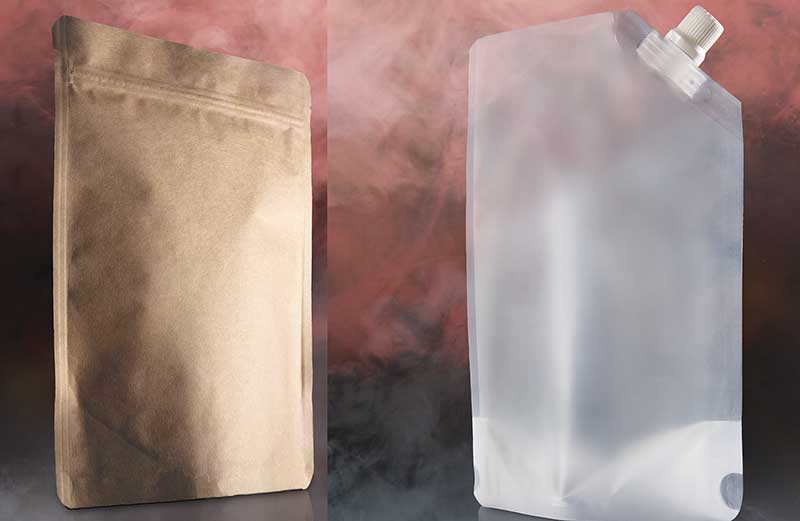
Sachets : le plastique reste très présent
posted Friday 02 June 2023
Abonnez-vous à la revue pour lire la suite de l'article
s'abonner
Si la demande pour des sachets en papier ne cesse de croître, la réalité industrielle reste en faveur du plastique, notamment pour ses performances. Les fournisseurs développent à la fois des solutions en papier (majoritairement avec une barrière à base de plastique) et en monomatière plastique.
Imprimeur et transformateur d’emballages souples et semi- rigides, Brodart Packaging fournit, entre autres, de multiples sacs en divers matériaux à destination de l’industrie agro-alimentaire. «Aujourd’hui, plus de 50% des demandes de nos clients portent sur des sachets en mono-matériau recyclables ou en papier. Des clients que nous fournissons déjà basculent de structures complexées aluminisées vers une association papier–PE, ou sur du 100% PP ou PE. Ils doivent, dans ce cas, réévaluer leur besoin en termes de barrière car rien ne peut remplacer un complexe aluminium à ce jour, mais on voit bien que dans de nombreux cas, la barrière aluminium historiquement utilisée est sur-effective par rapport au produit conditionné», constate Benoit Charpentier, directeur de l’usine Brodart Packaging – Breger centre.
La solution papier–PE reste un produit phare: «nous réduisons au minimum l’épaisseur de plastique permettant d’assurer la résistance mécanique du sachet, sans non plus augmenter la part de papier, ce qui n’aurait pas de sens. Si un film polymère est intégré dans le sachet papier, on peut y apposer un zip, une valve de dégazage, un bouchon…», précise Benoit Charpentier. Les sachets en papier pour du café, par exemple, assurent des DLC de 18 mois. L’un des inconvénients de ce matériau reste cependant sa fragilité. Il est également plus «marqué» dans le cas de pliures, et son impression, sur l’extérieur du packaging, n’est pas protégée. «Les équipes marketing sont favorables au papier, mais en termes de performance, de machinabilité et de recyclage, certains de nos clients déclarent vouloir revenir sur des solutions à base de plastique ! Le papier est, en effet, contraignant sur les machines, car c’est un support plus épais, qui se déchire», remarque Sébastien Brodart, directeur général du groupe.
