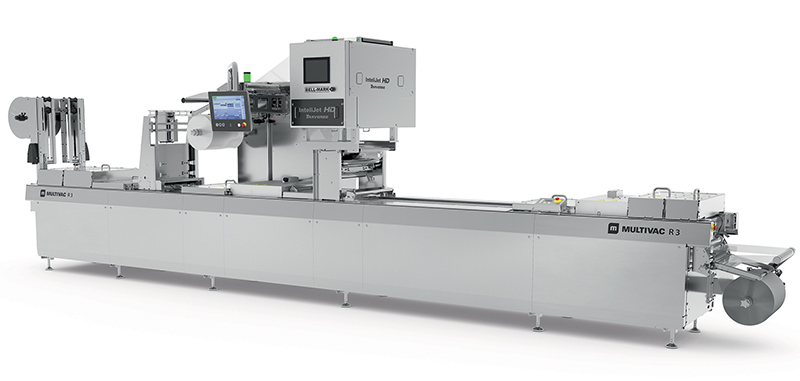
Thermoformeuses : plus d’efficacité, de flexibilité et d’automatisation
publié le jeudi 30 novembre 2023
Abonnez-vous à la revue pour lire la suite de l'article
s'abonner
Alimentées en bobines de films ou feuilles en plastique, les lignes de thermoformage conditionnent sous vide, dans des barquettes ou blisters, les flacons, ampoules, seringues, autres produits similaires et dispositifs médicaux. Objectif : préserver l’intégrité de ces composants et kits stériles à usage unique jusqu’à leur utilisation. Ces lignes intègrent également le scellage, la stérilisation, le marquage laser et l’étiquetage. Sur un marché pharmaceutique en croissance, et engagés dans des projets de relocalisation industrielle avec leurs clients, les fabricants de machines (Multivac, Ulma Packaging et Marchesini) mettent l’accent sur l’efficacité et la flexibilité de leurs machines, de plus en plus connectées avec l’usine du futur.
Kits de vaccins, de perfusion ou d’électrodes, ou sachets individuels de seringue pour usage unique, les applications de conditionnement sur les thermoformeuses médicales et pharmaceutiques sont variées, mais visent principalement des productions de moyennes à grandes séries dans un objectif de rentabilité. Fabricant de machines généraliste, Multivac a dédié un business unit à ces applications médicales pour développer des machines 100% conformes aux besoins. «Nous intervenons également pour conditionner et sceller des implants et prothèses en poches médicales sur des lignes en petites séries, une activité manuelle qui est en train d’évoluer vers des machines automatisées pour des raisons de rentabilité», souligne Hervé Houy, ingénieur commercial médical et pharmaceutique chez Multivac. La stratégie évolue aujourd’hui avec les besoins de l’industrie pharmaceutique, en particulier dans un contexte de relocalisation et réindustrialisation en France et en Europe.
Flexibilité et efficacité
La crise sanitaire a changé la donne et les big pharma sont engagées dans la régionalisation de leurs activités de production pour raccourcir les circuits et sécuriser leurs approvisionnements. Les fabricants de machines accompagnent cette dynamique industrielle, qui vise notamment les vaccins avec les seringues préremplies, mais aussi les produits biologiques injectables, dont certains nécessitent d’être emballés sous atmosphère modifiée. «Pour les industriels, relocaliser les productions signifie également produire autrement, en investissant dans l’automatisation», indique Hervé Houy. Multivac est ainsi sollicité pour des projets de rapatriement de productions sur le territoire français, une tendance de fond qui va s’étaler sur plusieurs années selon l’ingénieur commercial.
Parmi les évolutions sur les machines, une tendance depuis quelques années se confirme vers plus de flexibilité et de polyvalence, en encourageant la compatibilité avec différents types et dimensions d’emballage, mais aussi en optimisant l’espace pris par les équipements dans les salles blanches de production et en garantissant leur modularité (chargement devant/derrière…). La recherche d’efficacité se voit aussi dans les changements de formats et d’outillages. «Nos machines permettent de valider les changements d’outillage et les recettes d’utilisation chez nos clients, ce qui a contribué à des gains de temps considérables liés à ces opérations, qui pouvaient prendre 2 à 3 jours il y a quelques années et aujourd’hui moins de quatre heures sur des lignes entièrement automatisées», note-t-il. Illustration avec la nouvelle thermoformeuse R3, automatisée et compacte, dédiée à de l’entrée de gamme sur des cadences moyennes pour le conditionnement en emballages thermoformés standards de seringues jetables, fournitures de laboratoire, connecteurs, … souvent produits en grande série au niveau mondial. Cette machine a la capacité de traiter les films d’emballage recyclables en mono-matériau, sans former de plis, et demande peu d’entretien grâce à sa construction particulière et modulaire.
En parallèle, les machines évoluent vers l’usine 4.0, l’enregistrement des données pour la traçabilité et le suivi des performances en production. «On fournit à nos clients des rapports de lots qu’ils sauvegardent pour faire de l’analyse de données de production et de l’amélioration permanente», indique Hervé Houy. La maîtrise de la maintenance prédictive permet aussi d’anticiper les pannes sur les équipements et d’être plus efficace. Un autre axe vise l’automatisation des lignes aux postes de chargement et déchargement grâce à des robots. «On commence à être questionné sur l’utilisation des robots collaboratifs («cobots») capables d’accomplir des tâches simples en fin de ligne, et qui sont devenus moins coûteux et plus flexibles», ajoute-t-il.
Du manuel à l’automatique
Dans le but d’améliorer l’efficacité et la productivité des lignes d’emballage, l’automatisation est également l’un des axes de développement d’Ulma Packaging. La série TFS est notamment adaptée pour évoluer d’un système de conditionnement manuel à automatique pour les produits alimentaires ou médicaux. Un exemple est la thermoformeuse TFS 200, qui conditionne en emballage thermoformé à partir de deux bobines de films flexibles ou rigides. «En option, on peut réaliser du vide et une réinjection de gaz (MAP) à l’intérieur de ces emballages», précise le constructeur, qui met en avant les avantages de cette machine en termes de polyvalence, facilité d’utilisation et modularité pour les changements de format.
Cap sur l’usine 4.0 et les blisters mono-matériaux
Avec ses thermoformeuses, Marchesini met le cap sur un environnement pharmaceutique 4.0, en intégrant notamment la maintenance prédictive. Un exemple est la FB420, une machine d’emballage automatique à mouvement intermittent entièrement servomoteur, avec une construction en balcon, des stations servo-commandées indépendantes et contrôlées par PC. Cette machine thermoforme des barquettes pour les flacons, ampoules, seringues et produits similaires à partir de films tels que des stratifiés multicouches PVC, PET, polystyrène, PP, PLA. «Elle est 100% prête et testée pour tous les matériaux thermoformables durables, en particulier la production de blisters mono-matériaux», souligne la société, avec plusieurs autres avantages : robustesse, construction modulaire, simplicité d’utilisation et d’entretien, changement facile et sans outil. Cette solution offre une performance élevée, avec des rythmes de 10 à 45 cycles par minute, et une vitesse de production pouvant atteindre, par exemple, 1000 ampoules par minute ou 600 seringues préremplies par minute.