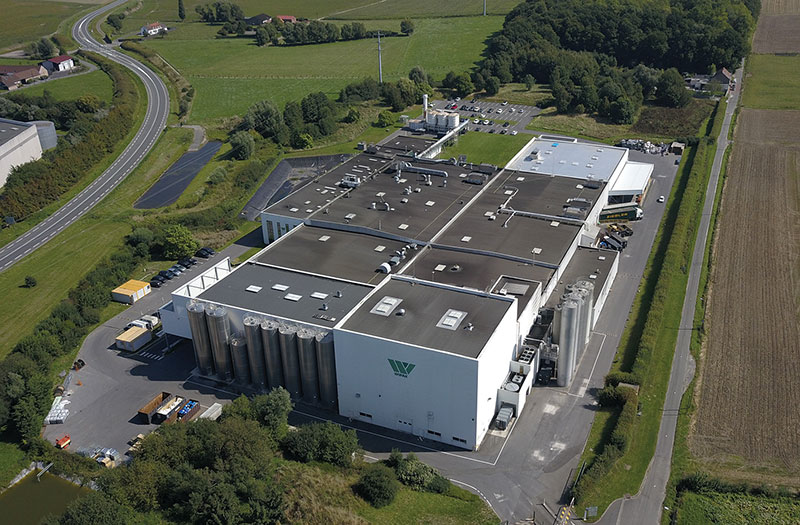
Wipak démarre sa nouvelle ligne d’extrusion à Bousbecque
publié le vendredi 31 mai 2024
Abonnez-vous à la revue pour lire la suite de l'article
s'abonner
Après plusieurs mois de travaux d’extension, Wipak Gryspeert – filiale française du groupe Wipak – met en route sa nouvelle ligne d’extrusion baptisée Green Cast sur son site de Bousbecque près de Lille. D’une capacité de 8000 tonnes par an, l’outil deviendra à terme la ligne de choix pour la production de la gamme de films Green Choice. Explications.
Le groupe finlandais Wipak (CA de 1,2 Mrds € et 4200 employés dans le monde) – dirigé par la 2e génération de la famille Wihuri – affiche un savoir-faire de 50 ans dans la fabrication de films multicouches pour les emballages alimentaire haut de gamme (Wipak) et les produits médicaux technique (Wiicare). Avec l’ambition affichée de devenir l’entreprise d’emballages flexibles la plus durable au monde en atteignant rapidement une neutralité carbone. Pour ce faire, le fabricant a choisi d’équiper son usine française de Bousbecque, dans le nord de la France, d’une nouvelle ligne extrusion Green Cast, qui sera dédiée à terme à la production de films recyclables de la gamme Green Choice. Celle-ci rassemble trois types de produits : les films renouvelables qui intègrent les papiers stratifiés plastique très demandés en Allemagne, en Espagne et en France ; les films plastique incorporant du recyclé mécanique ou chimique ; et enfin, les films recyclables mono-matériaux PP et PE répondant aux nouvelles exigences réglementaires. «Si nous sommes techniquement prêts pour proposer à nos clients des solutions recyclées, la question de la disponibilité de la matière avec un contact alimentaire et son approvisionnement reste actuellement un frein à leur déploiement. Quant aux films recyclables, ces solutions mono-matériaux sont d’ores et déjà disponibles et nous sommes prêts pour cette transition. En 2022 déjà, nous avions été récompensés par un Oscar de l’Emballage pour notre sachet 100% PE développé pour le gruyère râpé de Paysan Breton. Notre nouvelle ligne Green Cast est l’illustration même de notre engagement à accélérer vers la production de ces films recyclables», explique Franck Hancard, directeur commercial de Wipak Gryspeert (CA de 85 M€ et 210 salariés).
