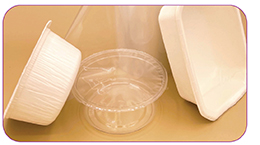
Films d’operculage : préparer leur recyclabilité
publié le jeudi 31 mars 2022
Les fabricants de films d’operculage font face à divers challenges pour répondre aux demandes des clients, qui s’orientent vers des opercules adaptés à la recyclabilité ou réintégrant de la matière recyclée.
Actuellement, le principe dominant dans le secteur est de concevoir des films d’operculage adaptés à la recyclabilité. «En ligne avec les guides Ceflex (un consortium d’entreprises, d’associations et d’organisations qui collaborent pour améliorer les performances des emballages souples dans l’économie circulaire en Europe, NDLR), les mono-matériaux sont préférés aux complexes de polymères afin de s’assurer de leur recyclabilité dans les filières existantes», souligne John Shipley, directeur des divisions Australie et Europe de KM Packaging. La société a lancé une nouvelle gamme d’opercules en PP. Chez le fabricant de supports souples fonctionnalisés Rexor, Laurence Touillon, responsable commerciale de la division alimentaire, constate «des demandes récurrentes pour des mono-films enduits ou des complexes mono-matériaux – 100% PP ou 100% PET – potentiellement recyclables dans la filière substrats souples en cours de développement».
Sur des applications d’operculage, les polyoléfines (PE/PP) montrent cependant des limites en termes de résistance thermique. «Ils sont seulement adaptés au réchauffage par micro-ondes. En outre, le contact direct avec les outils de thermoscellage peut causer un problème, car il y a un risque que le film colle à la tête de scellage. Dans un film d’operculage, on retrouve habituellement du PET ou du nylon dans le film extérieur afin d’apporter de la résistance à la chaleur, ainsi qu’une barrière plus élevée. Les polyoléfines, eux, ont une barrière à l’oxygène assez basse», relève John Shipley. Sans compter, que désormais, l’industrie évolue de plus en plus vers des barquettes en monoPP ou monoPET : «nos matériaux doivent donc souder sur du PP ou du PET, ce qui est plus compliqué que sur du PE. Nous faisons évoluer nos couches soudantes en ce sens : nous travaillons pour trouver plusieurs types de matières pouvant correspondre à des contraintes différentes. Par exemple, si le produit conditionné n’est pas souillant, la structure de l’opercule sera standard. Mais si on conditionne de la protéine animale avec un risque d’exsudat sur la zone de soudure, on travaillera la matière pour améliorer la qualité de soudure, avec des nuances d’un matériau à l’autre», détaille Philippe Guérin, directeur de la vente au détail et du e-commerce France pour Sealed Air. Le soudant PE, utilisé comme agent de liaison entre l’opercule et la barquette rigide, reste très présent sur le marché.
Extrait de la revue n° 666 – Mars 2022. Reproduction interdite sauf accord écrit d’Emballage Digest ou mention du support