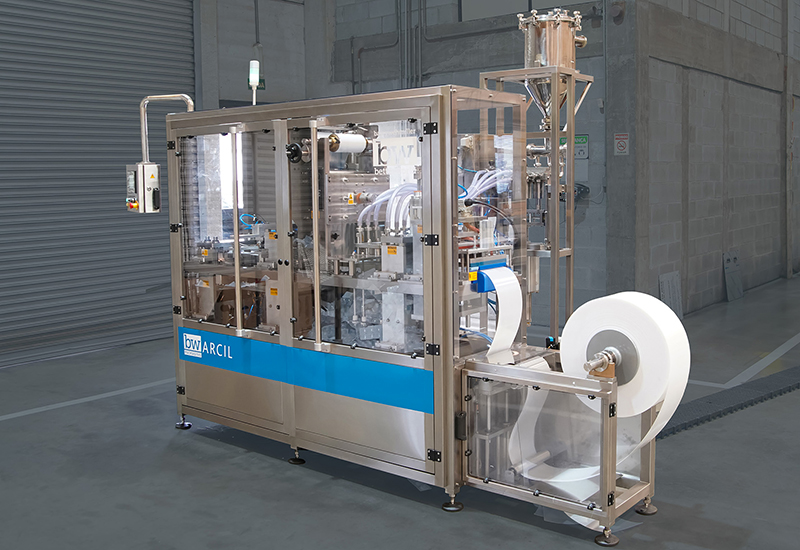
FFS vs FS : les outils de coupe change la donne
publié le dimanche 31 mars 2024
Abonnez-vous à la revue pour lire la suite de l'article
s'abonner
Est-il plus intéressant de former (avec une machine FFS), ou pas (avec une FS), son pot avant de le remplir et de le sceller : la réponse à cette question récurrente dépend bien entendu du type de pot souhaité, mais aussi des particularités de l’équipement de production.
Polyvalence en ce qui concerne les matériaux et les formats, coûts de la machine et des emballages, productivité… : la liste est longue des critères qu’un industriel des produits laitiers est amené à prendre en compte à l’heure du choix entre une machine FFS (Form-Fill-Seal) et une FS, c’est-à-dire une «simple» remplisseuse-scelleuse de pots préformés. Et pour couronner le tout, il y a cette incertitude qui plane sur les intéressés quant à l’avenir des plastiques en général, et de certains d’entre eux en particulier comme le PS. «L’aptitude des machines à traiter tel ou tel matériau que l’utilisateur sera peut-être amené à privilégier au détriment de tel autre, en fonction de sa recyclabilité ou de son empreinte carbone, devient déterminante dans la prise de décision», constate Johan Degardin, responsable commercial France d’IMA Food (marques Erca et Hassia pour les FFS, Erca, Gasti et Hamba pour les FS).
Plastique au choix pour les multipacks
Du point de vue de la dynamique commerciale, il semblerait que cette exigence de flexibilité donne actuellement l’avantage aux FS, qui s’accommodent en effet de tous les types de contenants (du verre au plastique en passant par le carton ou l’aluminium). Ceci dit, les FFS détiennent de sérieux atouts… D’abord leur capacité «native» à réaliser des conditionnements multipacks sans suremballage carton, contrairement aux FS. Ensuite – depuis peu mais chez plusieurs fournisseurs (au moins IMA et Synerlink, voir plus loin) –, celle de rendre ces multipacks séparables en pots individuels sans nécessairement faire appel à du PS.
«Parce qu’il est bon marché, facile à thermoformer et surtout à prédécouper, c’est ce plastique qui a jusqu’à présent été la norme pour les applications d’emballage FFS multipack sécable, plutôt que le PET ou le PP, rappelle le responsable commercial. Mais grâce à des outils de prédécoupe spécifiques et brevetés mis au point par notre filiale Intecma, une FFS haute cadence comme l’EF400est désormais tout à fait capable de mettre en œuvre aussi bien le PET ou le PP que le PS». Une innovation qui accroît donc sensiblement le degré de polyvalence du procédé FFS, même si le passage d’un plastique à l’autre n’est pas possible en mode «changement de format» sur la même machine.
