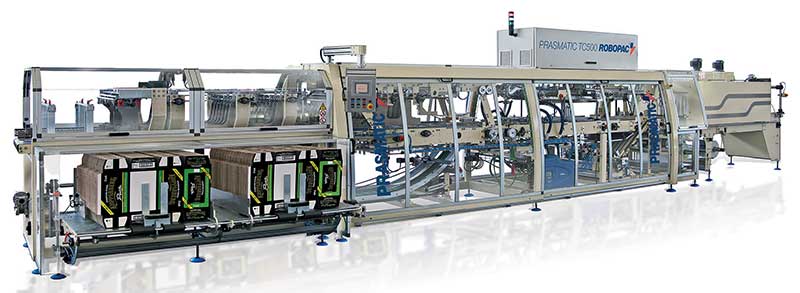
Fardelage : les besoins évoluent, les matériels s’adaptent
publié le vendredi 02 juin 2023
Abonnez-vous à la revue pour lire la suite de l'article
s'abonner
La polyvalence des équipements, la facilité des changements de formats et l’efficacité énergétique figurent parmi les principaux critères de choix.
Les industriels de l’agroalimentaire portent une attention croissante à leurs dépenses et à leurs coûts de possession. C’est la raison pour laquelle, dans le fardelage, un certain nombre d’entre eux s’orientent vers des matériels capables de gérer plusieurs types de conditionnement et matériaux. Tel est le cas des machines Combi commercialisées par Robopac France (groupe Aetna) : «ces équipements de marque Prasmaticpeuvent très facilement passer d’une configuration film plastique rétractable seul à une configuration film/carton (plateau plat, barquette), ou encore carton seul (barquette haute, caisse). Ils offrent donc cinq possibilités pour un seul investissement, ce qui rassure les clients un peu inquiets quant à l’avenir du plastique», observe Vincent Hamel, directeur opérationnel de Robopac France.
Jusqu’à 150 cycles/minute
Caractérisées par des cadences allant de 35 emballages/minute (modèle TC 300) à 65 emballages/minute (TC 600), en passant par 45 emballages/minute (TC 400) et 55 emballages/minute (TC 500), les machines Combi bénéficient en outre d’un nouveau châssis procurant une meilleure accessibilité aux organes internes. Pour des vitesses plus élevées, cette même marque Prasmatic propose également l’enveloppeuse sous film rétractable TC 800, donnée pour 85 emballages/minute. Non disponible en version Combi, cette machine est toutefois déclinée en quatre configurations spécifiques référencées : C pour les emballages avec film seul, CF pour les emballages avec plateau plat et film, CW pour les emballages avec barquette et film, et enfin T pour les emballages avec barquette.
Encore plus rapide, puisqu’elle peut atteindre 150 cycles/minute, l’emballeuse sous film rétractable
Vega HT, vendue sous la marque Ocme, existe elle aussi en plusieurs versions (film et/ou barquette, film avec plateau, table en U…). Parmi ses points forts, citons la présence de rideaux motorisés à l’entrée et à la sortie du tunnel de rétraction de façon à réduire les pertes calorifiques et donc la consommation d’énergie à vide. «Au sein du groupe Aetna, c’est sans doute Ocme qui conçoit les fours les plus performants. Mais nous nous efforçons actuellement d’insuffler le meilleur de chaque fabricant dans l’ensemble des marques», indique Vincent Hamel. C’est ce qui a été fait, par exemple, pour la nouvelle fardeleuse Nova de Dimac, qui dispose elle aussi d’un four dernier cri avec optimisation des flux d’air chaud, isolation thermique renforcée et portes automatiques.
