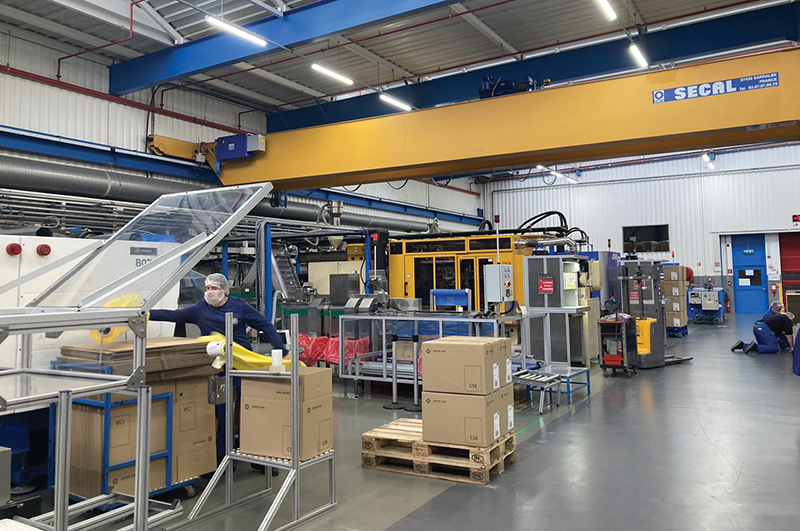
United Caps poursuit l’automatisation de son site de Wiltz
publié le jeudi 29 février 2024
Abonnez-vous à la revue pour lire la suite de l'article
s'abonner
Le fabricant luxembourgeois, United Caps, spécialiste des bouchons plastique et autres systèmes de fermetures de contenants alimentaires et de produits chimiques, investit dans son usine de Wiltz pour automatiser les fins de ligne tout en poursuivant la transformation de ses outils de production vers la fabrication de bouchons solidaires et/ou allégés.
Si le cœur de métier d’United Caps reste l’injection plastique, l’entreprise a su compléter son activité par des expertises connexes : étiquetage IML, impression pour les bouchons attachés, pose de joints étanchéité, ou encore assemblage de bouchons multi-composants (produits plus complexes, et à plus forte valeur ajoutée). Malgré un chiffre d’affaires en recul – 170 M€ en 2023 contre 185 M€ en 2022 – engendré par une consommation en berne et une chute des prix du coût des matériaux, le fabricant luxembourgeois reste optimiste et poursuit ses investissements. C’est le cas à Wiltz, son siège social, où est installée une usine trentenaire, certifiée ISO 14 001 et BCR-IOP. Le site d’une superficie de 3500 m² produit trois millions de bouchons par an, soit un tiers de la production totale du groupe. L’entreprise luxembourgeoise s’appuie, en effet, sur un parc industriel de dix usines en Europe et une autre installée à Kulim en Malaisie. «Notre stratégie a toujours été de produire pour les marchés locaux afin d’être au plus proche de nos clients et de leurs besoins industriels», explique Benoit Henckes, pdg d’United Caps.
Automatisation des fins de ligne
Articulée autour de trois halls de production, l’usine de Wiltz abrite un large panel de process technologiques et de savoir-faire industriels. Le premier hall est ainsi dédié à la production de capsules de café – avec pose d’opercule et étiquetage IML – mais également à la fabrication de bouchons twist-off pour bocaux. Adjacent, le 2e hall est, quant à lui, totalement dévolu à la production de bouchons pour bouteilles de lait et d’eau. Un cobot Doosan a été installé l’an dernier pour aider à l’étape finale de formage de cartons et de conditionnement des bouchons avant expédition dans des stocks box. «1,5 M€ ont été investis pour l’automatisation de ces deux halls. Les solutions de robots collaboratifs nous permettent de redéployer les opérateurs sur des postes plus stratégiques. Le prochain chantier concernera la mise en place de nacelles aériennes pour le convoyage des cartons et palettes vers des stations de filmage et d’impression en lieu et place des étiquettes. Les premiers essais sont concluants, les travaux démarrent et devront être finalisés avant le mois de juillet», détaille Steve Stockwell, responsable production de l’usine de Wiltz. Enfin, un dernier hall est spécifiquement occupé par les lignes de production de bouchons pour briques de lait. L’espace est en pleine effervescence : les équipes y terminent le montage d’une nouvelle ligne dédiée à la fabrication du bouchon 23-H PAKpour le compte d’Elopak. Constitué de trois pièces – le bouchon, le verseur avec filet et le putter (élément de découpe) – et d’une nouvelle bande d’inviolabilité, ce nouveau bouchon attaché vient remplacer un bouchon deux pièces jusqu’alors utilisé, comme l’exige la directive (UE) 2019/904 sur les bouchons solidaires qui prendra effet au 1er juillet 2024. Grâce à son système breveté, son bord tranchant est spécialement conçu pour couper le trou pré-laminé avec un minimum d’effort. «Le 23-H PAK permet une ouverture facile et nette de la brique carton, sans endommager ni détacher aucune pièce du bouchon, ce qui le rend plus facilement recyclable. Sa fabrication a nécessité la mise en place de nouvelles presses, nouveaux moules et lignes d’assemblage sur ce hall», détaille le responsable de l’usine. Solution prête à l’emploi, le 23-H PAK s’intègre facilement à toute ligne de remplissage sans adaptation préalable, selon United Caps. Fort de son succès, une version aseptique du H-Pack voit le jour en diamètre 23 et 27 à destination du secteur laitier.
