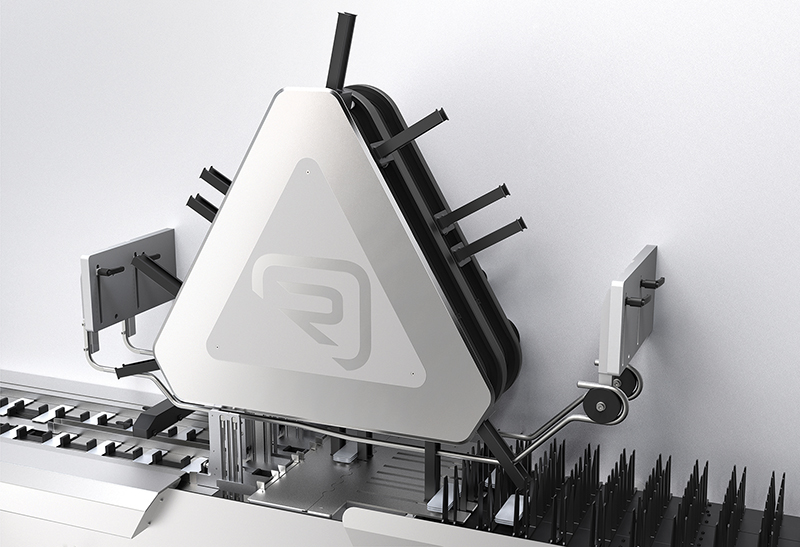
L’efficience et la durabilité se combinent sur les lignes blisters
publié le dimanche 31 mars 2024
Abonnez-vous à la revue pour lire la suite de l'article
s'abonner
L’engagement des marques en matière d’éco-conception se traduit par une évolution de la composition des blisters intégrant du full PP ou PE, ou encore des structures recyclées ou hybrides pour réduire la teneur en aluminium, voire des blisters entièrement papier. Ces changements apportés aux produits conduisent les fabricants de machines et conditionneurs (Romaco, Marchesini, Uhlmann, Körber Group) à s’adapter, revoir leurs machines et leurs process pour aider leurs clients cosmétiques et pharmaceutiques à produire de manière plus efficiente et durable, sur un marché en croissance continue. D’ici 2029, le marché des machines d’emballages blisters va augmenter de 4,3% à 762,9 millions de dollars, selon 24MarketReports*.
Le blister est très utilisé dans la pharmacie, parapharmacie, nutraceutique et cosmétique, comme mode de conditionnement et de présentation des comprimés et gélules à la fois efficace, hygiénique, sûr et inviolable. Les volumes vont continuer d’augmenter, d’après le cabinet 24MarketReports, face au développement de ces marchés d’application à l’échelle mondiale, aux réglementations strictes concernant la sécurité et l’intégrité des produits, et avec la nécessité d’améliorer l’efficacité et l’automatisation des procédés d’emballage. De fait, les machines blisters intègrent de plus en plus de robotique, d’automatisation et de contrôle numérique, pour améliorer les performances, la flexibilité et la fiabilité des opérations, en s’adaptant aux nouvelles tendances dans l’éco-conception des blisters et la performance environnementale.
Économiser la matière et l’énergie
Acteur très présent sur ce marché, Romaco contribue à l’évolution de la demande vers des blisters plus durables, en coopération avec des fabricants de films, et investit dans ses activités de R&D pour s’adapter aux besoins, selon Andreas Detmers, directeur R&D chez Romaco Pharmatechnik. «L’accent est actuellement mis sur les films sans PVC en PET, PP, PE ou papier et sur le traitement de monomatériaux pour améliorer la recyclabilité», indique-t-il. Un autre axe est d’économiser la matière. «Dans notre centre spécialisé sur les formats et les films PacTech, nous fournissons l’expertise et la technologie nécessaires pour tester les films de nos partenaires en mode industriel. Nous analysons ainsi un nombre important de paramètres tels que la température ou la pression des différents composants de la machine, par exemple de la station de formage, des plaques chauffantes, des rouleaux de scellage et du préchauffage du film d’operculage. L’objectif est d’optimiser des facteurs tels que les propriétés barrières, la sécurité des processus, la consommation d’énergie et la productivité pour s’adapter aux besoins de nos clients». Ce faisant, Romaco déploie son approche durable et efficiente jusqu’à ses machines. Exemple : la gamme de blisters Unity 600de Romaco Noack consomme près de 50% d’énergie de moins que le modèle précédent. L’économie provient notamment d’un système de transfert très efficace des blisters vers l’encartonneuse avec une gestion de l’air à la demande et des points de contact 100% étanches. La machine dispose également d’un moniteur d’énergie avec une fonction «économie d’énergie» automatique intégrée. En mode veille, la consommation d’énergie et d’air comprimé peut être réduite, sans avoir d’impact négatif sur l’efficacité globale de l’équipement (OEE). Autre particularité : la consommation d’air est automatiquement réduite lorsque la machine ne fonctionne pas, ce qui empêche les fuites minimes dans les tuyaux et les vannes, et réduit considérablement la consommation à long terme.
