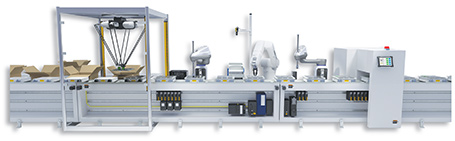
Maintenance prédictive : Omron convertit les données en leviers de productivité (publi-communiqué)
publié le lundi 26 juillet 2021
Fonctionnement optimal des lignes de production, gestion des fluctuations de consommation et des perturbations de chaînes d’approvisionnement, qualité et traçabilité des produits, flexibilité de la personnalisation sont autant de défis qui agitent plus encore en cette période de Covid les industriels, secteurs agroalimentaire et de l’emballage en première ligne.
Un premier bilan laisse entrevoir comme évident la nécessité pour les entreprises d’utiliser les données de leurs équipements pour accroître leur productivité et leur compétitivité. Dans ce schéma la maintenance prédictive a de toute évidence son rôle à jouer.
La puissance de la maintenance prédictive
Les arrêts machines non planifiés sont un casse-tête auquel n’importe quelle stratégie de maintenance apporte des réponses moyennant un coût, un impact humain et environnemental très variable. Mais pour Omron, acteur leader dans l’automatisation industrielle, il est évident que les bénéfices de la maintenance prédictive sont bien supérieurs. Elle permet d’utiliser les données existantes pour les convertir en informations révolutionnant ainsi les processus de production. Les défaillances de chaque composant de l’écosystème de production peuvent être anticipées et les pertes de productivité et impacts négatifs sur la notoriété de l’entreprise sont par conséquent maîtrisés Par ailleurs, l’entrée dans l’ère de l’industrie 4.0 rappelle l’impact humain de la maintenance. Les solutions numériques permettent de réduire la pression générée par un arrêt machine sur les équipes et bien qu’aucune stratégie de maintenance ne permette de garantir une disponibilité des équipements à 100%, les solutions de maintenance préventive et prédictive apportent de réels bénéfices humains.
Quand les données deviennent des informations stratégiques
Le numérique offre d’incroyables facilités pour la mise en œuvre d’une maintenance prédictive. Il suffit en effet de collecter les données des composants déjà disponibles et d’analyser ces informations. Les vibrations ou la température anormale de certains composants peuvent par exemple être les révélateurs d’un dysfonctionnement. Le vecteur ou la vitesse d’un changement peuvent également permettre de prédire un échec. Ainsi la première étape d’un dispositif de maintenance prédictive consiste à identifier les éléments critiques du processus et à constituer une base de référence des données inhérentes aux capacités du système. La seconde étape repose sur l’évaluation des options de collecte de données. Pour cela, une couche d’automatisation peu coûteuse, s’interfaçant avec le système de supervision peut s’avérer utile.
Les premières remontées de données laisseront entrevoir le niveau de complexité. Il s’agira alors de filtrer les interruptions dites normales pouvant entraîner des fluctuations de données, tel que le chargement périodique d’une machine pouvant occasionner une pointe de vibrations, de celles traduisant une réelle dérive.
Considérant le rôle essentiel de la maintenance prédictive, la dernière génération de robots Scara d’Omron, est équipée d’une fonctionnalité de maintenance intégrée révolutionnant le contrôle des robots, machines, capteurs de vision et la sécurité composants avec une fluidité sans précédent. Le virtuel et le réel fusionnent même en toute transparence.
Les tâches critiques telles que celles de la répétabilité sont ainsi mieux maîtrisées notamment avec l’émergence de nouveaux matériaux, de même que les environnements de travail et ce, malgré la multiplication des robots autonomes.
Force est de constater que le nombre croissant de données et le développement d’une offre d’outils d’analyse simples associés à un dispositif de maintenance préventive ont permis de rendre les lignes de production bien plus agiles hissant la fonction maintenance au rang de levier stratégique de productivité robots Omron à l’appui.