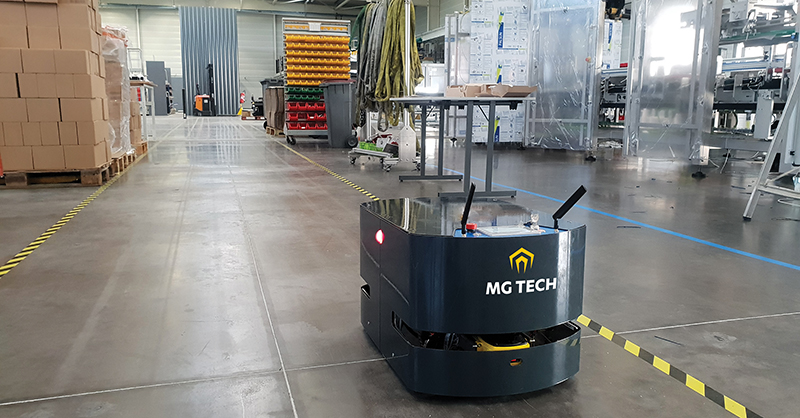
Les robots mobiles autonomes font une percée dans les IAA*
publié le dimanche 30 octobre 2022
Abonnez-vous à la revue pour lire la suite de l'article
s'abonner
Si les AGV ont ouvert la voie à la robotique mobile dans les usines agroalimentaires, les AMR, beaucoup plus autonomes et simples à mettre en œuvre (grâce à leur intelligence embarquée), devraient accélérer le mouvement.
Les véhicules à guidage automatique ou AGV (Automated Guided Vehicles) font désormais partie du décor dans les usines, où on leur confie généralement des tâches d’intralogistique peu valorisantes et/ou pénibles pour les employés. Dans le cas du nouveau Warehouse Freezer AGV de John Bean Technologies, l’idée est ainsi de transporter des charges de plus d’une tonne et de les lever jusqu’à 10 m de hauteur grâce à un mât hydraulique à trois étages en fonctionnant par -23°C dans les entrepôts de congélation.
Si la valeur ajoutée de ces robots AGV est considérable pour ce type de mission et dans ce type d’environnement, il y a d’autres tâches, qui relèvent peut-être moins de la logistique pure et dure, pour lesquelles une nouvelle génération de matériels semble prendre l’ascendant. Ces derniers, connus sous les appellations AIV (Autonomous Intelligent Vehicle) ou AMR (Autonomous Mobile Robot), se distinguent par une flexibilité bien supérieure, comme l’explique Gilles Gomila, responsable intégration d’Omron: «les AGV sont un peu comme des bus, avec des trajets et des horaires à respecter, tandis que les AMR ressemblent davantage à des taxis».
En effet, alors que les premiers suivent un chemin prédéterminé identifié par des marquages au sol, des bandes magnétiques, des réflecteurs ou d’autres repères, les seconds sont capables de se mouvoir en sécurité dans leur environnement de façon adaptative grâce à un ensemble de techniques embarquées, en particulier la télémétrie Lidar (Laser imaging detection and ranging) 2D ou 3D.
Infrastructure réduite
Dans les usines, cette autonomie de déplacement non seulement simplifie la mise en œuvre des robots, mais correspond aux objectifs actuels de production flexible dans l’industrie. «C’est la raison pour laquelle Omron n’a jamais proposé d’AGV – d’autant qu’il y avait déjà des acteurs bien installés – et préféré passer directement à l’AMR, à partir de 2010 en R&D et de 2015 en déploiement industriel», précise Gilles Gomila.
Chez le constructeur de fins de lignes de conditionnement MG Tech, qui s’est lancé dans les AGV il y a une dizaine d’années, l’historique est différent mais le constat est le même. «Désormais, nos développements portent exclusivement sur les AMR, indique Serge Pitois, responsable produits de l’entreprise : nous sommes toujours en mesure de fournir des AGV, si le client nous le demande, mais depuis trois ans, la dynamique du marché est clairement en faveur des robots mobiles autonomes».
Ce qui a changé la donne, c’est la démocratisation des composants nécessaires aux AMR, qui profitent notamment des retombées de la montée en gamme des équipements automobiles. Aujourd’hui, d’après Serge Pitois, les AMR ne seraient que plus que 30 à 40% plus chers que de simples AGV. Et cet écart diminue encore si l’on raisonne en coût global, puisque les AMR n’exigent aucune infrastructure au sol. «En fin de compte, même s’il faut quand même dépenser davantage pour les AMR, de plus en plus d’utilisateurs les préfèrent aux AGV en se disant – à juste titre – qu’ils seront plus faciles à intégrer dans leur flux de production si celui est amené à évoluer dans le temps», observe le responsable produits de MG Tech.