Le papier demande des concessions
Pourtant, la demande pour des solutions à base de papier ne cesse de croître. Le groupe Mondi investit dans des technologies pour renforcer la capacité de production de ses papiers FunctionalBarrier. Un investissement dans une extrudeuse est prévu au sein de son usine en République Tchèque. Un nouveau bâtiment abritera aussi des machines dernière génération (ligne d’extrusion, machine à refendre pour bobines de papier…). Des investissements sont également en cours dans l’usine Mondi en Allemagne, avec deux nouvelles stations d’enduction par dispersion, et la construction d’une entité d’enduction qui devrait permettre de pré-enduire le papier et d’élargir l’offre pour inclure davantage de qualités de papier (notamment celles contenant une part de recyclé). En début d’année, Mondi a élargi la gamme FunctionalBarrier, qui peut être recyclée dans le flux du papier. Ces papiers disposent de différents niveaux de barrière, selon les besoins : enduction à base d’eau, revêtement par extrusion, etc.
En Allemagne, l’une des usines Coveris fabrique des sacs en papier préformés pour des applications sur les marchés du chocolat et de la confiserie. «Nous constatons une forte demande. Nos solutions visent à réduire la part de plastique assurant la barrière : pour cela nous travaillons sur les matériaux – les papiers évoluent, sont plus résistants – et la technologie de façonnage. La façon dont on construit ou contrecolle le papier amène à différentes combinaisons, et peut réduire le besoin de barrière supplémentaire apportée par les matières plastiques. Cela a aussi abouti, par exemple, à une solution innovante de système de fermeture par soudure thermique», explique Jérôme Detais, directeur commercial du site Coveris Firminy, qui fabrique des sachets préformés, des sachets de type doypack, et des films FFS livrés en bobines. Il note cependant une forte tendance à la décoration aspect papier… sur du plastique ! «Le retour au papier nécessite des concessions très importantes. Aujourd’hui, le papier ne peut pas faire aussi bien que le plastique sur certaines caractéristiques, et de nombreux clients ne sont pas prêts à accepter la différence, notamment pour la durée de vie d’un produit», remarque-t-il. Les fournisseurs doivent en effet s’assurer que les produits soient bien compatibles avec la chaîne logistique ensuite, car celle-ci ne peut être modifiée rapidement. «Il faut aller au bout du raisonnement et anticiper la résistance du matériau, son aspect, sa tenue en rayon et lors de son utilisation, etc. », renchérit Jérôme Detais.
Du papier sans film plastique
L’entreprise Guyenne Papier a, elle, décidé d’aller plus loin, en supprimant complètement le plastique. «Grâce à des enductions spécifiques, nous apportons au papier des propriétés barrière sans plastique. Tout en conservant ses performances techniques, le papier reste recyclable et l’enduction ne dégrade pas la capacité du papier à être recyclé. Ces produits sont complexes en termes de fabrication industrielle. Nous avons mis au point des produits 100% naturels, sans transformation chimique : la molécule existe à l’état naturel», détaille Céline Procop, pdg de Guyenne Papier.
