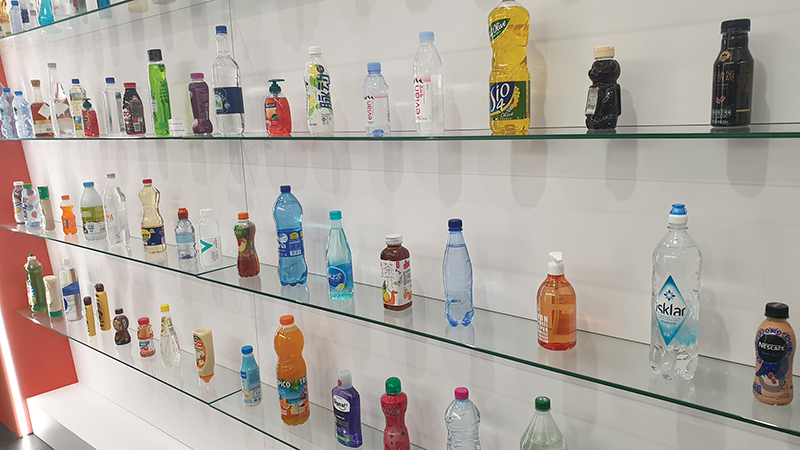
Sidel inaugure une ligne pilote de recyclage du PET
posted Sunday 30 October 2022
Abonnez-vous à la revue pour lire la suite de l'article
s'abonner
En marge du 60e anniversaire du site d’Octeville-sur-Mer en Normandie, Sidel a convié le 7 octobre dernier élus locaux, presse et partenaires à inaugurer son nouveau hub dédié au recyclage du PET. Une installation stratégique qui va permettre à l’expert du soufflage d’adapter ses machines aux résines plastiques recyclées, dont la demande est en forte progression notamment dans le secteur agroalimentaire, à l’instar de celui des boissons.
Selon la Fondation Ellen McArthur, la demande de r-PET augmente et le marché se développe à mesure que les propriétaires de marques recherchent des solutions neutres en carbone. La quantité de PET recyclé dans les emballages à l’échelle mondiale est passée de 5 à 8% entre 2018 et 2021, avec une projection estimée à 35% en 2030 en Europe. «C’est un matériau qui donne entière satisfaction aux consommateurs et qui permet une production flexible et optimisée puisqu’il permet de fabriquer et de remplir les contenants sur place, évitant ainsi le transport d’emballages vides», explique Vincent Le Guen, vice-président packaging, moules et solutions de lignes chez Sidel. Une pression qui oblige les constructeurs de machines à adapter plus finement leurs outils pour répondre aux nouveaux besoins de leurs clients. Illustration le 7 octobre dernier, avec l’inauguration officielle de la nouvelle ligne pilote de recyclage du PET par le groupe Sidel à Octeville-sur-Mer (Seine-Maritime), en présence notamment d’Edouard Philippe, maire du Havre. En connaisseur de la région et de son tissu industriel, ce dernier a d’ailleurs déclaré : «l’usage des matières plastiques était une question de bon sens en 1962 à la création de Sidel, aujourd’hui c’est une question d’urgence». Et Raphaël Clairin, président Sidel Blowing & Services, d’expliquer : «nos clients s’orientent progressivement vers du 100% rPET dans leurs emballages. Or, nous le savons, le PET recyclé mécaniquement est plus fragile et moins résistant. Nous devons anticiper les futurs challenges techniques que va engendrer cette transition, et plus particulièrement pour les produits sensibles comme les eaux gazeuses, les jus, le lait ou encore la bière qui représentent aujourd’hui 40% de nos commandes machines».
