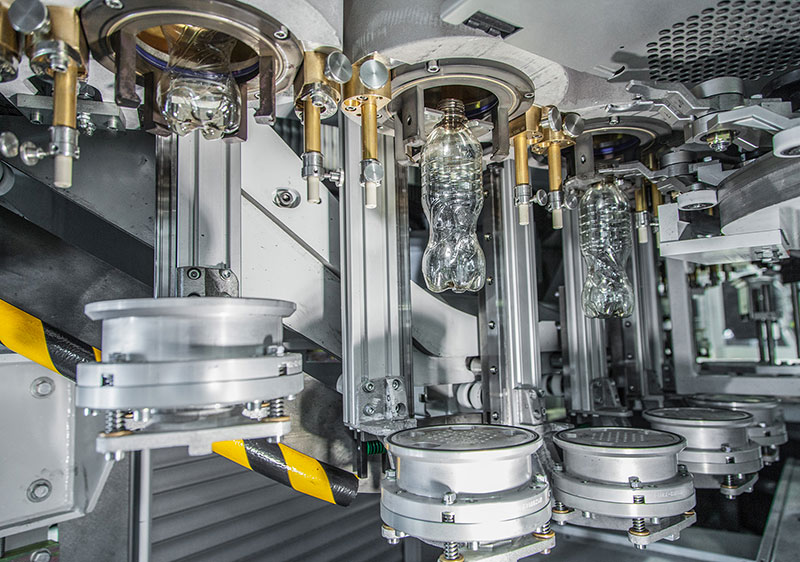
Le PET recyclé met les souffleuses sous pression
publié le mercredi 30 octobre 2024
Abonnez-vous à la revue pour lire la suite de l'article
s'abonner
Ce n’est pas tant la présence de PET recyclé dans la résine des préformes qui représente un nouveau défi pour l’industrie de l’emballage, même à taux élevé, que la diversité des grades de résine disponibles sur le marché. Il est néanmoins possible de mettre en œuvre des ajustements automatiques afin de réguler la performance de soufflage.
Incorporer au minimum 25% de matière recyclée dans les bouteilles* en PET à partir de 2025, puis 30% dans toutes les bouteilles en plastique à compter de 2030 : tels sont en substance les commandements inscrits dans le décret n° 2021-1610 du 9 décembre 2021 que devront appliquer les producteurs de préformes, les transformateurs, les embouteilleurs, etc., mais aussi, indirectement, les fabricants de souffleuses. «La présence d’une quantité plus ou moins importante de PET recyclé (rPET) dans les préformes est une réalité depuis des années. Hormis quelques paramétrages machine à revoir, cela n’a posé de problème à pratiquement aucun fabricant de souffleuse ni utilisateur… tant que la qualité de la matière première est restée stable», commente Alexandre Huet, responsable produit Soufflage & Couches barrière chez Sidel.
Contrôle de production et ajustements
En pratique, si l’élargissement de la fenêtre de «processabilité» des équipements opérée plusieurs années porte ses fruits, la variabilité croissante des résines justifie de plus en plus le recours à des systèmes d’optimisation automatique des réglages (chauffe, ventilation, soufflage, etc.), à l’instar de la solution Sidel IntelliADJUST™. Proposé en option sur les nouvelles souffleuses et disponible également en retrofit, ce dispositif vise à affranchir la machine des anomalies de production pouvant résulter, entre autres causes, d’une absorption fluctuante de la chaleur par les préformes en raison de variations de caractéristiques. «Le fonctionnement d’IntelliADJUST™ repose sur le contrôle de l’épaisseur des bouteilles en sortie de souffleuse, à différentes hauteurs, de façon à détecter d’éventuelles dérives et, le cas échéant, à appliquer les corrections adéquates au niveau de la chauffe et du soufflage, explique le responsable produit. La machine peut de la sorte compenser automatiquement certaines différences de grade d’un lot ou d’un sous-lot de préformes à l’autre, et ceci avec une cadence d’analyse de 90 000 bouteilles/h si nécessaire».
