ce nouveau centre s’inscrit dans la continuité du plan de croissance du loueur dont l’objectif est d’atteindre les 100 millions de mouvements de palettes sur le vieux continent à horizon 2025. «Dans la cadre de notre plan Network 2025, la solution proposée par HDF correspond exactement à ce que nous souhaitons déployer sur l’ensemble de notre réseau en France. Les objectifs affichés étant une diminution du temps d’immobilisation des supports sur les dépôts, des processus de tri et de réparation optimisés et un confort de travail accru pour nos opérateurs», souligne Thibaut Esnée, directeur d’IPP France. Siège social historique d’HDF Emballages, le site de Labourse dispose d’une capacité de traitement pouvant aller à plus de 2,5 millions de palettes à l’année. Pour réussir ce challenge industriel, et soutenir une croissance de 20% par an, son dirigeant Grégory Leblan a investi 3 millions d’euros dans la construction d’un nouveau bâtiment de 2000 m2 qui abrite une ligne de production de 40 mètres de long. Celle-ci est entièrement automatisée. Aucun port de charge lourde n’est réalisé par les opérateurs qui trient et réparent les supports de manutention.
Grâce à un réseau de 61 centres de service et de dizaine de milliers de points de collecte en Europe Occidentale, IPP collecte, trie, répare et gère plus de 60 millions de palettes par an pour le compte des plus grandes marques françaises et internationales.
LPR annonce avoir réduit ses émissions carbone
Engagée dans le dispositif FRET21 du programme EVE depuis septembre 2021, LPR – La Palette Rouge (Division d’Euro Pool Group) – a, en moins de deux ans, dépassé son objectif initial de réduire ses émissions de transport de 5,5% entre 2021 et 2023. Des résultats qui passent par l’utilisation de moyens de transport plus écologiques, l’optimisation du taux de chargement, la réduction des distances parcourues et l’achat de transport responsable. Ce bilan se traduit par une réduction de plus de 1130 tonnes d’émissions de CO2. De plus, grâce au développement de son réseau de Centres de Services et à l’optimisation constante de ses itinéraires par son service logistique, LPR a réussi à réduire la distance parcourue de 4% à l’échelle nationale, ce qui équivaut à une économie de plus de 650 tonnes de CO2. Cette réduction représente 60% de la baisse totale des émissions carbone en 2022. La même année, 70% de ses flux ont été assurés par des transporteurs certifiés « Objectif CO2», soit une augmentation significative par rapport à 55% à la fin de l’année 2021. En parallèle, LPR- La Palette Rouge, a franchi une étape décisive en introduisant les premiers flux de camions utilisant du Biofuel, en partenariat avec l’un de ses transporteurs. Cette initiative a permis de faire rouler plus de 1300 camions alimentés par du B100, un carburant composé à 100% de colza cultivé localement. «Notre adhésion au dispositif FRET21 nous permet de valoriser notre politique de décarbonation des transports, et nous sommes ravis des résultats obtenus jusqu’à présent. Nous nous engageons à poursuivre ces efforts en 2023, dernière année de notre premier cycle d’engagement dans le programme. Nous nous sommes très satisfaits de la dynamique positive qu’a suscitée ce dispositif au sein de notre entreprise», explique Jean-Luc Guenard, directeur général de LPR.