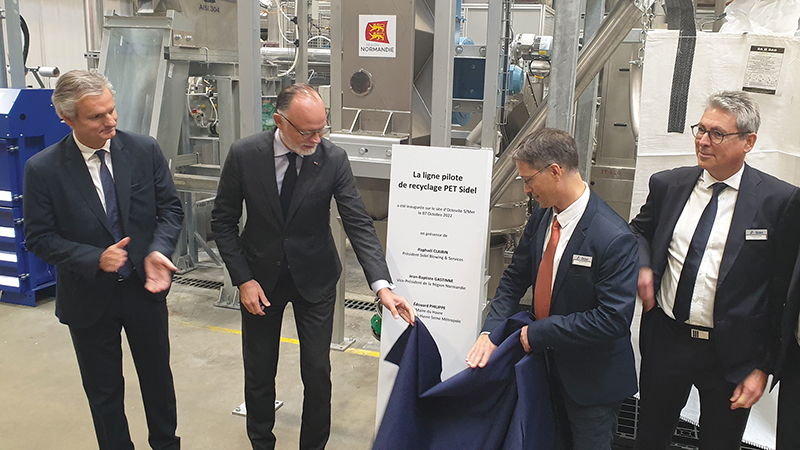
Un investissement de 2,5 millions d’euros
Réplique à l’échelle laboratoire d’une ligne industrielle de recyclage, ce nouveau hub couvre l’ensemble des étapes de recyclage, avec une capacité d’une centaine de kilos par jour. A partir des balles collectées localement par Veolia et les déchets récupérés sur site (bouteilles, barquettes, films PET,
etc.), un premier tri manuel est réalisé puis les matières séparées dans des bacs par flottaison pour récupérer le PET propre, qui est transformé en paillettes. Après une étape de séchage (machine Piovan) pour atteindre un taux d’humidité de 50 ppm, celles-ci sont passées dans une vis d’extrusion à 250°C pour produire des fils de PET qui sont refroidis et découpés en granulés amorphes. Vient ensuite une étape de cristallisation, de polymérisation à l’état solide pour retrouver la viscosité intrinsèque et de purification (machine Italvacuum). Réalisée sous-vide, à haute température, sous gaz neutre, elle permet l’obtention de granulés de PET recyclé de grade alimentaire. Ces granuléssont ensuite injectés dans le moulage (machine Arburg)soit en plaques pour contrôles en laboratoire (colorimétrie, points noirs) soit en préformes pour tests de soufflage sur un modèle Matrix SBO8 à quelques mètres de là. «La qualité du PET recyclé est primordiale pour comprendre son comportement, éviter les dysfonctionnements lors de l’étirage/soufflage comme des risques d’éclatement et ainsi, adapter au mieux le paramétrage de nos machines (temps de chauffe, pression, ventilation, etc.). Or, celle-ci n’est pas aujourd’hui homogène et nécessite des études plus fines pour mieux étudier et comprendre le PET recyclé. C’est tout l’objectif de cette nouvelle ligne pilote», détaille François-Xavier Gaillard, responsable de la division packaging & moules chez Sidel. Deux opérateurs ont été spécialement formés sur la nouvelle ligne pilote, la seule en France, selon le constructeur. L’idée sera dans un second temps d’offrir, en sous-traitance, l’accès à cette plateforme à l’ensemble de la filière de l’emballage qui pourra y mener ses propres tests sur les plastiques recyclés.
Un centre d’usinage intégré
Autre atelier du site d’Octeville-sur-Mer à avoir bénéficié d’un important investissement, le centre d’usinage du groupe Sidel. Depuis deux ans, 13 millions d’euros ont permis la modernisation des outils dont l’équipement de deux fraiseuses 4 et 5 axes Makino et Okuma et l’arrivée prochaine d’un îlot robotisé Armin Sherpa pour 2023. 65 personnes s’affairent au quotidien dans ce centre de production des moules, une pièce essentielle dans le process de fabrication des bouteilles et flacons, imaginées par les clients Sidel. «Il faut entre 3 et 15 heures d’usinage pour réaliser un moule en fonction de sa complexité. Nous consommons en moyenne 130 tonnes d’aluminium par an, et nous en sommes propriétaires ce qui nous libère de toute pression, quant à son prix et approvisionnement», explique François-Xavier Gaillard. Une fois passées dans des moules ébaucheurs, anodisées puis taillées – avec polissage à l’extérieur – les empreintes de corps et de fond sont gravées par laser et personnalisées avant assemblage. Un savoir-faire unique qui réclame une précision pointue et un contrôle qualité exigeant, le centre d’usinage étant certifié ISO 9001.
Plus globalement, le site d’Octeville-sur-Mer fait régulièrement l’objet d’investissements de la part du groupe pour réduire son empreinte carbone. 2,5 millions d’euros ont été débloqués pour remplacer l’ancienne chaudière à gaz par une chaudière biomasse. De même les compresseurs, de 20 ans d’âge, ont laissé place à de modèles nouvelle génération, plus performants. Refonte des bureaux, éclairage LED, isolation, bandes de recharge électrique, etc. sont autant d’initiatives prises par Sidel pour réduire sa consommation énergétique.
La formation au centre de la stratégie Sidel
Suite logique à l’ouverture du nouveau hub sur le PET recyclé, Sidel poursuit sa stratégie de formation sur le sujet auprès de ses partenaires et opérateurs en interne. «Depuis deux ans, le process rPET est la session la plus demandée sur les sites de nos clients et elle ne cesse de progresser», observe Sophie Wattiez, responsable du centre de formation certifié Qualiopi. Abrité par le plus ancien bâtiment de l’usine d’Octeville-sur-Mer, le centreaccueille six salles de formation et une équipe de huit formateurs. Réhabilité et modernisé en 2016, le local abrite également une souffleuse SuperCombi Matrix dernière génération afin de former directement opérateurs et apprentis en conditions réelles. «En 2021, 510 techniciens Sidel dont 138 opérateurs FSE sont passés par notre programme de formation à Octeville-sur-Mer», ajoute Sophie Wattiez. Des salles de formation à distance sont prévues en 2023 pour compléter l’offre du groupe.