Réduction des épaisseurs
Pour mieux appréhender les difficultés auxquelles ses clients pourraient être confrontés dans le domaine du soufflage, Sidel a par ailleurs mis sur pied une véritable ligne pilote de recyclage dans son usine d’Octeville (Seine-Maritime). «Nous allons jusqu’à injecter et souffler les préformesen bouteilles que nous allons recycler plusieurs fois de suite afin d’étudier la qualité des résines ainsi obtenues et, in fine, de développer de nouvelles solutions pour perfectionner nos équipements…». En ce qui concerne les bouteilles en PET, on se souvient que Sidel avait déjà marqué les esprits il y a une vingtaine d’années avec le lancement d’Actis (Amorphous Carbon Treatment on Internal Surface), un revêtement plasma interne susceptible de multiplier par cinq les durées de conservation des boissons (principalement gazeuses ou sensibles à l’oxydation) à épaisseur de contenant identique. Pour Alexandre Huet, Actis fait partie de ces procédés qui devraient connaître un regain d’intérêt dans le contexte actuel de renchérissement du rPET. D’une part parce qu’il s’avère pleinement compatible avec les impératifs techniques du recyclage, comme l’a encore démontré récemment l’obtention de la certification américaine APR (Association of Plastic Recyclers APR), et d’autre part parce que sa mise en œuvre peut se traduire par de substantielles économies sur le poste des matières premières. «Dans le cas d’une bouteille de boisson gazeuse de 500 ml, ce dépôt de carbone amorphe d’à peine 50 nanomètres d’épaisseur permet d’alléger le contenant de 20% (19 g au lieu de 24 g) tout en faisant passer la durée de vie du produit de 10 à 24 semaines», souligne le responsable produit. Des possibilités d’autant plus intéressantes que cette solution, initialement exécutée sur un équipement «standalone», est désormais disponible en configuration intégrée soufflage/revêtement plasma/remplissage (EvoBLOW™ Combi) avec des cadences pouvant atteindre 40 000 bouteilles/h.
Unité porte-moule coulissante
Le positionnement moyenne cadence (3 000 à 18 000 bouteilles/h) de Serac dans le soufflage (linéaire en l’occurrence) n’empêche pas cet autre fabricant généraliste de prendre lui aussi en compte le besoin de productivité accru d’une partie de sa clientèle. «Aujourd’hui, le volume maximal des contenants fabriqués sur la SBL (Serac Blower Linear)est de 3 l. Quant à la cadence, elle culmine à 18 000 bouteilles/h au moyen de 12 cavités, avec un temps de cycle de 2,4 secondes», précise Laurent Penet, responsable produits/soufflage. Une cadence réalisable avec des bouteilles de 200 ml, mais qui descend toutefois à 12 000 unités/h pour des bouteilles de 1 l, avec une machine à huit cavités. Du moins pour l’instant…
Productivité accrue signifie également accès aisé à l’intérieur de la machine et visibilité sur l’intégralité du processus afin de faciliter les différentes interventions, en particulier le changement de moule. «Grâce à une unité porte-moule coulissante, les changements de format sur la SBL s’avèrent rapides et sécurisés», argumente Guillaume Leroux, responsable marché produits sensibles.
Optimisation énergétique
Olivier Perche, directeur des ventes de 1 Blow, met lui aussi en avant l’accessibilité et la rapidité des changements de formats de ses machines, avec, en outre, la capacité de réutiliser des moules existants du genre demi-coquilles (par le biais d’un système d’adaptation) si le client en a l’usage sur d’autres équipements. Mais le porte-parole de ce pure player du soufflage linéaire met encore davantage l’accent sur l’efficacité énergétique de ses matériels (1 à 6 cavités, 1000 à 9000 bouteilles/h). «Les économies d’énergie, c’est notre marque de fabrique !». Pour preuve l’installation en standard de systèmes de récupération de l’électricité lors du freinage des servomoteurs. «Nos machines ont beau être cycliques, certains mouvements sont continus et peuvent donc transformer instantanément ces freinages autrement qu’en chaleur, avec à la clé une économie de 2 à 3%». Pour aller encore plus loin dans l’optimisation énergétique – et toujours en standard –, 1 Blow récupère également la pression d’air résiduelle après soufflage pour la transférer vers certaines fonctions pneumatiques. Au niveau des fours, mentionnons enfin la possibilité d’équiper les lampes de réflecteurs céramique destinés à focaliser le rayonnement infra-rouge pour en diminuer la consommation de 30 à 40%.