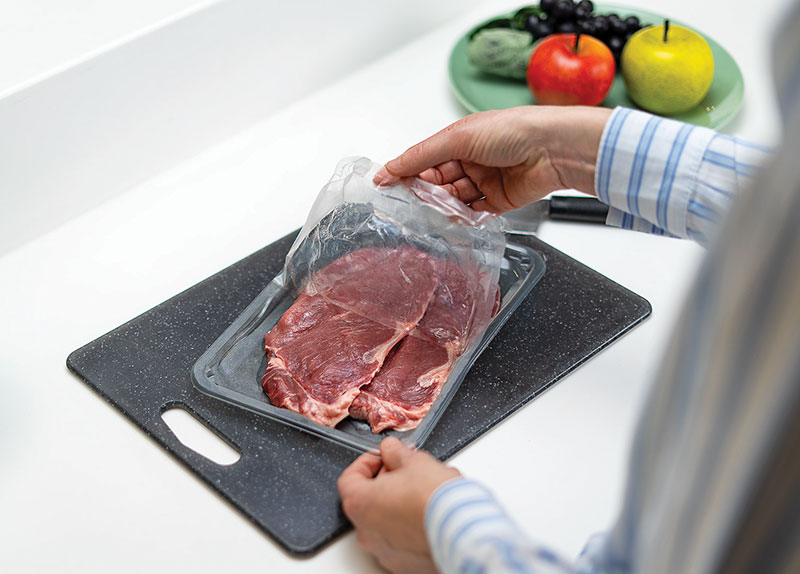
Films plastique : entre avancées et incertitudes
publié le dimanche 30 juin 2024
Abonnez-vous à la revue pour lire la suite de l'article
s'abonner
Les fabricants de films se focalisent sur des solutions monomatières, réduisant encore la part de matière et intégrant parfois du plastique recyclé. Les critères de recyclage n’étant pas encore définis concernant le règlement européen PPWR, certains développements sont en stand-by mais les investissements se poursuivent pour adapter les machines.
Si le règlement PPWR établit un cadre, ses critères ne sont pas encore définis, laissant les industriels dans le flou sur certains aspects. Il est néanmoins acté qu’à l’horizon 2030, tous les films devront être recyclables, et d’ici 2035 être recyclés en masse. «C’est ambitieux. Nous espérons que les critères de recyclage seront fixés d’ici 2028. Actuellement, si on se réfère au texte tel qu’il existe, les nouvelles sont très mauvaises pour les films plastiques ! Notre industrie a eu la naïveté de penser que les législateurs allaient prendre en compte les spécificités des différents films, notamment pour la protection des aliments. Les films fins destinés aux emballages alimentaires – dont ceux protégeant les protéines fraiches– sont complexes. Ces derniers ne pèsent que 2% de la totalité du tonnage des plastiques mis en marché en Europe, mais emballent 46% des dépenses alimentaires. Les enjeux sont importants : ils concernent la protection, le gaspillage ou encore la sécurité alimentaire», explique Arnaud Brunet, directeur Marketing & Produits EMEA de la division alimentaire de Sealed Air. Le groupe produit différents types de films destinés à des applications variées – operculage, suremballage, film skin, flowpack…
Les organisations professionnelles et les fabricants de films estiment qu’il est nécessaire de remettre de la réalité dans la définition des critères du PPWR. «L’organisme européen RecyClass, très actif concernant la définition des critères, se révèle contre quelques résines (comme certains types de polyamide) ou prône des limitations en quantité de résine, en pourcentage (pour l’EVOH, entre autres). En France, le COTREP estime par exemple que les films ne devraient pas contenir de polyamide. Mais aujourd’hui rien de ce qui est proposé ou envisagé ne garantit à nos industriels des solutions à la fois performantes, techniques et automatisées. Nous avons mis en place des groupes d’actions collaboratives pour démontrer auprès de certains organismes que la barrière EVOH ou le polyamide sont acceptables à des niveaux permettant un emballage performant. L’objectif est aussi de défendre nos critères au CEN (Comité européen de normalisation) sur la base de données réelles», indique Arnaud Brunet, qui pointe des incohérences du PPWR. «Un opercule monomatière de 50-60 microns pourrait être accepté, mais un autre non recyclable de 25 microns ne le serait pas…», relève-t-il.