Le film étirable se fait une place
Pour réduire la consommation d’énergie des équipements de fardelage, liée en grande partie à celle des fours de rétraction du film plastique, il est toujours possible d’essayer de diminuer l’épaisseur des films, ou encore de remplacer ce four par de simples buses de soufflage à air chaud lorsque la taille des paquets le permet. Mais il y a également l’option plus radicale qui consiste à passer du film rétractable thermiquement et de passer au film étirable, lequel est lui aussi rétractable mais de façon purement mécanique, sans aucune chauffe. Une solution que propose avec succès B&B Verpackungstechnik. «Il y a cinq ans, les machines stretchde la gamme SBP (jusqu’à 40 fardeaux/minute) représentaient déjà la moitié de nos ventes de fardeleuses ; désormais, nous en sommes aux trois-quarts !», confie Alain Le Coq, responsable commercial de l’activité conditionnement de PBH France, représentant de B&B dans l‘Hexagone. Et d’expliquer que malgré un coût d’investissement un peu plus élevé que celui des machines standard du fait de l’ajout d’un dispositif de gestion de l’étirement du film, ces matériels sont rentabilisés d’autant plus rapidement que le prix de l’énergie ne cesse d’augmenter et que l’espace libéré par le tunnel peut servir à un équipement plus productif. Sans parler des économies de consommables… «Ce qui limite encore l’adoption du film étirable dans le fardelage, c’est en réalité la méconnaissance d’une partie des utilisateurs», estime Alain Le Coq.
Banderolage « vert »
Avec la volonté d’économiser l’énergie, la possibilité de mettre en œuvre un matériau plus «vert» que le plastique figure en tête des préoccupations de la clientèle de PBH. Lorsqu’il est question de suremballer des produits secs et pas trop lourds comme des boîtes de pâtes ou de céréales, le responsable commercial oriente alors vers la gamme B&B Matador PP (pour Packaging in Paper, en l’occurrence du papier kraft associé à une fermeture par colle chaude). De conception ancienne mais régulièrement remises au goût du jour, ces machines affichent une cadence tout à fait honorable de 15 cycles/minute.
Autre signe du regain d’intérêt pour le papier : l’entrée au catalogue Bulteau Systems de la banderoleuse de table Proband V2000. «Destinée à la confection de petits colis, cette machine effectue une mise sous bandes de maintien soit en plastique, soit en papier imprégné d’une cire PE que l’on fait fondre par ultrasons avant soudage», détaille Romain Girard, directeur technique de Bulteau Systems.
Ce dernier tient d’ailleurs à préciser qu’il est dès à présent en mesure de remplacer cette cire PE par du latex naturel pour les clients qui excluraient l’emploi de toute matière synthétique, même en petite quantité. Capable de réaliser jusqu’à 30 liens/minute, la Proband V2000 intéresserait, entre autres, les cuisines centrales faisant appel à des boîtes lavables en inox. «L’avantage de cette machine par rapport à la concurrence, c’est sa modularité, poursuit Romain Girard. Au module de base, exploitable en mode semi-automatique ou bien intégrable en ligne moyennant quelques options, on ajoute le système de soudure et les arches adaptées à la taille des colis, sachant que ces arches interchangeables conviendront elles-mêmes à différentes largeurs de bande. Pour le poids maximal du colis, cela dépend de cette largeur mais aussi de la résistance de la bande et du nombre de liens : tout cela est à étudier au cas par cas».
Le « sur-mesure » ne désarme pas
Pour en en revenir au fardelage pur et dur, Lionel Questroy, directeur des opérations de Novipack (groupe Bulteau Développement), note pour sa part une certaine tendance au ralentissement des cadences, la productivité n’étant selon lui pas – ou plus – le critère de choix numéro un des industriels auxquels il a affaire. En revanche, les clients se montreraient toujours très exigeants sur l’adaptation des machines, au point de rentrer parfois dans le cadre du «sur-mesure». Des demandes auxquelles le distributeur répond en puisant dans le savoir-faire de partenaires tels que Vimacor, LP Packaging ou Minipack-Torre. En termes de ventes, c’est LP Packaging qui détient la palme avec la fardeleuse automatique SFE 800 : une machine monobloc (tapis d’alimentation en ligne et tunnel de rétraction intégrés au châssis). Du côté des nouveautés, «plutôt rares dans ce domaine», concède Lionel Questroy, mentionnons chez Minipack-Torre l’introduction de la Wrapjet 30 Integral, une machine automatique six pistes sans barre de soudure à une seule bobine qui réalise des fardeaux soit avec du film thermo-rétractable seul, soit avec du film et un carton intercalaire, soit encore avec du film et un plateau, et cela à une cadence pouvant atteindre 30 fardeaux/minute.