Innover par le biais de la durabilité
En s’appuyant sur un outil industriel conséquent (217 presses de 50 à 650 tonnes, 53 machines d’assemblage et 21 lignes d’impression au total), United Caps a su se forger une image d’expert de la pièce plastique injectée pour fermeture, bouchon et couvercle, à quelques exceptions près comme pour les capsules café ou les mesurettes pour lait en poudre. «Nos produits ont des contraintes et fonctionnalités que doivent prendre en compte nos équipes R&D basées à Messia-sur-Sorne en France dans tout nouveau développement. Heureusement, il reste encore des évolutions technologiques possibles sur le choix des matériaux, l’optimisation des moules, les procédés de production ou encore l’étape post-molding», confie Benoit Henckes. La RSE oriente d’ailleurs fortement les choix du fabricant luxembourgeois dans ses projets et derniers concepts. «Notre objectif est de proposer des bouchons fabriqués à partir de 100% de plastique renouvelable ou de plastique recyclable», annonce Rony Van Regenmortel, responsable durabilité à la direction d’United Caps. Pour quantifier les efforts d’éco-conception réalisés sur les références de son portefeuille, l’entreprise a mis au point l’outil de calcul d’ACV baptisé GaBi (émissions carbone, eau, acidification des sols, etc.). «Il permet de suivre les initiatives prises pour améliorer le profil de nos produits. Pour accompagner cette démarche, toutes nos usines tournent depuis un an à l’électricité verte. D’autres investissements ont été déployés pour décarboner davantage encore nos sites : remplacement de machines hydrauliques par des modèles électriques, installation de systèmes de refroidissement des lignes et de panneaux solaires quand cela est possible», complète Rony Van Regenmortel.
Allégement, bouchons attachés et ressources biosourcées
Plusieurs derniers lancements privilégient la voie de la réduction du poids du bouchon. A l’instar de Kindcap, un couvercle pour boite de lait infantile, fabriqué à partir d’un mélange unique de résines PP qui utilise moins de plastique dans le processus de production. Moins coûteux que les bouchons en PE traditionnels et plus flexible, le Kindcap facilite l’ouverture sans distorsion de forme. Couvercle le plus fin et le plus léger du marché (-35% de gain de poids) selon son fabricant, il ne nécessite que peu ou pas de modifications des lignes existantes et affiche une vitesse de bouchage maximale de
510 bouchons par minute pour le 99 Kindcap (4,15 g) et de 320 bouchons par minute pour le 127 Kindcap (7,2 g). Autre illustration avec le New 29 Flip-on, 20% plus léger qu’un bouchon standard 29/21 CTC dédié aux huiles alimentaires. Avec un poids plume de 1,6 g et une bande d’inviolabilité qui reste attachée après ouverture, le bouchon s’utilise d’une seule main et permet de sécuriser le remplissage, le transport et la mise en rayon. Autre piste explorée : l’injection de gaz permet de diminuer la densité totale du bouchon. La technologie a été déployée lors de la production du bouchon WIP Mucell, pour un gain de 8% du poids initial. «Il est plus facile de travailler l’allégement d’une référence même si aujourd’hui, l’ensemble du secteur cristallise leurs efforts pour basculer leurs lignes vers des bouchons solidaires. Avec notre gamme de bouchons attachés UCTC, nous offrons un large panel de solutions adaptés aux besoins de chaque client. Il est tout de même intéressant de noter que les bouchons attachés sont en moyenne 30% plus lourds qu’un bouchon classique, ce qui est somme toute assez contradictoire avec les efforts d’allégement de notre filière», note Rony Van Regenmortel. En parallèle, la recherche de résines biosourcées – «biobased ou drop-in biobased» issues d’un feedstock de 2e génération – se développe tout comme la recherche de PE/PP de grade alimentaire par la voie du recyclage chimique.