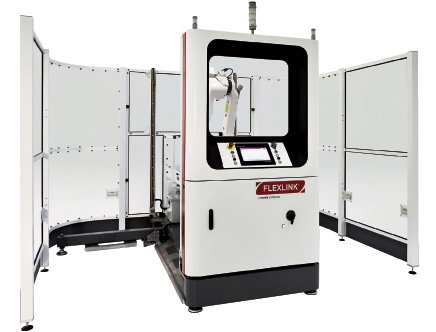
The new RI20 palletizer from FlexLink simplifies complex processes
posted Wednesday 10 June 2020
The RI20 palletizer developed by Flexlink is suitable for palletizing closed boxes within fast-moving consumer goods industries. The unit includes enhanced safety features that allow a safe coexistence between the robot and operators on the production floor.
The presence of operators in the safety area dynamically adjusts the speed of the robot instead of stopping it, reducing unnecessary downtime. Also, two pallet loading docks create a seamless pallet exchange that allows them to be filled in succession and increase capacity by up to 5%.
The compact design of the unit saves up to 40% floor space compared to heavy robot palletizers. The mainframe does not have to be attached to the floor and the RI20 can easily be moved using a forklift. The palletizing unit can be relocated in just a few hours, 50% quicker than alternative solutions, and can be used in multiple lines during the day.
The RI20 has an intuitive, web-based pallet pattern manager and does not require robot programming. It takes less than 10 minutes to set up a new recipe, or just a few clicks to load an existing design.
The RI20 is available with several options: a rigid interlayer module, the Robot Config software (pallet pattern manager), a portable tablet, the remote assistance package, a preventive info package, and a data collection package.
Headquartered in Gothenburg, Sweden and part of Coesia group, FlexLink has operating units in 31 countries and is represented in more than 60. In 2017, the company had 1116 employees and a turnover of $ 300 million.
All rights reserved except agreement written by Emballage Digest or mention of the magazine