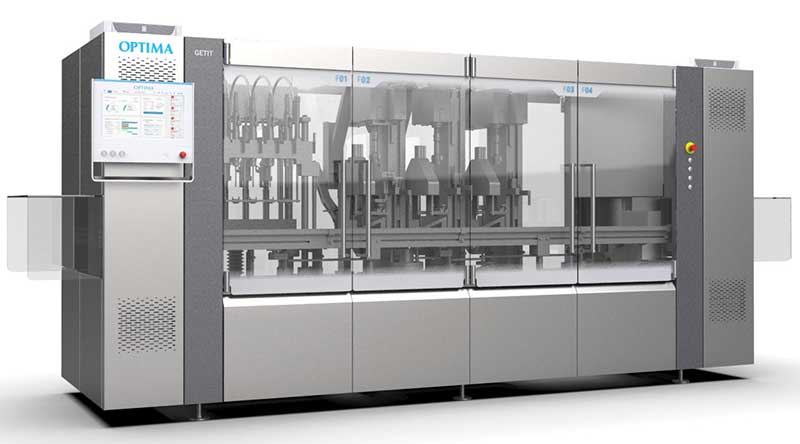
Remplisseuses : en quête d’une flexibilité maximale
publié le jeudi 31 août 2023
Abonnez-vous à la revue pour lire la suite de l'article
s'abonner
Le niveau d’exigence augmente pour les secteurs cosmétiques et pharmaceutiques qui ont besoin de remplisseuses modulaires, évolutives et flexibles de la part des fabricants de machines (Optima, IMA, Syntegon, Groninger) pour une mise sur le marché rapide de leurs produits. Dans la pharmacie, la complexité vient des thérapies personnalisées (cellulaires et géniques) et de petits lots à forte valeur ajoutée qui encouragent l’utilisation de conteneurs prêts-à-l’emploi pour avoir une flexibilité maximale. La révision de l’Annexe 1 (injectable) implique également l’adoption de technologies barrière sur les lignes. Comme dans les autres secteurs, la numérisation et l’automatisation aident à s’adapter aux nouvelles contraintes.
Inflation, problèmes d’approvisionnement, multiplication des produits et formats, exigences de sécurité et environnementales en hausse … «Les secteurs cosmétiques et pharmaceutiques sont en évolution rapide avec un environnement commercial qui a rarement été aussi difficile à gérer pour nos clients», constate Jens Betsch, directeur marketing chez Optima.
Gagner en flexibilité
« Les fabricants cosmétiques sont soumis à une pression énorme pour innover et la recherche de personnalisation dans les produits exige d’avoir des solutions d’emballage flexibles, de haute qualité et économiques», continue-t-il. C’est pourquoi le constructeur a développé des systèmes de remplissage modulaires et évolutifs, comme Optima Moduline Smart, pour accélérer les mises sur le marché. Parmi ses avantages : une grande flexibilité de format, une cadence jusqu’à 60 récipients par minute, un encombrement réduit, l’ajout facile de modules et des délais de livraison courts. De son côté, Groninger a transféré son savoir-faire stérile ou aseptique aux produits OTC, de diagnostics et aux compléments alimentaires conditionnés en flacons avec la flexcare 10, qui offre un changement rapide des pièces de format pour traiter une large gamme de produits avec peu de temps d’arrêt, selon Otto Helmle, directeur des ventes consommateur produits de santé et cosmétique. «Grâce à ce concept de machine, nous répondons aux exigences de l’industrie de traiter les produits de manière sûre et efficace, mais aussi flexible», note-t-il. La flexibilité s’applique également aux volumes de remplissage de 0,1 à 400 millilitres et jusqu’à 4200 unités par heure.
Combiner complexité et efficacité
Dans la pharmacie, la difficulté est de combiner des processus de remplissage et fermeture complexes avec des exigences d’efficacité, de productivité et de fiabilité pour tous les types d’emballages et de lots. «Le principal défi est de gérer la pression sur les coûts pour lancer un médicament en un temps record», résume Jens Betsch, qui met en avant les solutions clés en main, fiables, intelligentes et intégrées d’Optima, comprenant une ligne de remplissage, un isolateur et, selon le produit, un lyophilisateur pour répondre à ces enjeux. Dans la pharmacie, c’est surtout sur les produits liquides que les contraintes de flexibilité et de rendement sont les plus fortes. «Cela résulte de l’augmentation du nombre de médicaments innovants administrés par voie parentérale pour traiter le cancer, les maladies génétiques ou encore auto-immunes», analyse Markus Heinz, chef de produits flacons chez Syntegon Technology. Les thérapies cellulaires et géniques, dites personnalisées, nécessitent la production de lots de plus en plus petits – entre 15 000 à 60 000 récipients à remplir et seulement quelques milliers pour les essais cliniques, voire 5 à 10 récipients par patient dans le cas d’une thérapie cellulaire autologue… Cela exige d’avoir des plateformes de production dédiées avec des changements rapides et de minimiser les pertes de produits à forte valeur ajoutée.
RTU et Annexe 1
La recherche de flexibilité dans les contenants, combinée à l’urgence de la mise sur le marché, alimente la croissance rapide des conteneurs prêts-à-l’emploi (RTU). «S’ils sont depuis longtemps l’apanage des seringues préremplies, ils le deviennent de plus en plus pour les flacons et les ampoules aussi bien pour les applications en vrac que les petits lots», avance Markus Heinz chez Syntegon, dont le dernier né de la série ALF 5000 permet le remplissage et la fermeture de conteneurs RTU, et peut être équipé de fonctions intelligentes (suivi individuel, etc.). Le rendement est de 36 000 flacons ou ampoules par heure. La variante «combi» remplit les deux formats (flacons et ampoules) sur la même plateforme.
En outre, et pour les médicaments injectables, la révision de l’annexe 1, applicable depuis août 2023, a un impact significatif pour les fabricants de médicaments stériles. «Le chapitre 2 recommande fortement l’utilisation de technologies appropriées pour ‘séparer’ les opérateurs des produits, à l’aide de systèmes barrières tels que RABS et d’isolateurs, avec un degré d’automatisation plus élevé», précise-t-il. Pour s’adapter à ces nouvelles exigences, Syntegon a lancé Versynta microBatch, une cellule de protection hautement flexible, qui complète la Versynta FFP (Flexible Filling Platform) modulaire, pour le remplissage automatisé de petits lots. «La solution microBatch atteint des cadences de 120 à 500 récipients par heure et permet un changement complet de lot en moins de deux heures», précise-t-il. L’isolateur réduit considérablement le risque de contamination. Le remplissage automatisé et le contrôle à 100% en cours de processus garantissent une qualité élevée constante.
Un autre axe dans la (bio)pharmacie vise l’automatisation et la numérisation. «La robotique permet de faire un grand pas en avant dans la protection et la qualité des produits, en minimisant l’intervention humaine », pointe Markus Heinz. Et la numérisation contribue au monitoring en temps réel des machines pour prendre des décisions fondées sur les données et l’optimisation des opérations. Ce que permettent les nouvelles solutions logicielles basées sur le cloud de Syntegon telles que Synexiopour la visualisation des données liées aux équipements et à la production, et le logiciel Monitor qui suit les indicateurs clés de performance. En complément, la solution Uptime, dévoilée sur le salon interpak cette année, aide à déterminer des axes d’amélioration concrets, par exemple en identifiant les motifs d’arrêt les plus fréquents d’une machine.