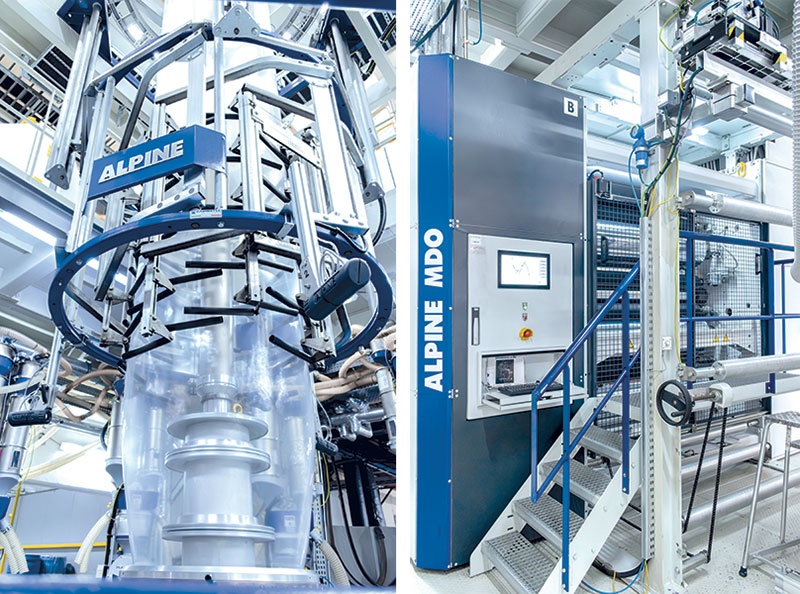
Production of flexible mono-material packaging in Latin America
publié le lundi 14 octobre 2024
The Colombian packaging manufacturer Microplast Coldeplast, based in Medellín, has invested for the first time in a 5-layer blown film line with inline MDO from Hosokawa Alpine. The plant went into operation in 2023 and produces PE and MDO-PE films for various laminating films, which are then used in flexible packaging solutions. This not only increases the company’s production capacity, but also contributes to the circular economy in the packaging industry.
The company has been producing flexible packaging solutions at two production sites in Medellín since 1956, including for food, pet food, household and care products and building materials. Microplast Coldeplast mainly processes PE, PET, BOPP, PA, aluminium and paper and supplies its customers with rolls and bags. In line with its corporate strategy and global market trends, the company needed to increase its production capacity and make its products more recyclable. “In many markets, the demand for recyclable packaging has risen sharply or is even encouraged by laws and government regulations. To remain competitive in the long term and open up new markets, we need to adapt our technology, » says Lina Fajardo, Head of Technical Marketing and Sustainability at Microplast Coldeplast. PET and BOPP should therefore be replaced by PE mono-material solutions in some laminations.
In search of a partner to realize this project, Microplast Coldeplast turned to Hosokawa Alpine. The decisive factor in this decision was the global experience that the Augsburg-based machine and plant manufacturer has in the field of full PE packaging solutions. « As a pioneer in MDO technology, we have been working with monoaxial stretching of blown film for over 25 years. Over 100 of our systems are in use around the world, » says Marcelo Gräf, Senior Sales Manager at Hosokawa Alpine. The company relies on customised systems that are developed and adapted specifically for the customer’s product.
The MDO process begins with a heating phase: here, the film is conveyed on heated rolls and brought to the ideal temperature. In the following stretching phase, the film is stretched between two rollers to achieve the desired stretching ratio. At the same time, the film thickness is reduced, while optical and mechanical properties such as transparency, rigidity and barrier properties are improved. « The thinner film thickness reduces the amount of material required. This not only conserves resources, but also saves on material costs, » explains Gräf.
Microplast Coldeplast uses a 5-layer blown film line from Hosokawa Alpine with inline MDO and a layflat width of 1600 mm. The company then produces full PE films, which are further processed into various flexible packaging solutions. A particular challenge in the development of the system was, in addition to some specific technical features, the process stability with a low film thickness of 25 µm. The new plant has enabled the packaging manufacturer to increase its production capacity to over 400 million linear metres per year.