Se définissant comme un «coucheur-enducteur», l’entreprise achète le papier et le traite en surface pour lui donner des propriétés. Sous la gamme Sunibarrier, trois nouveaux produits thermoscellables ont été lancés récemment, après quatre années de recherche et développement. Le papier Greenbee s’adresse aux aliments secs et gras : biodégradable (même dans l’eau de mer), il est adapté à des utilisations courtes. Sa technologie a été développée avec l’entreprise Lactips, spécialiste des polymères naturels. La solution Ladybee est, elle, adaptée aux produits secs, ou humides et non-gras (gâteaux, fruits secs), pour des DLC longues. «Ce papier offre une grande performance de thermoscellage, et permet de maintenir des cadences soutenues. La technologie s’appuie sur une enduction à base d’eau, qui ne dégage pas de nanoparticules», explique Céline Procop. Pour les produits secs, gras et humides, la solution Universalbee dispose aussi d’une barrière à l’eau. «Thermoscellable également, elle est toutefois moins performante que le papier Ladybee sur ce point, et sa productivité est moindre. Nous ne proposons pas de solution tout-en-un, d’où ces offres ayant chacune des spécificités de performances dans le but d’approcher un niveau de barrière élevé», ajoute-t-elle. Avec une DLC à trois mois, la durée de conservation permise par ces papiers n’est pas encore équivalente à celle des films plastique. «Il y a une incohérence entre la volonté d’emballages plus écologiques, et l’exigence de conservation. Quelle est vraiment l’utilité d’une DLC longue ? L’enjeu pour nous est d’améliorer la performance de nos produits sans utiliser des substances controversées – comme la résine fluorée, ni rajouter de l’EVOH, qui serait un plastique en plus dans la matière», souligne la pdg. L’entreprise effectue une veille importante sur les substances chimiques, expérimente de nombreuses formules de couche, et réalise beaucoup d’essais sur machines afin de trouver les meilleurs alliages couche – enduction – papier (dont le poids est de minimum 58 g/m2). La machinabilité de ces solutions n’est pas différente des films ou des papiers complexés. «Nous devons simplement faire un peu de pédagogie auprès de nos clients qui basculent du film au papier, car le papier est plus rigide, notamment lors du remplissage des sachets. Ils trouvent des ajustements», note-t-elle. En termes de coût, les papiers Sunibarrier sont minimum 15 à 20% plus cher qu’un film plastique.
Sachets en 100% PE ou PP : des contraintes spécifiques
En parallèle, les sachets en monomatière se développent. Chez Coveris, l’ensemble des développements tourne autour de la recyclabilité et de l’économie circulaire. «Nous axons les développements sur des produits à 100% à base de PE, surtout dans notre usine de Firminy, car la filière de recyclage de ce matériau est la plus avancée. Le PE se montre aussi plus rigide, plus résistant, plus facilement soudable que d’autres plastiques. Au sein du groupe, nous développons également des pack en PP et en polyester. Avec nos partenaires, nous travaillons sur l’allègement des matières. Nous atteignons une certaine limite, mais, dans certains cas, le fait de basculer en mono-matériau permet de réduire le nombre de couches de 3 à 2. Et des technologies d’orientation de film permettent aussi d’obtenir de bonnes propriétés avec des épaisseurs très fines», détaille Jérôme Detais. Un système d’ouverture/fermeture, tel un zip, peut être pré-soudé sur le film. «Nous conservons la même technologie de remplissage chez nos clients qu’auparavant mais sur une monomatière, ce qui est un challenge. De même, avec un mono-matériau, les prédécoupes laser pour faciliter l’ouverture du sachet doivent être modifiées, car le PE ne se comporte pas comme le PET. Nous avons développé des solutions avec nos partenaires machines pour trouver la bonne combinaison entre le réglage des paramètres de la machine et le matériau», ajoute-t-il. Jérôme Detais remarque une demande accrue pour des systèmes de fermeture de type scratch, et pour de l’impression en très haute qualité, «y compris concernant l’impression en flexographie, qui atteint désormais quasiment le niveau de l’héliogravure».
Le fournisseur Brodart Packaging dispose également d’une gamme de sachets en PE, renforcés par des barrières EVOH ou encore des enductions d’Alox, selon le niveau de barrière souhaité. Apporter une haute barrière au PE reste toutefois difficile. Les DLC sont équivalentes à celle d’un papier-PE. «Concevoir des sachets en PE n’est pas simple – ce matériau est sensible aux contraintes thermiques et moins facile à travailler sur machine que le PP, mais la filière de recyclage est en place. Nous avons passé beaucoup de temps à valider les process industriels sur des sacs de type stand up, des options de bouchon, de zip… Nous avons également accompagné nos clients pour régler les températures de scellage, les cadences», détaille Sébastien Brodart. Le groupe travaille aussi sur des sachets en 100% PP, misant sur le développement de la filière de recyclage. Thermorésistant, le PP ouvre de nouvelles perspectives d’applications, par exemple sur des sachets de grande contenance pour de la purée de fruits.