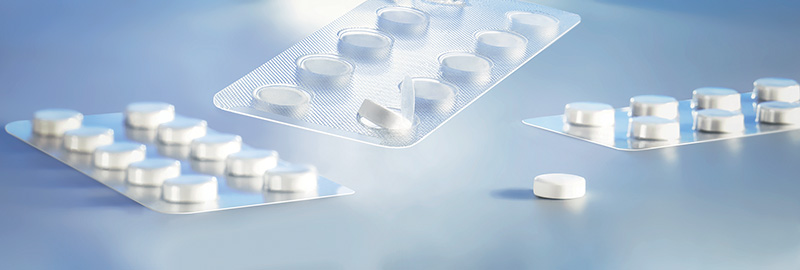
Vers des blisters plus responsables et fonctionnels
posted Tuesday 28 February 2023
Abonnez-vous à la revue pour lire la suite de l'article
s'abonner
Le blister est l’emballage primaire de médicament le plus utilisé. Avec de nombreux avantages liés à la délivrance d’une dose individuelle (observance), l’inviolabilité et un coût économique intéressant. Le plus gros problème reste son recyclage, étant constitué d’une coque en plastique, dans 90% des cas en PVC, avec une couche en aluminium. Face aux exigences de durabilité, les fabricants explorent plusieurs axes (biomatériaux, blisters mono-matériaux) pour développer des blisters plus responsables et fonctionnels – avec le défi de rester abordables.
Plusieurs initiatives voient le jour autour des biomatériaux : des matières innovantes biosourcées, issues de la biomasse végétale ou animale, c’est-à-dire à l’origine entièrement biologique. C’est par exemple le cas d’Astellas Pharma, qui a mis sur le marché il y a deux ans un blister composé à 50% de bioplastique, à savoir du polyéthylène dérivé de la canne à sucre, pour son médicament «Irribow® Tablet 5μg» (chlorhydrate de ramosétron, indiqué dans les cas de diarrhée – syndrome du côlon irritable). Il s’agit «d’un emballage vertueux pour l’environnement, à partir de ressources végétales entièrement renouvelables, et basé sur le concept de la neutralité carbone qui vise à équilibrer les émissions et l’absorption des gaz à effet de serre», souligne Astellas, qui a commencé ainsi à diminuer le PVC dans ses blisters, tout en réduisant son empreinte industrielle.
Améliorer le recyclage
Au-delà de réduire les déchets plastiques, les fabricants de films travaillent à améliorer la recyclabilité du blister, un sujet de préoccupation de longue date. L’allemand Liveo Research a récemment ajouté une solution complète de blister A-PET à son portefeuille. «Celle-ci se compose d’un film blister A-PET sans halogène (BlisForm MA) et d’un opercule en PET (BlisLid MA) pelable développé avec adapa Danemark (ex-Danapak Flexibles)», décrit Isabelle Unseld, sa directrice marketing. La solution A-PET, hautement transparente, est transformable sur des lignes de blisters PVC standards et recyclable dans les flux RIC1 existants. «Ces blisters mono-matériaux sont une bonne option pour le recyclage mécanique et chimique, car ils évitent les étapes de séparation des matériaux et les risques de contamination liés aux blisters conventionnels», explique-t-elle. L’entreprise s’est pour l’instant concentrée sur des blisters mono-matériaux à faibles barrières, mais les travaux en cours s’orientent vers des solutions à moyennes et hautes barrières.
Premier pas vers la circularité
Une autre innovation dans le secteur est le blister transparent, à barrière intermédiaire, de Tekniplex Healthcare, certifié recyclable dans les flux de polypropylène européens – «un premier pas vers la circularité des matériaux en santé», selon Melissa Green, sa responsable marketing mondiale. L’emballage recyclable associe un film blister en polyoléfine à un film d’operculage en PP barrière. L’une de ses principales caractéristiques est sa transparence pour que «le patient voit à travers». C’est aussi un avantage, selon elle, pour faciliter l’inspection visuelle manuelle et automatisée du médicament sur les lignes de fabrication. Le blister a été lancé, dans un premier temps, avec une option d’opercule pelable. D’autres options seront disponibles en 2024. A noter : Tekniplex met également à disposition une combinaison blister et opercule mono-matériaux en polyester, entièrement recyclable, pour les comprimés et gélules qui ne nécessitent pas de protection barrière. Les deux types de blisters recyclables ont été testés avec succès dans plusieurs essais à petite et grande échelle sur différents équipements de fabrication. «Des évaluations sont en cours également avec les clients», ajoute-t-elle. En outre, Tekniplex met à disposition un nouveau papier couché renforcé à faible grammage pour la protection des dispositifs médicaux tels que les seringues, les tubes intraveineux, les cathéters… Ces innovations s’inscrivent dans sa stratégie de «repenser de manière responsable» les emballages.
Blister cellulose
D’autres fabricants vont plus loin dans leur engagement d’éliminer les plastiques à usage unique et, au-delà, le PVC des blisters. C’est pour y arriver que le cabinet de conseil PA Consulting et PulPac ont créé le collectif Blister Pack Collective. Un premier cap est de commercialiser leur blister en fibre moulée à sec, issu de la technologie DMF du fabricant suédois, qui a été lancé et présenté sur Pharmapack Europe 2023. L’idée ambitieuse est d’utiliser des ressources renouvelables de pâtes et de celluloses pour produire des emballages à base de fibres, à faible coût et à haute performance, et qui seraient traités de manière circulaire dans les flux de papier. «Le processus de fabrication exclusif utilise moins de CO2 et très peu d’eau pour créer des matrices de comprimés très polyvalentes, correspondant à la conception et au nombre de comprimés du blister PVC de base, offrant une solution évolutive pour les laboratoires», explique Tony Perrotta, expert durabilité et économie régénérative chez PA Consulting. En 2022, un premier prototype a été réalisé pour démontrer la faisabilité. Cette année, la collaboration avec l’industrie sera clé pour faire la démonstration de la solution sur ses équipements et intégrer les fonctions barrières. 2024 devrait être l’année du développement réglementaire et de la mise à l’échelle de la production. «Ce partenariat avec PulPac et le collectif avec les industriels devrait se traduire par un apprentissage et une croissance accélérée», espère-t-il.