Réversibilité des machines
« Qu’il s’agisse du PET ou du PP, le principe reste le même, explique Jérôme Flandrin, responsable marketing et formation clients chez Erca : au lieu de faire appel à une matrice en dessous et à un couteau au-dessus, comme pour le PS, ces nouveaux outils mobilisent deux couteaux de part et d’autre du film, ainsi que des dévêtisseurs qui en facilitent la pénétration en réduisant l’épaisseur du plastique. Pour autant, les rétreints du PP et du PET sont différents, de même que le nombre de pas de chauffe pour le formage (12 pour le PP au lieu de 8 pour le PET), ce qui conduit à deux matériels distincts».
En revanche, moyennant le changement d’une partie de l’outil de découpe, il sera tout à fait envisageable pour l’acquéreur d’une EF400 conçue pour le PET de repasser au PS si nécessaire, et vice-versa… On notera également qu’Erca a profité de cet upgrade pour améliorer le processus de formage de la machine (plus puissant au niveau des poinçons d’étirage) afin d’assurer une répartition optimale du plastique dans les moules et ainsi minimiser l’épaisseur et le coût matière du pot (jusqu’à 15 ou 20% en reprenant aussi le design).
Optimisation qui ne fait en réalité que renforcer l’avantage économique unanimement reconnu des FFS par rapport aux FS, du moins à partir d’un certain volume de production : «un pot thermoformé coûte entre deux et cinq fois moins cher qu’un pot fabriqué à l’avance et on estime généralement que cet écart, à mettre en balance avec un coût matériel légèrement supérieur à performances comparables, rend cette solution compétitive au-delà de 12 000 ou 15 000 pots/h», estime Fabien Jégo, chef de produits chez Synerlink (marques Arcil pour les FFS et Dairy Pack pour les FS).
Une usine dans l’usine
Mais tout dépend bien sûr de ce coût matériel et, depuis quelques temps déjà, Arcil s’efforce précisément de déplacer les lignes en développant une offre FFS «accessible» dans laquelle on trouve notamment la DN200(de type pneumatique, six pots), caractérisée par une cadence de 5400 pots/heure pour un tarif autour de 250 000 euros (contre 1 à 1,5 million d’euros pour un modèle
20 000 pots/h classique).
Outre les questions de flexibilité et de prix de revient par pot pour un volume donné, c’est également sur le terrain de l’organisation que se joue le match FS vs FFS, juge le chef de produits. Car selon lui, «une FFS, c’est un peu comme une usine dans l’usine !». Avec des contraintes, comme la nécessité d’une « plus grande compétence technique (chauffe du plastique, particularités de la maintenance, etc.) de la part des opérateurs et des techniciens», mais aussi des aspects largement positifs, comme une autonomie machine de plusieurs heures, alors qu’elle se compte en minutes pour une FS. «Celle-ci résulte de l’emploi de consommables sous forme de bobines dont l’acheminement exige cinq fois moins de camions que leur équivalent en pots préformés vides, au grand bénéfice de l’empreinte carbone du produit fini», ajoute Fabien Jégo.
Le soufflage en embuscade
Reste qu’au-delà des logiques économique ou environnementale, l’aspect des contenants – ou en tout cas la perception qu’en auront les consommateurs – s’avère bien souvent crucial dans le processus de sélection d’une machine par un industriel. «Les FFS sont relativement standardisées et limitées dans les formes, ce qui les pénalise sur le segment des produits laitiers premium», confirme Fabienne Cheriaux, responsable marketing/applications alimentaires de Serac.
S’il se tient à l’écart du thermoformage – en dehors du fait d’équiper des FFS existantes en stations de dosage –, ce spécialiste des remplisseuses-scelleuses (gammes Néo en rotatif jusqu’à 6 000 pots/h, Linéa XSen linéaire jusqu’à 12 000 pots/heure puis Linéa LMS jusqu’à 55 000 pots/h) propose depuis quelques mois une solution monobloc alternative baptisée Cupboxqui vise elle aussi des coûts et une empreinte carbone des contenants moindres qu’en mode FS.
«Cette machine permet de souffler des préformes en PET dans un moule avec une plus grande latitude de conception qu’en FFS, puis de remplir les pots ainsi fabriqués – recyclables évidemment – et de les thermosceller avec des opercules en plastique ou en aluminium», résume Fabienne Cheriaux. Contrairement aux pots PET thermoformés à partir d’un film, le rendu obtenu (transparence, brillance) est proche de celui du verre, la légèreté et la résistance aux chocs en prime. Là encore se pose la question de la rentabilité : «elle est acquise à partir de 15 millions d’emballages produits annuellement, indique la responsable marketing, sachant que la cadence peut atteindre 18 000 pots/heure».