Automatisation et efficacité
De fait, Romaco a réalisé de nombreux progrès en matière de durabilité. Quelques exemples cités par Andreas Detmers : les plaques chauffantes à isolation thermique des stations de formage des lignes blister réduisent la consommation d’énergie et, par conséquent, la chaleur perdue dans les salles blanches climatisées. La température de la station de scellage peut être régulée via trois zones de chauffage et contrôlée individuellement pour l’adapter aux exigences réelles du processus de scellage et la réduire de manière globale. «Toutes nos lignes sont aussi équipées d’une carcasse extérieure en verre acrylique 100% recyclé», pointe-t-il. D’autres améliorations visent l’empilement des blisters par le bas et une stabilité contrôlée par guidage. «Seules les piles complètes sont transférées vers l’encartonneuse», note-t-il. Un logiciel breveté enregistre toutes les étapes du processus pour le rattrapage des écarts et assurer une traçabilité complète des blisters dès les étapes amont. En outre, l’industrie pharmaceutique demande de plus en plus d’avoir recours au contrôle automatique d’échantillons en cours de processus sur les machines (in-process control, IPC) pour plus d’efficacité. Un autre avantage est la conception Poka-Yoke des pièces de formats, «une fonctionnalité très recherchée, selon Andreas Detmers, car elle réduit le taux d’erreur lors des changements de formats, minimisant les temps d’arrêt et augmentant ainsi la productivité». Par ailleurs, Romaco est attentif à la performance de ses machines, mais aussi de sa propre production. «Toutes nos lignes blisters sont disponibles dans une version climatiquement neutre. Leur empreinte CO2 est calculée en tenant compte de tous les composants, matériaux et itinéraires de transport. Ces émissions sont ensuite compensées par des projets Gold Standard», conclut Andreas Detmers.
Standardisation et personnalisation
En outre, et sur un marché de volumes en croissance, la réactivité et la flexibilité sont nécessaires pour fournir des solutions en temps record aux laboratoires et à leurs sous-traitants. Un exemple avec le groupe Marchesini qui a fourni à PharmaPac UK, une solution monobloc intégrée robotisée, composée d’une machine de conditionnement sous blister et d’une encartonneuse, disponible dans ses stocks et personnalisée en l’espace de six mois aux spécifications de son client. Une réactivité rendue possible grâce à la nouvelle approche de standardisation de Marchesini en matière de lignes blister et une production par lots. Sa division blister, basée à Carpi, en Italie, a travaillé main dans la main avec PharmaPac UK sur ce projet compliqué. Ces dernières années, Marchesini a standardisé tous les composants électriques et pneumatiques nécessaires à sa gamme de produits. «Cela signifie que l’approvisionnement de tous les composants critiques a été plus efficace, limitant ainsi l’impact de la pénurie mondiale», pointe la société.
Modularité des solutions
Chez Körber Pharma, priorité est donnée à l’agilité de ses solutions pour anticiper les futurs besoins du marché. Sa ligne blister automatique, disponible en version une ou deux voies, est idéale pour les petits lots, avec une grande variété de changements et de formats d’emballage, offrant efficacité et flexibilité pour un traitement jusqu’à 400 blisters par minute. «Notre machine de dernière génération
BE4 Blisterest conçue pour traiter tous les nouveaux matériaux à venir, notamment le PP», souligne Erk Wolters, vice-président des ventes chez Körber Pharma Packaging Machines. Avec le fonctionnement à deux voies, la vitesse peut être réduite, permettant ainsi des principes de dosage plus simples. Le concept 100% modulaire peut à tout moment évoluer vers une solution haut débit allant jusqu’à 800 blisters par minute. Sa technologie brevetée garantit une étanchéité constante et de haute qualité. Autre avantage : la plateforme Blister Expert propose une interface de type smartphone avec un grand écran personnalisable et de nombreuses fonctions spécifiques au client. Avec sa blistéreuse BEC 400, Uhlmann couvre également un large panel de besoins et de formats du marché. Couplée à ses services numériques, la ligne forme un système complet coordonné entre les systèmes d’alimentation, la blistéreuse et l’étuyeuse sur une longueur de moins de neuf mètres. Conçue pour les étuis de grand volume et le conditionnement de plusieurs blisters en un seul emballage, la ligne dispose de la plus large gamme de formats de la famille BEC, selon le fabricant. Avec une vitesse allant jusqu’à 400 blisters par minute, elle conditionne toutes les configurations blisters/étuis sur deux voies avec des performances élevées, des changements de format rapides en moins de 30 minutes, un nettoyage facile et une utilisation intuitive via l’IHM SmartControl, qui garantit des performances et une sécurité maximale pour le conditionnement de différentes tailles de lots.