La nécessité de prendre en compte le cycle de vie complet d’un produit
« De notre point de vue, le réglement PPWR est plus ou moins la transposition inversée de la loi AGEC en droit européen, avec quelques adaptations. Cette règlementation européenne donne une ligne directrice et fixe des règles pour les quinze prochaines années. Son texte n’est cependant pas toujours logique : il est parfois moderne, mais présente hélas une vraie iniquité de traitement entre les matériaux… En bref la philosophie de tout cela, c’est le recyclage des emballages en s’orientant sur du PP ou du PE pour les flexibles. En outre, un taux d’incorporation de matière recyclée est obligatoire : à partir de 2030, les emballages devront contenir 35% de recyclé, et 65% en 2040. Tout cela fait sens. Utiliser des matières recyclées permet de diviser par deux l’empreinte carbone du pack. Le règlement favorise l’émergence d’un marché, en obligeant toute l’industrie à embrasser la cause des mono-matériaux et des filières de recyclage. Pour moi, c’est un cercle vertueux. Elle va permettre de changer de regard sur les matériaux en plastique car ils seront valorisés et redeviendront une matière première », analyse Thierry Bonnefoy, pdg de Leygatech, fabricant de films barrière et de thermoformage. 70% de la production de la société est monomatière. La loi PPWR touche un large spectre de solutions de conditionnement. L’emballage plastique de regroupement fait partie de celles-ci «mais ce sont toutes les solutions de regroupement de produits qui doivent être étudiées et challengées. Le règlement vise l’éradication de l’emballage de regroupement promotionnel (impliquant la notion de produits en lots promotionnels). Pour l’instant, nous ne constatons pas d’impact sur l’approche de nos clients ou de report vers d’autres solutions», note Fabrice Lemaitre, directeur des ventes du groupe Barbier, qui produit, entre autres, des films de regroupement en PE. «Il est vraiment essentiel d’analyser le cycle de vie complet d’un produit afin de déterminer la solution la plus adaptée ainsi que d’intégrer à la réflexion l’impact sur les cadences des machines de conditionnement et les conséquences sur l’emballage logistique du produit», ajoute Vincent Vial, secrétaire général de Barbier.
Des marges de progression qui permettent d’avancer, malgré des inconnues
Ces incertitudes concernant les critères du PPWR ont un impact sur le développement des films. «Aujourd’hui, les investissements portent sur la R&D, mais pas forcément sur l’exécution des solutions, puisque le cadre n’est pas fixé… Sealed Air a investi des centaines de milliers d’euros pour démontrer la compatibilité de certaines résines avec le recyclage mécanique. Pour les films skin, compliqués à rendre recyclables, nous avons un plan de développement. Nous sommes désormais en mesure de proposer des solutions, mais cela passe par le développement d’un système spécifique, car il faut à la fois repenser le film et la machine. Nous avons élaboré différents scénarios et activerons le plus adapté quand les critères seront mieux définis», détaille Arnaud Brunet. La loi européenne implique une notion de réduction de matière. «Nous ne sommes pas encore arrivés au bout des logiques d’écoconception. On est souvent allé chercher des polymères complexes pour des solutions très optimisées. Désormais le cahier des charges change. Cela restera à la marge mais des emballages en monomatière ne seront pas toujours équivalents au pack initial – ils seront peut-être plus mous, moins brillants. Il faut aussi admettre que certains produits allaient parfois un peu loin dans le marketing, le groupage, le sur-groupage…», note Thierry Bonnefoy. Quant au groupe Barbier, ses principaux axes de travail sur les films portent sur la réduction des épaisseurs et l’augmentation du taux de plastique recyclé incorporé dans ses produits. «Nous sommes en mesure d’intégrer du plastique recyclé dans des films d’épaisseur de plus en plus faibles tout en conférant au produit les mêmes caractéristiques mécaniques», précise Fabrice Lemaitre. Le groupe Barbier possède deux sites de recyclage intégrés. «Nous achetons des gisements de déchets plastiques post-consommation que nous recyclons dans nos propres unités dédiées. Nous sommes, certifiés «Intégration de Matières Plastiques Recyclées (MPR)» par l’organisme LNE garantissant le taux d’incorporation ainsi que la traçabilité complète. L’intégration du recyclage dans nos activités nous donne l’avantage de maitriser la composition et la répétabilité de nos formules adaptées aux contraintes industrielles et aux besoins de nos clients», assure Vincent Vial. Même démarche chez Gepack Europe, transformateur et distributeur de films. «En partenariat avec nos fournisseurs, nous diminuons les épaisseurs des films. Les clients sont demandeurs, mais la machinabilité est un frein. Aujourd’hui, nous atteignons une épaisseur de 15 microns sur un operculage en PET», indique Eric Le Borgne, pdg de l’entreprise.