TRS sous contrôle
En France, Omron aurait à ce jour livré plus de 300 AMR, surtout dans le secteur automobile, les semiconducteurs et les cosmétiques. Dans l’agroalimentaire, bien que nouveau, ce mouvement paraît bien enclenché, se félicite Gilles Gomila : «les IAA, comme l’ensemble des industries manufacturières, aspirent à une plus grande agilité en termes de charge. Elles veulent aussi pouvoir modifier plus rapidement leur production, lancer des séries limitées, etc., ce qui n’est pas toujours compatible avec la stabilité des séquences logistiques exigée par les AGV. Alors que les AMR, eux, s’accommodent sans difficulté de séquences variables».
Le responsable intégration d’Omron prend l’exemple d’un fabricant de pâtisseries dans l’atelier duquel
un AMR est chargé d’une part de l’approvisionnement bord de ligne, en tâche de fond, et d’autre part de la récupération des brisures de pâtisseries (un sous-produit recherché par d’autres industriels) en tâche à la demande. «Il est difficile actuellement de trouver du personnel pour assurer ces fonctions peu gratifiantes, alors qu’un AMR les réalise sans jamais faillir et peut ainsi optimiser le taux de rendement synthétique (TRS)», argumente Gilles Gomila. Parmi les applications types des AMR dans les IAA, il cite également les échantillonnages qualité sur les lignes ainsi que le co-packing pour les promotions ou les événements spéciaux (Halloween, Noël, etc.) qui nécessitent beaucoup de main-d’œuvre.
Configurationssur-mesure
Selon Serge Pitois, si la rentabilisation de ces matériels (valant de 60 000 à 100 000 euros) est sans doute plus aisée pour les entreprises de grande taille, les structures plus modestes peuvent aussi y trouver leur intérêt grâce à la diminution des manipulations humaines et des arrêts machines. «De plus, il faut voir les robots autonomes comme un saut technologique incontournable à terme, alors autant ne pas trop attendre», estime le responsable produits. MG Tech propose à l’heure actuelle trois modèles : le Minibot (680 x 450 mm), capable de déplacer des charges jusqu’à 100 kg à 5 km/h au maximum ; l’Evobot(1520 x 780 mm), conçu pour le déplacement de charges jusqu’à 2000 kg à 7 km/h, et enfin l’Evobot-T (1100 x 700 mm), dédié au tractage de charges lourdes.
Pour tous ces modèles, une station de biberonnage permet au(x) robot(s) de se recharger automatiquement entre deux missions, en fin d’exercice ou encore à la demande d’un opérateur. «Le Minibot est très à l’aise dans l’approvisionnement bord de ligne, tandis que l’Evobot cible davantage la manipulation des palettes, commente Serge Pitois. Mais attention, le véhicule ne suffit pas, prévient-il. Un projet de robotique mobile doit aussi aborder la question des équipements : convoyeur de réception/sortie (bacs, caisses, palettes…), lifter (pour soulever et déposer les charges), bras robotisé… Et là, c’est du sur-mesure, contrairement à la base mobile, nettement plus codifiée».
Gestion de flotte
En ce qui concerne l’intégration des AMR aux systèmes informatiques des entreprises, tout dépend du nombre de robots en présence. S’il n’y en a qu’un, cette intégration n’a rien d’obligatoire. S’il y en a plusieurs, le premier logiciel à entrer en scène est le FMS (Fleet Management System), autrement dit le gestionnaire de flotte. Chez Omron, ce dernier est baptisé Enterprise Manager : «agissant en véritable chef d’orchestre, il peut piloter jusqu’à 100 véhicules de notre gamme – parmi les modèles LD 60/90 (en référence à la charge, en kg), LD 250, MD 650 et HD 1500 – et leur donne des ordres en fonction de la priorité des missions à accomplir, de la position de chaque AMR par rapport au point à atteindre, du niveau de charge électrique, etc.», détaille Gilles Gomila.
L’étape suivante réside dans la connexion du FMS au logiciel de pilotage de la production (MES), au progiciel de gestion intégré (ERP) ou encore au système de gestion d’entrepôt (WMS). «Plus ou moins important selon le logiciel à interfacer, ce développement informatique rentre dans le cadre de la maîtrise d’œuvre globale que nous assurons systématiquement pour ce type de projet», insiste Serge Pitois. Quant à la cohabitation éventuelle de robots de différentes marques dans une même usine, le responsable produits de MG Tech reconnaît que c’est «un vrai sujet… non traité pour l’instant, faute de standardisation».