Une nouvelle ligne d’extrusion taille XL
Sur le parc de 11 usines du groupe Wipak, seuls trois sites ont des capacités d’extrusion, à savoir ceux de Nastola en Finlande, de Walsrode en Allemagne et de Bousbecque en France. Après 27 ans de bons et loyaux services, l’ancienne ligne Ultra Cast – d’une capacité de 1000 tonnes par an – laisse place à un mastodonte : la Green Cast. Avec 8000 tonnes de films par an et des laizes pouvant atteindre 2,90 m contre 1,40 m sur la précédente extrudeuse, la nouvelle ligne fournie par le constructeur américain Davis Standard fait passer Wipak Gryspeert à une autre échelle. «Nous allons nous orienter clairement vers de gros volumes de production avec cet outil», confie le responsable des ventes. S’élevant sur trois niveaux, la Green Cast impressionne par sa taille. Au premier étage, s’aligne en cercle une dizaine de blocs de dosage de résinesqui viennent alimenter au niveau inférieur 13 vis à extrusiondont deux doubles vis dédiées aux granulés de plastique issus des déchets de l’usine. Le polymère à l’état fondu à travers une filière est extrudé à plat puis étiré et refroidi sur des rouleaux thermostatés. Pour alimenter la «bête», deux silos supplémentaires ont été ajoutés à l’extérieur de l’usine pour stocker les granules plastique. «Nous avons profité de l’arrivée de la nouvelle extrudeuse pour revoir l’ensemble de notre process et de nos flux de production. Intégrer nos rognures de découpe pour les rebroyer et les réinjecter dans la procédé de fabrication en circuit fermé a demandé beaucoup de travail à nos équipes. Mais aujourd’hui, nous sommes fiers d’atteindre notre objectif de zéro déchet», précise Franck Hancard. Formés sur les sites de Nastola en Finlande et Walsrode en Allemagne, les opérateurs de Wipak Gryspeert ont pu rapidement prendre en main la nouvelle extrudeuse, opérationnelle depuis quelques semaines. Elle vient ainsi compléter un parc déjà bien équipé en solutions connexes, à savoir trois lignes de coextrusion Blown 7, 8 et 9 couches pour la production de films pelables, scellables voire refermables pour les sachets repack, des films haute barrière EVOH et des films coextrudés PA/PE/PP/EVOH (capacité de 11 000 tonnes) et une ligne de coextrusion pour les produits APET d’une capacité de 5000 tonnes.
Une extension de l’usine en complément
L’arrivée de la ligne Green Cast a été l’occasion de repenser l’organisation des flux et a mis en évidence le besoin d’agrandissement de l’usine de Bousbecque. Une extension de 1500 m² a été ajoutée à la superficie initiale du site afin d’accueillir, en complément à l’extrudeuse, une zone de stockage additionnelle et d’autres équipements dont des nouvelles machines de découpe et une fin de ligne automatisée. Au total, pas moins de 18 millions d’euros auront été investis par Wipak pour ce projet, avec l’aide de l’Etat français et de l’Union européenne. «Après le premier pôle extrusion où se trouve la ligne Green Cast, nous avons pu revoir avec l’extension nos autres pôles, en ayant désormais des espaces dédiés à la découpe/lamination, la réticulation des films, l’impression des films ou encore au conditionnement des bobines», décrit Franck Hancard. L’arrivée de deux machines de slitting supplémentaires fait passer désormais à 140 millions de m² la capacité de découpe de Wipak Gryspeert. «La manipulation des bobines semi-automatique par deux nouveaux bras robotisésa été fortement apprécié par les opérateurs, dont les conditions de travail ont été améliorées. Le but sera de généraliser l’utilisation de ces robots sur l’ensemble du hall de découpe», ajoute Laura Zelus, chargée des ressources humaines et de la communication chez Wipak Gryspeert. Toujours dans la continuité de réduction des TMS (troubles musculosquelettiques) de ses équipes, une fin de ligne automatisée a également été mise en place. Les bobines filles de films plastique ainsi coupées et préparées sont houssées individuellement avant d’être palettisées puis fardelées par des robots Fanuc mis en place par l’intégrateur italien Trascar.
Personnaliser les films par impression
La moitié des ventes de Wipak Gryspeert concerne les films imprimés. Doté d’un service graphique pour la création et la validation des visuels et d’un département des encres pour l’analyse colorimétrique et le mélange sur place des couleurs, le site fournit les marques agroalimentaire en films imprimés. Pour ce faire, deux machines d’impression en flexogravure – l’une en huit couleurs, l’autre en dix couleurs et laminage en ligne – offrent une capacité annuelle de 54 millions de m². En complément, une ligne d’impression par rotogravure neuf couleurs continue à tourner. «Si la machine est plus longue à préparer, elle apporte plus de nuances dans certains dégradés, et s’avère encore très utile pour certaines impressions. Même si nous réfléchissons à l’option de presses digitales qui pourraient nous apporter de la flexibilité pour les petites commandes», confie Franck Hancard. Une fois imprimés, les films passent ensuite sur deux machines de laminage avec ou sans solvants et transitent dans un espace de réticulation des bobines durant 24 à 48h afin que le film substrat et le film supérieur finissent leur complexage. Les films ainsi produits sont dédiés aux marchés des viandes et de la salaison, de la boulangerie (pain précuit), des fromages à pâte dure et râpés, des fruits de mer et poissons, des plats préparés, du snacking et des soupes. «Wipak est reconnu pour ses films plastique techniques à haute valeur ajoutée capables de conserver des produits complexes. Nous nous adressons à des secteurs où les attentes en conservation et en effet barrière sont fortes. Rendre ces emballages vertueux sans faire de compromis sur ces propriétés est un défi d’autant plus intéressant à relever», explique le directeur commercial. Confiante en l’avenir, la filiale française a encore «sous le coude» une superficie de 1000 m² pour décider de futurs investissements afin d’accompagner au mieux le marché.