Des stratégies différentes selon les fabricants
Il constate par ailleurs une tendance aux films pouvant être scellés sur des contenants réutilisables en inox ou en céramique. Cela nécessite de nouvelles formulations pour le scellage. «L’enjeu est de pouvoir souder sur ces matériaux de façon propre, lisse, sans laisser de résidus ensuite. Nous concevons des opercules sans colle, à base d’un polymère PE dont les propriétés intrinsèques permettent cela», explique Thierry Bonnefoy. Leygatech travaille également sur des solutions sans polyamide pour les films destinés aux emballages sous vide ou les films thermoformables, en remplaçant cette matière pertubatrice lors du tri par de l’EVOH, miscible dans du PE ou du PP. Par ailleurs, grâce à l’acquisition récente du fabricant français Propyplast (qui produit notamment des films d’operculage et pour la lamination), Leygatech muscle son offre à base de PP. «Avec le portfolio de Propyplast, nous serons par exemple en mesure de remplacer un opercule en aluminium, enduit d’un polymère pour le souder au pot, par un PP ou un complexe PP-EVOH-PP à moindre coût, mais ayant les mêmes fonctionnalités», assure Thierry Bonnefoy. La société Gepack Europe a pris le parti de se focaliser sur les solutions monomatières en PET. «Pour moi, c’est l’avenir. Le PET peut être recyclé dans une circularité et à nouveau utilisé dans des emballages pour l’alimentaire. Plus on augmente son épaisseur, plus sa barrière est élevée. Si nous devons ajouter une barrière, nous choisissons une barrière minérale comme de l’AlOx, plutôt que de l’EVOH», souligne Eric Le Borgne. Il remarque une nouvelle attente : «pour les operculages et les flowpacks, nos clients souhaitent éviter d’utiliser des films BOPP pour privilégier des films compostables. Notre gamme de films compostables – y compris en home compost – permet l’operculage sur des barquettes compostables (en pin, fibres de canne à sucre, etc.) ou en carton mais également des utilisations flow-wrap ou sur machine VFFS», détaille-t-il.
De nouveaux types de films nécessitant d’adapter les machines
Les fabricants de films poursuivent leurs investissements. Chez Leygatech, «nous rétrofitons des machines car certaines ne permettaient pas d’obtenir un nombre de couches de matière première plus élevé, ou une répartition adaptée des couches. Pour produire des films monomatières efficaces, ceux-ci doivent cumuler beaucoup de couches – 7 à 9, contre 1 ou 3 pour des films classiques. En effet, plus on utilise de grades différents de PE, plus on décline ce polymère en diverses propriétés pour compenser les films multi-matières. Les machines doivent donc être adaptées», explique Thierry Bonnefoy. Sealed Air a investi plus de 100 millions d’euros dans son site d’Epernon pour adapter les lignes à l’usage de certaines résines, et à s’affranchir d’autres résines. En effet, le groupe compte par exemple dans ses gammes des films intégrant 30% de matière recyclée chimiquement, issue des déchets consommateurs, ainsi que des films utilisant seulement 5% d’EVOH pour répondre aux demandes de certains pays. «Nous nous sommes aussi équipés de machines pour réintégrer nos déchets directement dans la production, et de systèmes pour contrôler le pourcentage des différentes résines dans nos formules. Nous avons pris des risques, en décidant par exemple de ne pas descendre en dessous d’une certaine barrière, car la protection de l’aliment doit primer avant tout», assume Arnaud Brunet. Sealed Air prévoit de lancer prochainement des sachets de très grande contenance, recyclables et certifiés par l’institut Cyclos-HTP, une référence reconnue dans toute l’Europe du Nord. En attendant un consensus à l’échelle de toute l’Europe…